In the middle of the composite materials world, pre-impregnated materials, simply pre-pregs, could be a pinnacle of engineering innovation. In short, these materials act as the key to unlocking such industries’ potential by providing unparalleled high-strength, low-weight, and robust materials like dielectric material to the copper layers and copper foil.
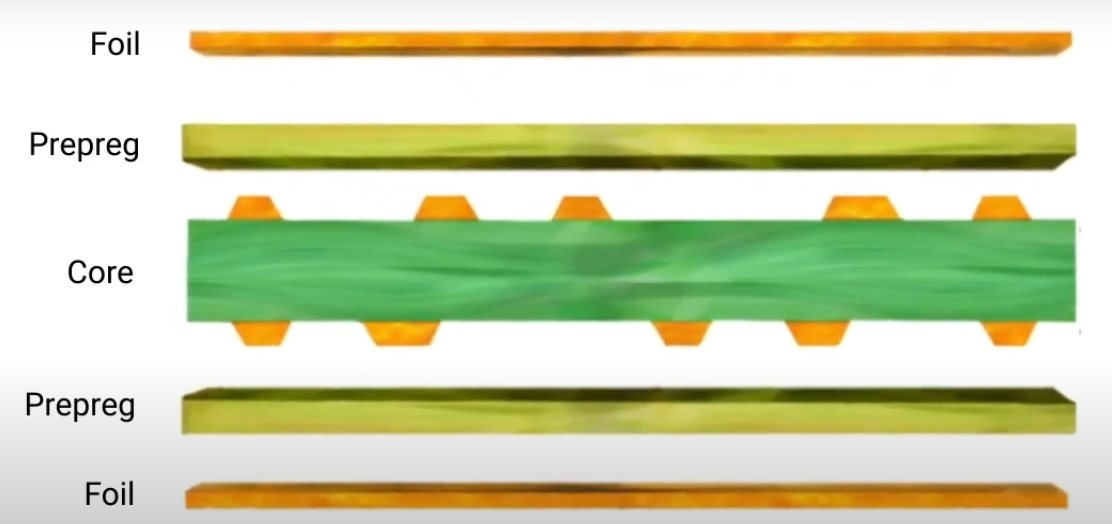
This blog deals with the concepts of pre-preg materials, classified as thermoset plastics, their manufacturing processes like injection molding or tape laying, their applications, and the latest developments that are driving their evolution.
What is pre-preg?
Pre-preg means “pre-impregnated” composite fibers that use a matrix material, such as epoxy resin, which is already in place. The fibers, commonly carbon, glass, or aramid types of fibers, are fully saturated with a certain amount of resin, which is tacky or in a partially dry state, until they are placed into a mold for a complete curing process under a high temperature and pressure.
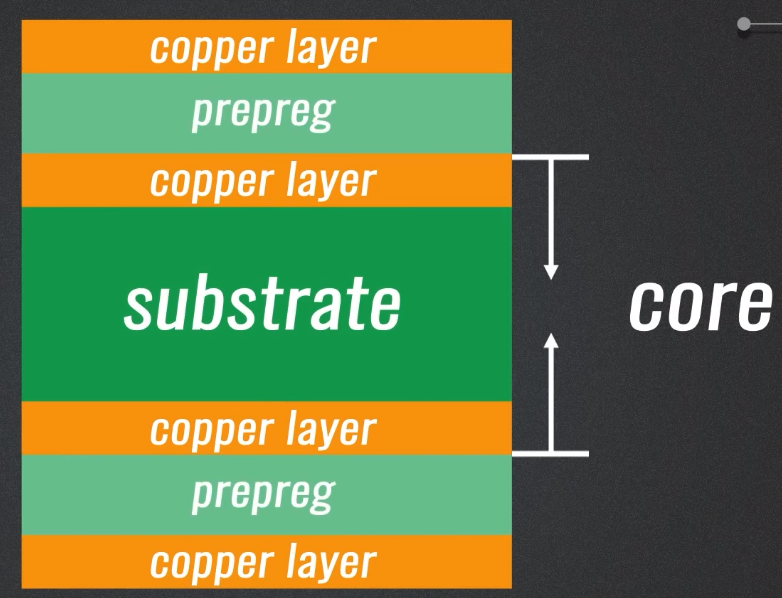
This precise impregnation makes sure that resin bonding agent is evenly applied, proper fiber-to-reinforcement ratios, and consistent mechanical properties are achieved throughout the entire composite structure.
Manufacturing Process of Prepared material
The manufacturing of pre-preg materials involves several sophisticated steps:
Resin Mixing: The resin formulation is the initial step that should done and composites should be mixed thoroughly. The most critical parameter will be for the selection of the resin, as it will determine the thermal and mechanical characteristics of the composite.
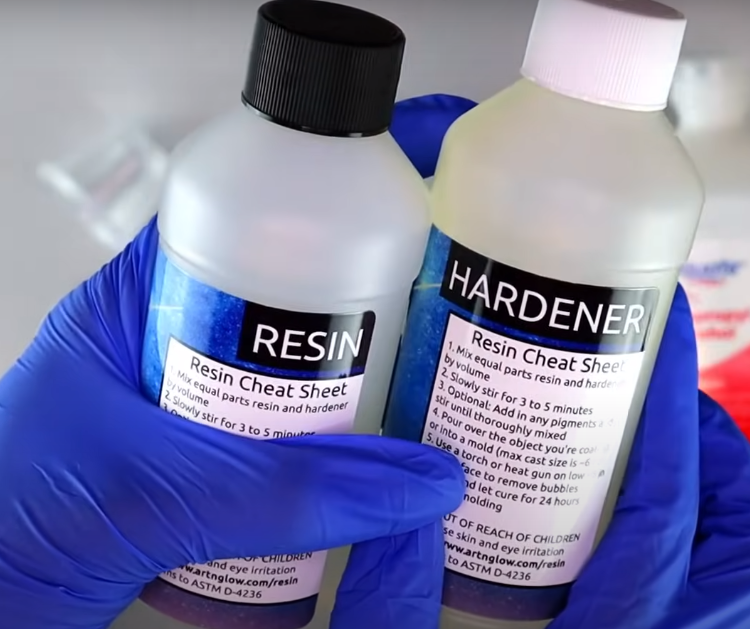
Impregnation: The fibers do not pass through a resin bath or a hot-Application process but are impregnated with liquids instead and every fiber gets coated equally.
Calendaring: The fibers as well as the resin deposited on them go through rollers that control the fabric pcb thickness and resin content.
Curing: The material partially cures (“B-staged”) so that it can be handled easily and cut. This phase is significant because it ensures key ingredients are preserved, thus providing convenience in using the product designed for lay-up.
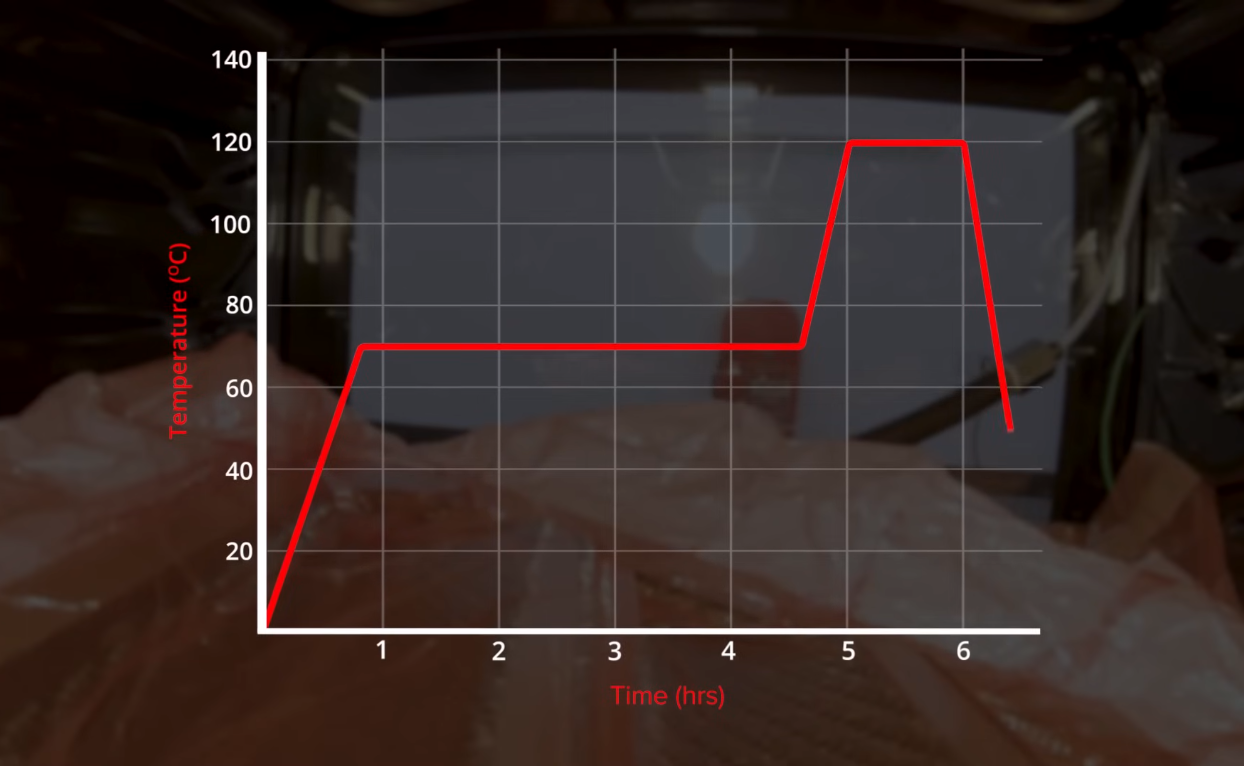
Types Of PCB Prepreg
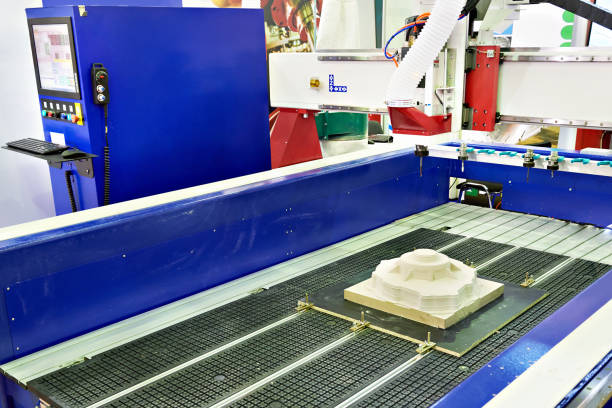
PCB prepregs are materials that function as assembly components in multilayer printed circuit boards (PCBs). In particular, they perform layering operations like copper layer and bonding operations for multilayer PCBs. Here are the main types of PCB prepregs, each with unique properties and applications:
Standard Epoxy Prepregs
These are the overall PCB types of prepregs mostly used in fabrication processes which have good thermal and electrical characteristics. This can be applied in so many arenas, in fact.
High-Tg Prepregs
These prepregs possess higher glass transition temperature (Tg) value as compared to the other prepregs. Therefore, they are more appropriate for high-temperature resistant applications, which give them better thermal and mechanical stability.
Low-flow Prepregs
With the aid of a weave pattern that limits the flow of resin in the lamination process. The concurrent layer is most suitable for applications where precise alignment of features is needed for example, in high-density Density Interconnect PCBs.
Halogen-Free Prepregs
Forming without halogenated compounds, these pre-pregs show no environmental hazards and are used in applications where cutting off the toxic emissions from combustion becomes crucial.
Polyimide Prepregs
High thermal stability, chemical resistance and mechanical properties are some of the factors that enable them to be used for hi-tech performance applications operating under pressure conditions.
High-Speed Digital Prepregs
For the specified RF pulses, these plies have low dielectric constants and low loss factors, which can be used for high-speed digital applications.
Applications in Industries
Pre-preg materials are extensively used in industries where structural integrity, copper thickness, and weight are critical.
Aerospace and Defense
e.g., structural components like wings, fuselage sections or even the inner cabin sections.
Automotive
Where in high-performance chassis, cars and structural members is this to be implemented.
Sports Equipment
These are walking sticks used in the fabrication of golf clubs, bicycles and racing poles, where minimizing weight without degrading strength is vital.
Wind Energy
Reusing it in the making of wind turbine blades so that these can not only fulfill all the mechanical needs but also withstand the stringent environmental conditions.
What Is the Difference Between Prepreg and Laminate?
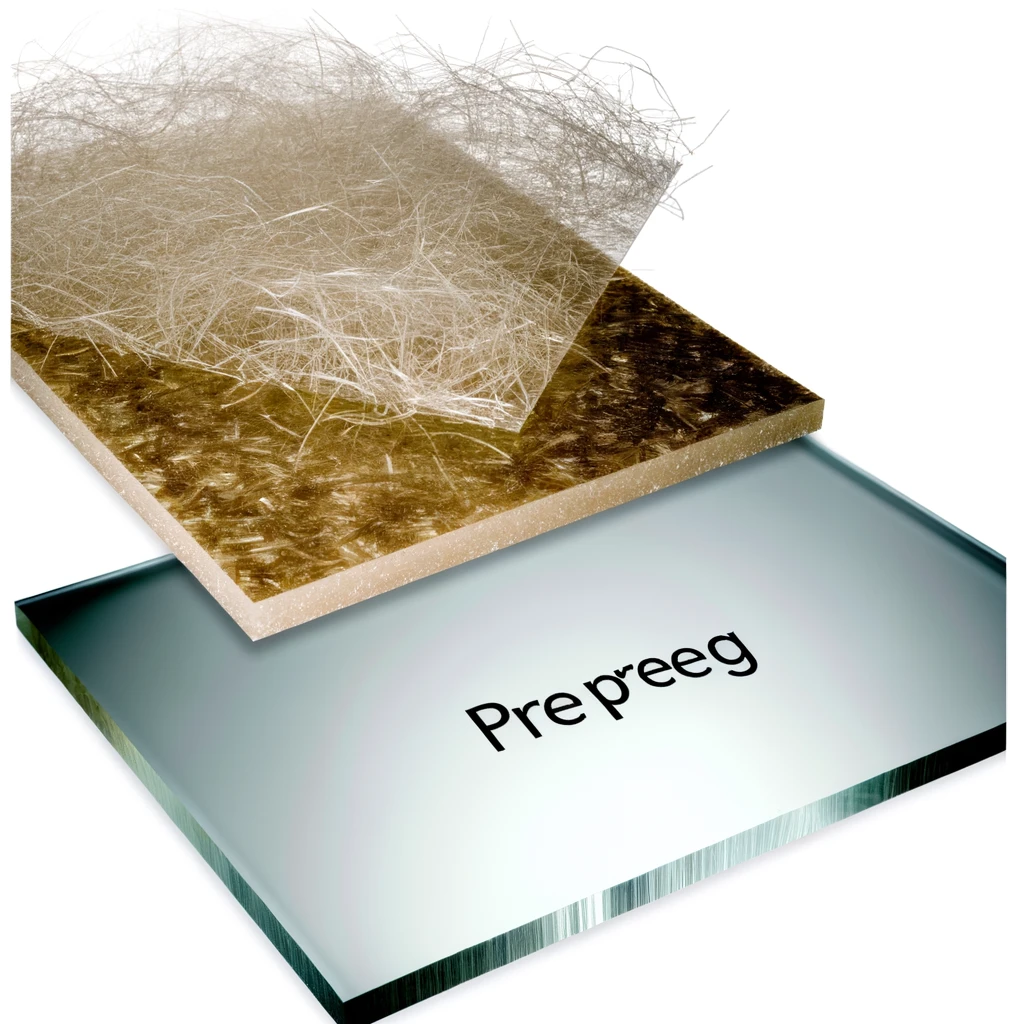
As a very widely used material in the molding of PCB, there are two essential materials: prepreg and laminate, which have crucial differences. Prepreg is known as the mist of these fibrous materials, like fiberglass or carbon fiber, impregnated with partially cured resin, such as epoxy. Lacking in elegance, it is a pro that guides the procedure of laminating layers by applying heat and pressure while compiling the PCB.
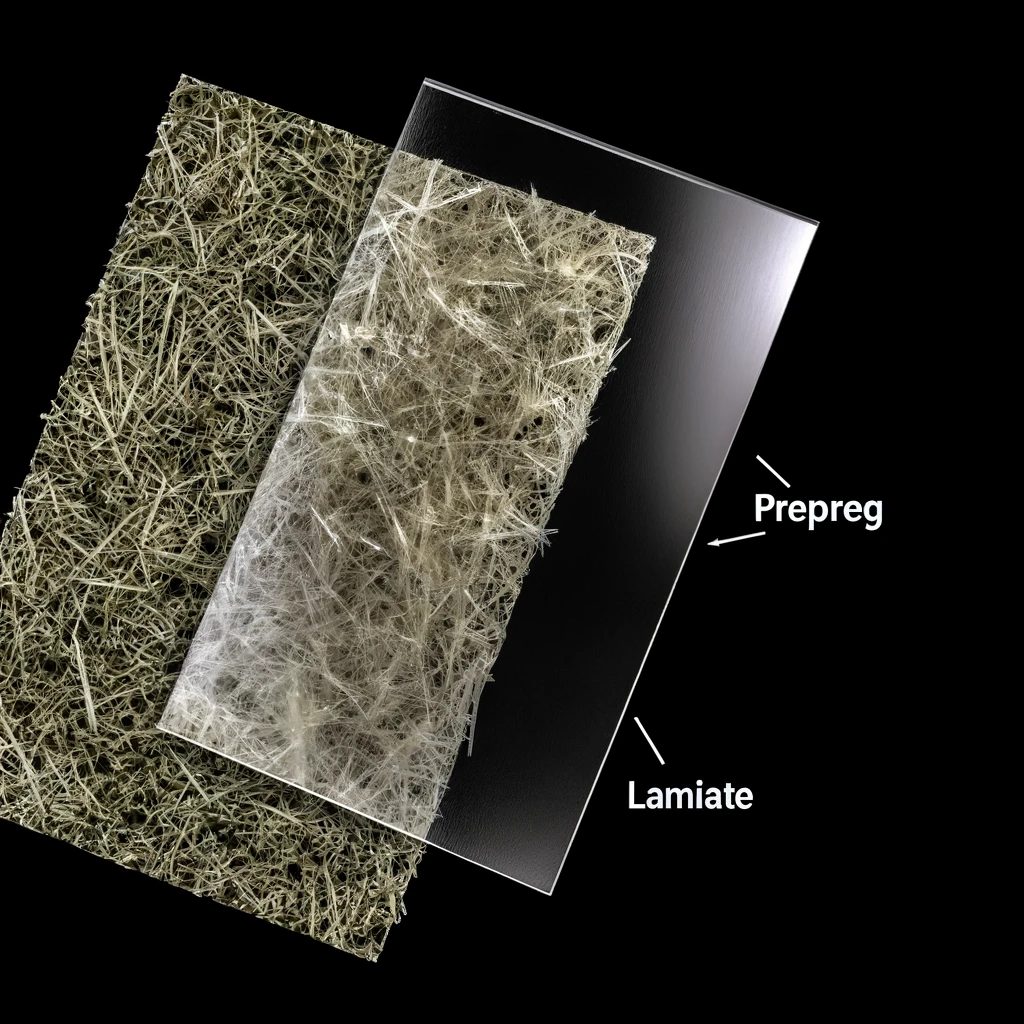
Laminates, or in some cases, thicker versions of sheets known as composite panels, consist of two cores of fiberglass cloth that have completely cured resin remains fluid. It consists of two rigid parts of PCB, which are the substrates on top of which components and electronic circuits are mounted. To an extent, prepreg is a sort of bonding medium between numerous laminate layers; laminate, on the other hand, gives the materials strength and is the surface used to place circuitry.
Why is prepreg important for multilayer PCBs?
Prepreg has become an essential element for multilayer PCBs since it is used as the adhesive layer between the laminates during the PCB manufacturing process that binds the separate sheets together. Its properties are essential for:
- Electrical Insulation: Prepreg layers provide not only thermal but also electrostatic isolation between the various layers of a PCB, so as to prevent electrical short circuits and support signal integrity.
- Thermal Management: It is a heat dissipation lanche processor that uses the general thermal stability of the PCB.
- Mechanical Strength: Prepreg is composed of resin and fiber, which are the main ingredients responsible for the mechanical strength of print circuit boards. The resin can cope with stress and environmental factors.
- Uniformity and Reliability: Prepreg offers the manufacturer the quality of unwavering thickness as well as uniform dielectric properties, which help the PCB perform well and be highly durable.
Properties Of PCB Prepreg
PCB prepreg has several key properties that make it ideal for use in printed circuit board manufacturing:
- Dielectric Constant: The dielectric constant is specific and is responsible for the electrical insulation effectiveness, and these channels influence signal transmission.
- Thermal Stability: Prepreg has its high temperature resistance, which makes such operations as soldering possible without degrading the board; additionally, the PCB’s operational stability is maintained.
- Mechanical Strength: It offers a structural support that helps to stand up against physical and thermal stresses during the operation.
- Chemical Resistance: Prepreg is an excellent option in relation to many chemicals for the properties of corrosion and degradation that last forever.
- Adhesive Properties: It possesses a remarkable adhesive strength that bolsters a strong layer-to-layer bonding between the varied layers of the PCB.
- Flexibility: The prepreg manufacturer has intact flex, which makes it possible for alignment during the stacking process.
- Thermal Expansion: Its controlled thermal expansion coefficient is very close to copper’s and laminate’s, and there is no expectation of laminate delamination or warping when this occurs.
Prepreg Testing
Prepreg testing is integral, as prepreg qualification assures the quality and consistency of prepreg materials prior to production run. Common tests include:
Resin Content Test
Defines the resin content of prepreg, which in turn determines the prepreg’s adhesive and insulating functions.
Flow Test
Characterizes the amount of resin that exudes from the pre-preg when it is heated to and squeezed by pressure; this is critical in understanding how the prepreg will respond during the lamination process.
Cure Test
Evaluates the degree of curing or staking of the resin to make sure that it is okay for storage and going through the next action.
Glass Transition Temperature (Tg) Test
Determines the temperature at which the resin starts to flow from a glass-like state to a semi-liquid one; the resin flow and its movement highly depend on the thermal condition.
Dielectric Constant Test
Ensures that it complies with the dielectric constant specification for the application, that involves both electrical insulation and signal integrity.
Tensile and Flexural Strength Tests
Check mechanical strength and flexibility of prepreg to make sure that it is possible for prepreg to bear mechanical stress when assembling and operating following PCB construction.
The Future of Pre-Preg
It is through ongoing studies and the production of nanotechnology and bio based resins that the opportunities in the pre-preg market sector will be redistributed. Inventions such as graphene-enhanced pre-pregs are now allowing wider access to composites with ultimate reduced weight, maximum strength and minimum environmental impact.
Material Analysis of Pre-Preg
Resin and fiber materials used in pre-preg will also be main components of this material analysis. The basic components of pre-preg as a rule are reinforcing fibres, such as glass-fibre, carbon-fibre, or aramid, being impregnated with epoxy thermo-setting resin. Analyzing resin contents, degree of curing and the distribution uniformity of the resin within the fiber matrix are the targets of the study. It also analyses the thermal-mechanical behavior, including the glass transition temperature (Tg), tensile strength, and flexibility. Moreover, from the stress-strain curve, the modulus of elasticity will be measured. The studies by the advanced methods of DSC (Differential Scanning Calorimetry) and TGA (Thermogravimetric Analysis) are more concerned with thermal properties, whereas the mechanical properties are assessed by tensile and flexural testing. This exhaustive analysis of material properties guarantees the validity of fiberglass fabric meeting the performance standards set for industries involving extensive reliability, such as the aerospace or automotive industries.
Prepreg In PCB Fabrication
PCB prepreg and its role is essential in the process of PCB fabrication, particularly when creating multilayer boards. It performs the bonding and insulation function, which holds together and interconnects these different multilayer printed circuit boards (Multi PCB) under heat and pressure. The prepreg thickness is made of glass fiber yarn saturated with resin, mostly epoxy, and placed between the board laminates in the course of the PCB slab with layer processing and copper foils. When the stack is subjugated with heat and force in a lamination press, the resin melts, spreads and cures, becoming a shardy, uniform solid structure. Such process not only assembles stack elements (layers) chemically but also provides electrical continuity and isolation for layers throughout the insulation process. Fibre epoxy prepreg choice, considered for its resin content as well as its use in hottest soldering and in other thermal testing requirements, affects everything from thermal management to electrical properties as well as overall board reliability.
Advantages of Pre-Preg
Here are the advantages of pre-preg, organized in an ordered list:
- Uniform Resin Distribution: This guarantees that mechanical as well as electrical responses are uniform across the composite.
- Reduced Voids and Defects: Makes the structure more uniform and guarantees longer lifespan by eliminating the air bubbles, leaving it smooth.
- Simplified Manufacturing Process: Make it possible to do without the resin mixing and applying process that requires human operators now and as a result, cut down on the labor costs and the possibility of errors being made.
- Precise Fiber-to-Resin Ratio: Beefs up the strength to the weight, an all-important factor in the functioning of high-performance equipments.
- Efficient Use and Storage: Insulating material can be saved at significantly low temperatures and consumed directly, resulting in less handling and waste.
- Improved Quality Control: This improves product quality because some things can be checked and corrected during the process of making them.
Disadvantages of Pre-Preg
While pre-preg materials offer significant advantages, they also come with certain disadvantages:
- Cost: The starting materials for prepreg, unlike other composite materials, are normally costly due to their high-end production processes.
- Limited Shelf Life: The preweighted resin is time-sensitive (its shelf life is limited) and requires refrigeration to avoid premature curing, which can add to the cost of storage and home handling.
- Limited Process Flexibility: Although resin curing would be a permanent process, it cannot be reversed so that when the resin becomes a hardened final product, it is no longer possible to change any ingredient or fiber in order to achieve the desired design.
- Specialized Equipment Required: The fact that you need to have autoclaves or heated presses for the curing process may be one of the reasons why a start-up company would have to spend more money for the initial setup and operation.
- Waste: Many material cut-offs and excesses cannot be relied upon to be close to 100% re-usability, whereas in other methods like wet layup, there should be a higher level of left-over resin capable of being used somewhere else.
Challenges and Solutions of Pre-Preg
Though pre-pregs have many advantages, they also possess some difficulties, which include compromised shelf life and the necessity for a deep freezer. Material science advancements have resulted in the creation of OOA pre-pregs, which can be put through low temperatures and have longer shelf-life storing characteristics. This, in turn, is contributing to overcoming the problems created by the high temperatures.
Conclusion
Among the first materials to be used in composite technology is prepreg core material, such as core and copper foil, that is built on superior characteristics and therefore can be employed in different special industrial applications. As technology develops, the range of opportunities for prepreg increases, and they are gaining importance in material science pursuits. Through the adoption of such upper-grade materials, manufacturing companies can make the most of the increased efficiency, sustainability, and cost-effectiveness of their products.
This deep dive into the world of pre-preg materials showcases their significance and transformative power in modern manufacturing, truly living up to the blog’s title, “Layered Precision: Almost a Peel Back on the Power of Pre-Preg in Composite Manufacturing.