The printed circuit board forms the backbone of any modern electronic equipment, from wireless devices and smartphones to sophisticated medical equipment. At the center or heart of this very complex board is a structure made of varied materials, all coordinated to serve one purpose: overall functionality and performance of the board. This is the PCB core, which is the fundamental material to build up everything else in the PCB; above it, there are the prepreg materials and multiple layers to constitute the PCB. Anyone working in the design and manufacture of electronic devices will know how important it is to get a good understanding of the difference between PCB core and prepreg materials. This article describes these materials in terms of characteristics, application, and significance in order to provide a wide view of all the resin materials’ role at the very heart of a PCB.
What is Prepreg material?
Prepreg is a conductive dielectric material, and it is used in providing the desired insulation layer between mold surface of the copper and the core of the PCB. It is a dielectric material that is placed sandwiched between copper layer and (2) cores or between a core and copper foil (1). Broadly speaking, it is termed as the binding material since it does the combination of two cores or a core and a copper foil.
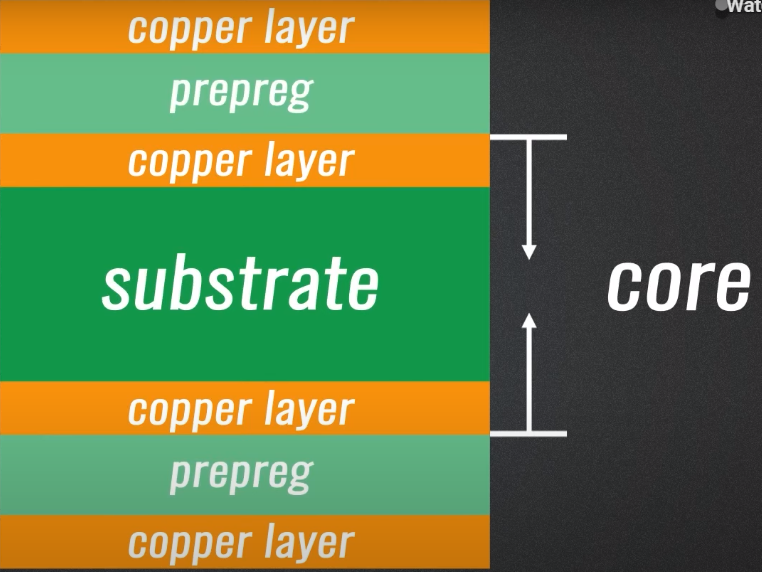
As its name suggests, prepreg is a glass fiber that has been impregnated with a resin bonding agent resin. All prepreg resin using material are known as B stage materials. Found in several types, depending upon their material thickness and the resin content amount of resin bonding agent resin content in all the resin, that they carry prepreg resin using material are very broadly available in 3 formats, depending on their resin content:
- Standard Resin
- Medium Resin
- High Resin
A Typical Prepreg Preparation Process Includes:
- Reinforcing with Resin
- Excessive resins removing
- High and low curing preparation
Why Prepreg material is important?
Prepreg —short for “pre-impregnated”—is a formal term for one of the raw materials used in the manufacture of PCBs. Technically, it refers to carbon fiber or glass fiber, or to woven carbon fiber or glass fiber/glass cloth that has been pre-impregnated with a resin system. This material holds importance to PCB fabrication for a few reasons:
- Structural Integrity: The prepreg in a multilayer PCB bonds the core layers with the copper foil into a sandwich-type structure and provides the bonding strength between the substrates to maintain the structural integrity of the PCB.
- Electrical Insulation: Prepreg material have very good electrical insulation properties. They prevent electrical interference and crosstalk between conductive layers, which is important for the integrity of the signal within complex circuits.
- Thermal Management: The resin helps in heat dissipation and thus aids to dissipate the thermal effect generated by electronic components. More efficient thermal management is, in turn, more essential for high-speed or strongly reliable electronic devices operating in harsh environments.
- Flexible in Design: Prepregs allow for multilayer PCB fabrication, and therefore, more complex and dense designs can be made possible. This is especially important to consider when looking at gadgets that are meant to satisfy a lot of functions all within the constraints of very minimal space.
- Customization: This will allow the use of different types of prepreg materials to obtain some specified characteristics and requirements, such as high-frequency performance, low dielectric material, or better mechanical properties. This is probably more possible with respect to the intended application on PCBs, for example.
- Cost Efficiency: Manufacturing of PCBs can be cost-efficient when the prepreg is used as compared to the rest of the methods. It makes the lamination process easier, consequently reducing time and costs for the production and maintaining high standards of quality.
In brief, prepreg is the most critical ingredient in the PCB manufacturing recipe to obtain mechanical strength, electrical performance, thermal management, design flexibility, and cost-effectiveness properties of the final product. Its role is very important for providing reliability and efficiency throughout the operation of modern electronic devices.
What is PCB core material?
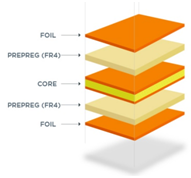
PCB core are effectively one or more prepreg laminates. PBCs are also composed of a core material that performs a fundamental function for the board since it is the substrate on top of which the copper layers and all the other components that make up the board are added. The role of core in the operation of the board is to support the structure of the board as well as act as means of electrical insulation layer for the board. A closer look at PCB core material and its significance is provided below:
Material composition of the PCB core
Typically, a stiff, insulating substrate constructed of one of the following materials makes up the core material of a PCB:
FR-4: An epoxy laminate reinforced with glass, FR-4 is the most often utilized core material. It provides a good mix of thermal stability, moisture resistance, electrical insulation, and strength.
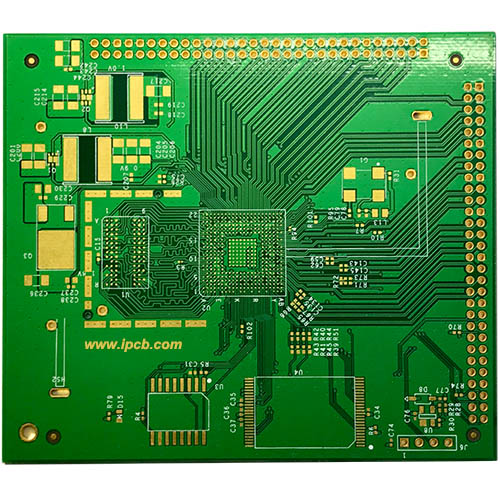
Metal Cores: Copper or aluminum cores can be utilized in applications that call for improved heat dissipation. These are frequently seen on LED or high-power PCBs.
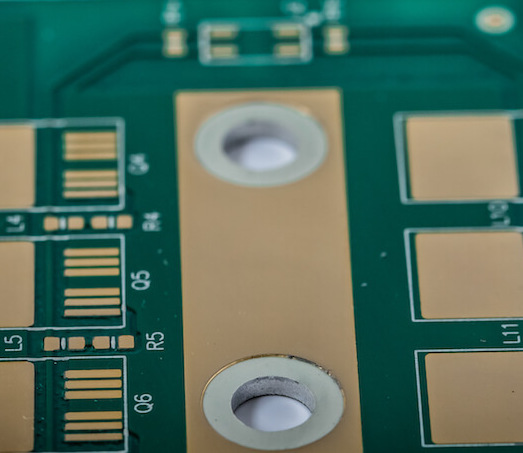
Polyimide: Known for its superior thermal and chemical resistance, polyimide cores are used in flexible PCBs, enabling more intricate and long-lasting designs.
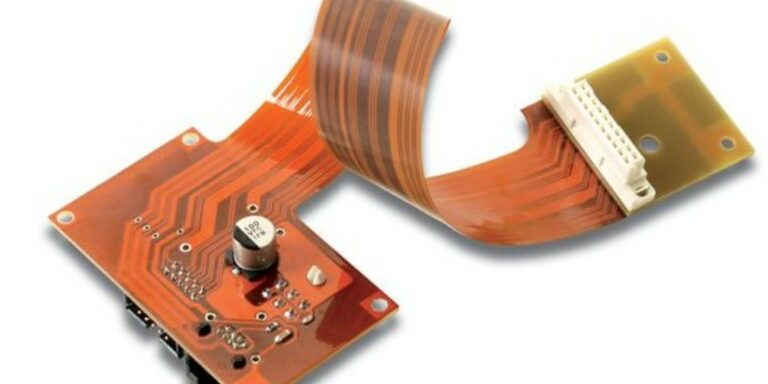
The PCB Core Material’s Functions
- Structural Support: The PCB can resist handling during production and usage because the core gives it the required rigidity and mechanical support.
- Electrical Insulation: It maintains signal integrity and prevents short circuits by electrically isolating the conducting layers from one another.
- Thermal Management: To ensure the longevity and continued functionality of the PCB, certain core materials, especially metal cores, aid in the dissipation of heat produced by electronic components.
- Dimensional Stability: The PCB’s dependability and accuracy depend on the core material’s ability to hold its size and shape in a variety of environmental circumstances.
PCB Core Structure Types
- One or two conductive layers layered on each side of a single core layer make up single-sided and double-sided PCBs. They are employed in less complicated applications and are simpler.
- Multilayer PCBs: These consist of prepreg and core layers and multiple layers of conductive material. These PCBs have a core that is positioned in between the layers, giving complicated and high-density designs a strong foundation.
The Value of PCB Core Materials
The performance, dependability, and longevity of the PCB are directly impacted by the selection of core material. Important things to think about are:
- Thermal Properties: For applications where there is a lot of heat generation, high thermal conductivity cores are necessary.
- Electrical Performance: The PCB’s impedance control and signal transmission are influenced by the dielectric characteristics of the core material.
- Mechanical Strength: The core must not break or distort when subjected to mechanical pressures during production and use.
In summary, the foundational component that has the biggest impact on a printed circuit board’s overall performance and usefulness is the PCB core material. To guarantee the best possible performance and dependability, it must be carefully chosen and matched to the unique needs of the electronic application.
PCB Core vs. Prepreg – What’s the Difference?
Laminates and PCB cores are comparable and distinct in certain aspects. Your core is essentially one or more prepreg laminates that have been heated, pressed, hardened, and partially cured together. Copper foil is then coated on both sides of the core. A full resin flow is infused into the prepreg material; the excess resin is toughened but not fully cured. When two cores are placed on either side of a prepreg laminate, the excess resin starts to bond to the surrounding layers when the stack is exposed to heat. This is how most manufacturers refer to the prepreg resin flow as the glue that ties core materials together. The crosslinking process of the hardened excess resin gradually cures it, bringing its final material qualities closer to those of the core layers.
A glass fiber weave is enclosed in the resin material, and the glass weave is made in a manner somewhat similar to that of threads. Using a loom, the glass weave can be made very tight (7628 prepreg, for example) or loose (1080 prepreg, for example) throughout the manufacturing process. The electromagnetic properties of resin content flow freely the yarn, which are then in charge of dispersion, losses, and any fiberglass epoxy laminate weave effects observed by signals in the board, are determined by any gaps in resin flow, excess of resin content, and the overall homogeneity of resin content ratio the yarn.
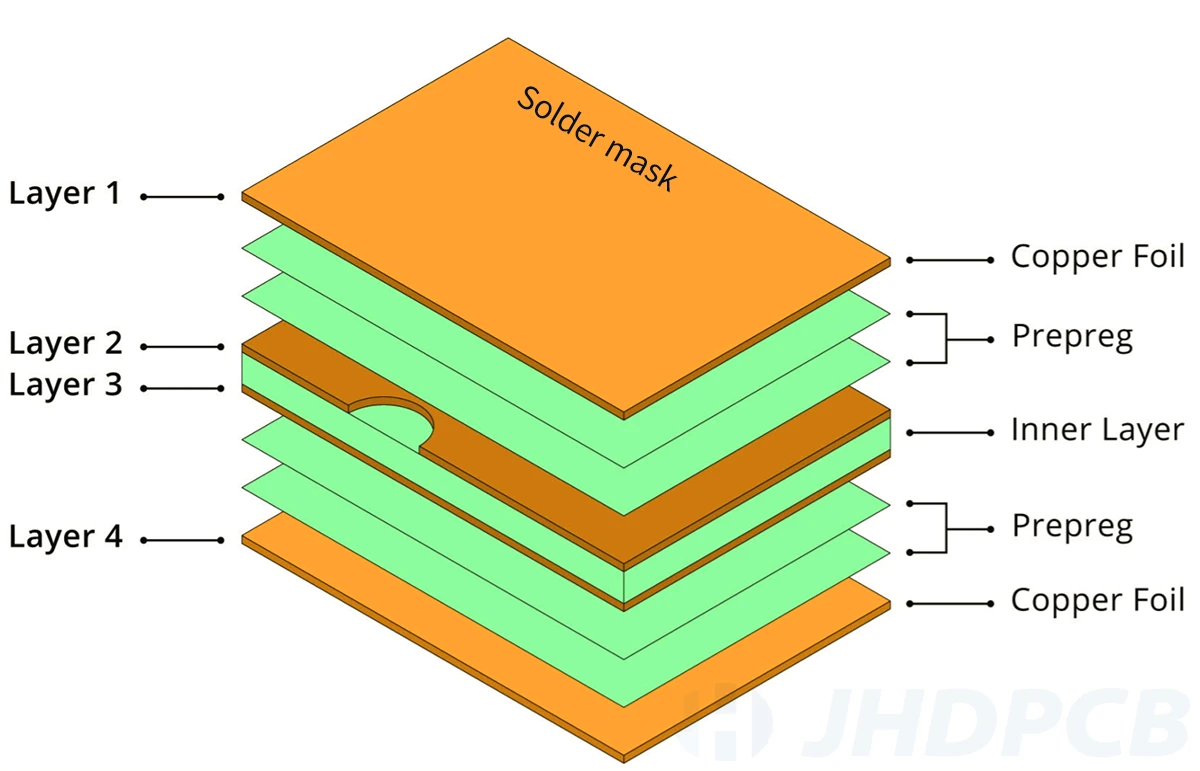
The dielectric constants layer thickness of prepreg and PCB core materials might vary slightly based on the kind desired thickness, amount, and weave of the glass. Because the effective dielectric constant that a signal on a track sees varies on the dielectric constant constants composite materials.
The desired thickness of the surrounding materials, this can be an issue for designing boards that require highly exact dielectric constant and impedance matching. It is challenging to anticipate precise dielectric constants and losses in a connection due to the incompatibility of some prepreg and core materials, as well as the existence of core/prepreg stacks with significantly varied dielectric constants (see below).
At high voltage, creepage and leakage current are issues with any PCB core or prepreg material. One explanation for the creepage requirements for FR4 materials is the electro migration of copper and the ensuing formation thermal expansion of conductive filaments. In order to address this issue and raise the glass transition and decomposition temperatures, non-dicyandiamide (non-DICY) resin remains fluid were substituted in FR4 cores and laminates. In comparison to DICY resins, phenolic resins offer higher glass transition and decomposition temperatures as well as greater insulating resistance upon complete heat curing cycle.
Materials for lamination process of PCB
Several materials are used in the process to PCB laminate production to produce a sturdy, multi-layered structure. Every material has a distinct function in maintaining the electrical performance, temperature control, and mechanical stability of the PCB. The following are the main components that go into the lamination process:
Prepreg
Prepreg, also known as pre-impregnated material, is a composite made of fiberglass cloth that has been woven and covered in a resin system, the resin content usually being epoxy resin. During the lamination curing process, it is tacky and sticky because it has been partially cured in resin ratio or fully cured typically epoxy, in excess of resin content (B-stage).
Epoxy, polyimide, and BT (bismaleimide triazine) resins are the different types of resin systems.
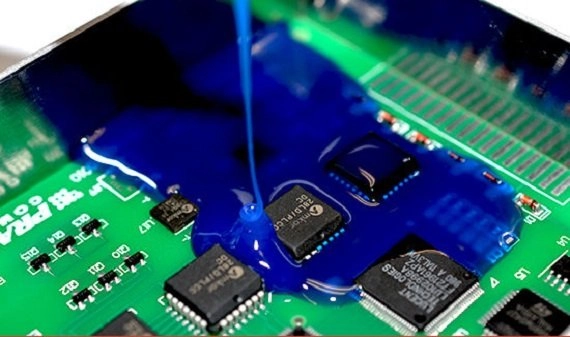
- Properties: Good electrical insulation, mechanical strength, and thermal stability. Depending on the required loss tangent (Df) and dielectric constant (Dk), several prepregs can be selected.
Copper Foil
The conductive pathways of the PCB are created by laminating copper foil onto two copper layers each of the prepreg and core layers.
- Copper foil that has been electrodeposited (ED) is frequently utilized due to its excellent adhesion qualities and affordability.
- For applications needing superior performance at high frequencies and high flexibility, Rolled Annealed (RA) copper is the preferred material.
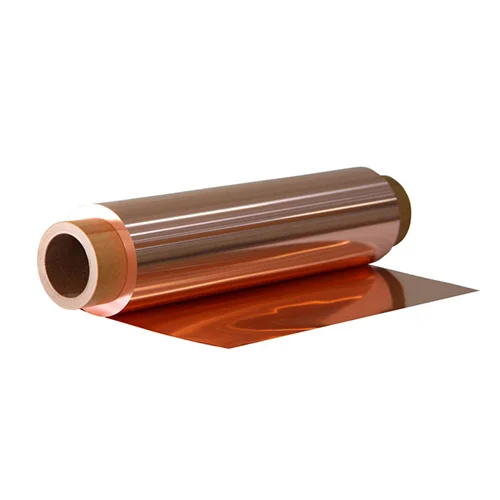
Solder Mask
Solder-mask is then adhesively applied the same layer thickness as core and copper foil and outer layers of the PCB to protect the core and copper foil traces and to prevent solder bridges from forming during assembly.
Epoxy Liquid Solder Mask: Market 1: This is the most basic type offering decent protection and insulation.
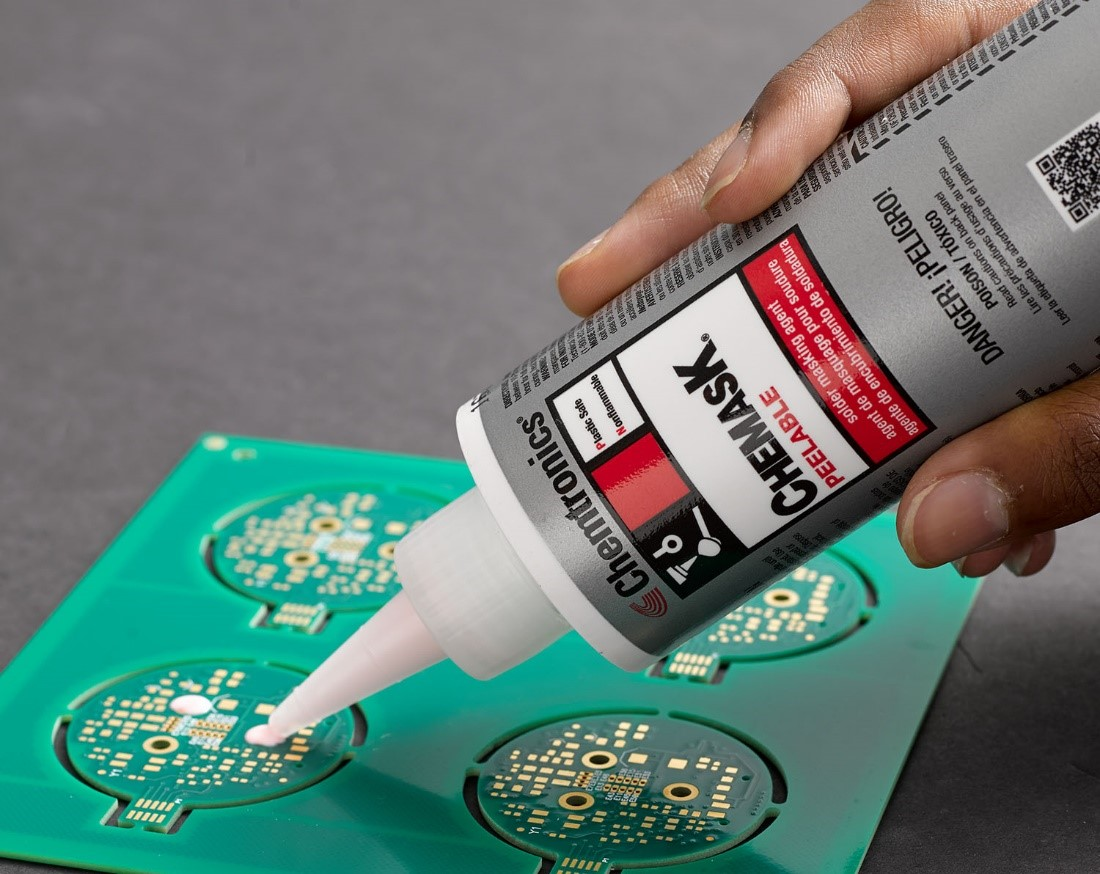
Liquid Photoimageable (LPI) Solder Mask: Enhances the accuracy required when engineering fine-pitch parts.
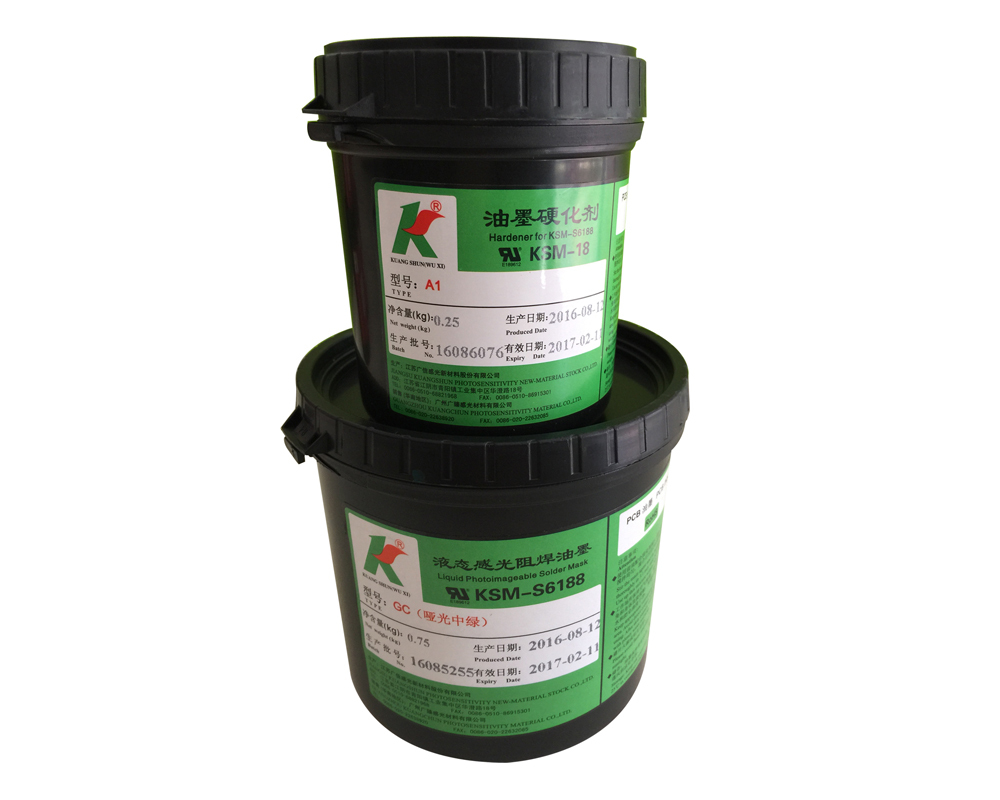
Coverlay
The solder mask does not have to be used in flexible PCBs since a coverlay is applied. It is made up of copper layer and a polyimide film over the copper layers to which a layer of adhesive has been coupled.
Polyimide Coverlay: Is an outstanding choice due to its ability to exhibit thermal and electrical stability for flexible circuits.
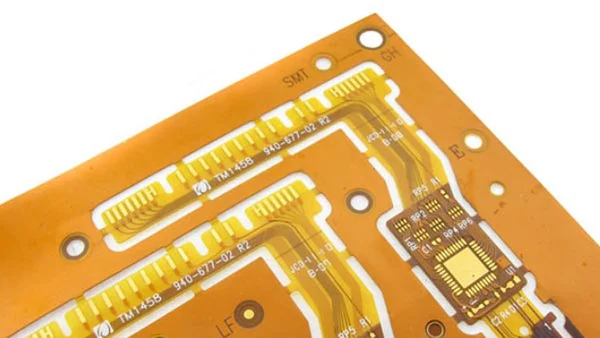
Adhesive Sheets
In some types of PCB constructions adhesive sheets are used to connect two copper layers together in the construction when these are manufactured for flexible PCBs or in order to connect copper layers to stiffeners.
- Epoxy Adhesives: Ideal for their adhesiveness and thermal performance capabilities.
- Acrylic Adhesives: run on the ability and water resistance of these flooring.
Factors to Choose the Lamination Materials.
Electrical Properties
- Dielectric Constant (Dk): Dielectric constants of low value are preferable when there are to be used for high frequency systems to avoid signal delay.
- Loss Tangent (Df): A low loss tangent is also as important for high-frequency circuits because a high loss tangent reduces signal quality.
Thermal Properties
- Glass Transition Temperature (Tg): Both para- and ortho-toluidines were used to develop materials having higher phase transition temperatures for their use in applications where high temperatures are involved.
- Thermal Conductivity: It is important to identify materials that are able to conduct heat efficiently especially in the power electronics system.
Mechanical Properties
- Tensile Strength: The capacity of the material to sustain forces without transforming the shape and size.
- Flexural Strength: Pliable and hard-flexible PCBs need to sustain flexural action.
Chemical Resistance
- Moisture Absorption: Despite having low moisture absorption characteristics, the humidity of the environment should not affect the electrical properties of the PCB.
- Chemical Resistance: The inability of chemicals used in the manufacturing process and during the operational life of the PCB fabricated to exhibit inhibitory or biocidal properties.
Cost and Availability
- Material Cost: Cost of performance is a critical issue for such companies like semiconductor manufacturers that are engaged in the production of consumer electronics.
- Availability: Overcoming the challenges in the supply chain of the raw materials to maintain production continuity.
Compatibility with Manufacturing Processes
- Lamination Compatibility: It should also be possible for materials to be compatible with chemicals and machinery used in producing laminated products.
- Processing Temperatures: Materials to be processed should also follow the temperatures used in the processing with the ability to enable manufacturing equipment.
The types of material used for lamination purpose in the manufacturing of PCB are of great importance in the aspect of performance, reliability and cost of the boards. If the manufacturer knows the value of electrical, thermal, mechanical, chemical properties and cost as well as the availability, he can produce PCBs of quality that best suit the needs of the application.
Conclusions
It is therefore important for people involved in the production of printed circuit boards to acquire information that enlightens them about room temperature and curing process and the application of heat and the cure temperature at room temperature to the PCB core and prepreg material. This product is the base of the PCB consisting of pre preg materials ca. of FR-4, polyimide or metal substrates that offers the electrical grounding room temperature/increasing separation room temperature as needed. The second category of prepregs are fiberglass cloth with resin impregnated designed to serve as the layers that provide mechanical strength to the core and electrical contact to copper.
The use of such materials and their selection and application are instrumental in ensuring that the PCB achieves most of the demands that are placed on modern electronics. Critical factors like dielectric properties, thermal stability mechanical strength and cost effectiveness to enhance or maintain the performance and reliability of the final product need to be analyzed when selecting the right dielectric material. Due to the fact that fast-development electronic devices necessitate such PCB that is high-density, high-speed as well as being too advanced in structure, the role of the core and prepreg materials becomes indispensable.
With that said, understanding the differences between the core and prepreg materials used in PCBs, and how they are applied when manufacturing them, can help industry stakeholders gain insight into the comprehensive and complex processes involved in producing reliable and high-power circuit boards. This knowledge not only gives out the specification of the work to be done in the designing and manufacturing of the device but also puts food for thought for further innovation of the advanced electronic devices of the future.