Surface Mount Technology (SMT) has come to be appreciated as the ‘game-changer’ in the thrilling world of electronics manufacturing, being the latest innovation that alters the process of putting electronic components on printed circuit boards (PCBs). The objective of this article is to dismiss the myths associated with SMT and enlighten the reader about its principles, the advantages of SMT, and its role in the miniaturization and functionality improvement of modern electronics.
What is Surface Mount Technology?

Surface Mount Technology (SMT) is a technique that enables placing components directly onto the PCB surface. Different from Through-Hole Technology (THT), which involves the insertion of component leads through the holes on the PCB and then soldering them on the other side, the SMT of molten solder pulls components have connecting tabs or pads that are soldered directly into the PCB’s surface.
SMT involves mounting electronic components on the board’s surface instead of running the leads through the PCB’s holes (like THT). It is done with the help of the specific instruments that accurately put the components onto the solder boards to which they are applied. The solder paste will then be heated, turning it into a liquid and, at the same time, bonding the components to the PCB.
Basic Principles of SMT
These are the basic principles:
- Component Size and Packaging: They are also small in size and come in compact designs with flat forms, such as resistors, capacitors, diodes, and integrated circuits (ICs). This advancement closely resulted from the institution of leadless wires (leads) or, moreover, flexible swapping that is related to insertion, which effectively enabled more condensed and sophisticated PCB designs.
- Mounting Techniques: SMT components are put onto PCBs through automatic assembly equipment, e.g., pick-up and place machines. These sorting machines get the components with the help of a vision system and then solder them using the reflow soldering technique, where solder paste is applied to the PCB pads and later the entire PCB is heated to melt the solder mask, thus creating a much more secure soldered joint.
- High-Density Interconnection (HDI): Through SMT [surface-mount technology], multi-layer circuit designs become more compact and complex, with traces and via available on different levels. HDI technology enables signal quality, eliminates electromagnet interference, and enhances the overall performance of electronics.
Role of SMT in Miniaturization and Functionality
Miniaturization:
SMT is an essential technique in the miniaturization of electronic devices that helps to add more functionality in small form factors. This is clear in mobile phones that utilize SMT technology in the integration of high-end processors, memory chips, sensors, and connection modules into slim and lightweight models.
Increased Functionality:
SMT helps with the assembly of the most complex elements of soldering electronic components, like microcontrollers, RF (Radio frequency) chips, and MEMS (micro-electric Systems) sensors, with high accuracy and repeatability. The use of sensors improves the performance of electronics as it allows sophisticated electronic assembly, which brings wireless communication, interactive sensing, and AI-based automation features.
Surface Mount Components
These are the lists of surface mount components:
Resistors are passive electronic components that contribute to the electrical flow limitation. Resistors, which come in surface mount packages, including chip resistors (rectangular) that are typically soldered directly to the PCB surface, are a common part of the resistor group in SMT. They are provided in different rating values and power restitutions, making them versatile for many features. SMT resistors provide components that are miniature, requiring less space and enabling us to have compact and densely packed PCBs.
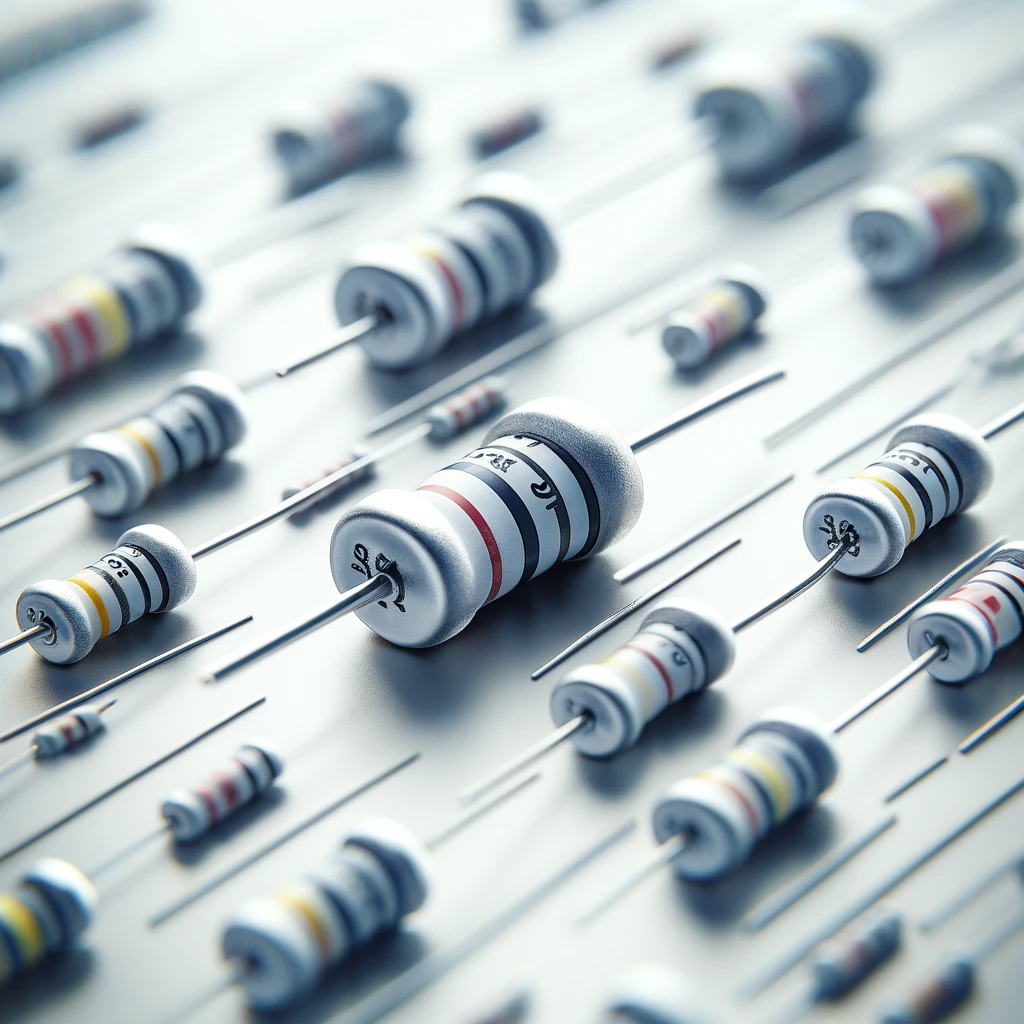
Capacitors perform practical functions such as cleaning, rectifying, and gluing circuits. Ceramic-type SMT capacitors made of tantalum (TDK) are most common, as their small size offers high capacitance values. SMT capacitors often play an integral part in reducing microprocessor sizes and in enhancing the performance of electronic devices by providing stable power sources and less noise.
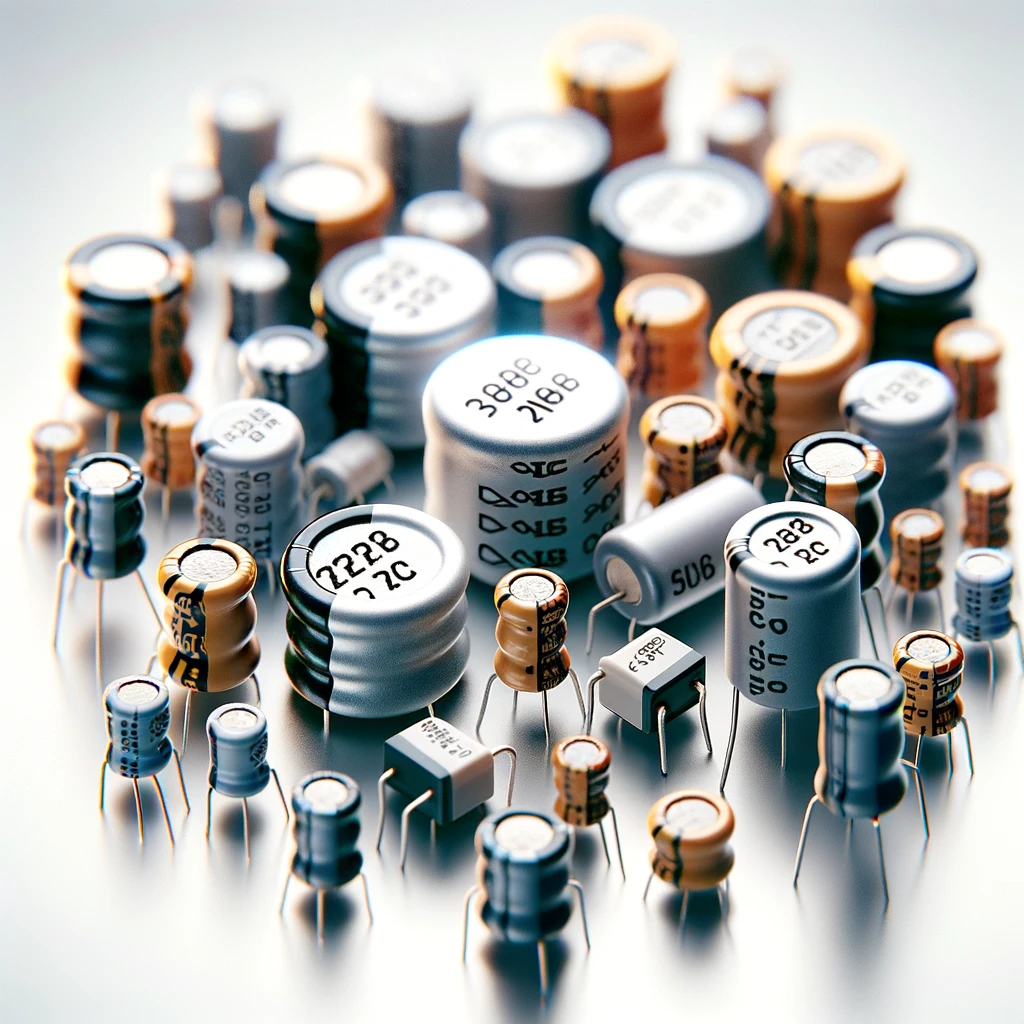
Diodes are semiconductor devices that only permit current to flow in one direction while blocking it from running in the opposite direction. SMT-class diodes, including Schottky diodes and Zener diodes, are effective for general rectification, voltage regulation, and signal modulation tasks. As a result of their small size and great operation efficacy, they are used in modern circuits as essential ones, especially for power management and signal processing applications.
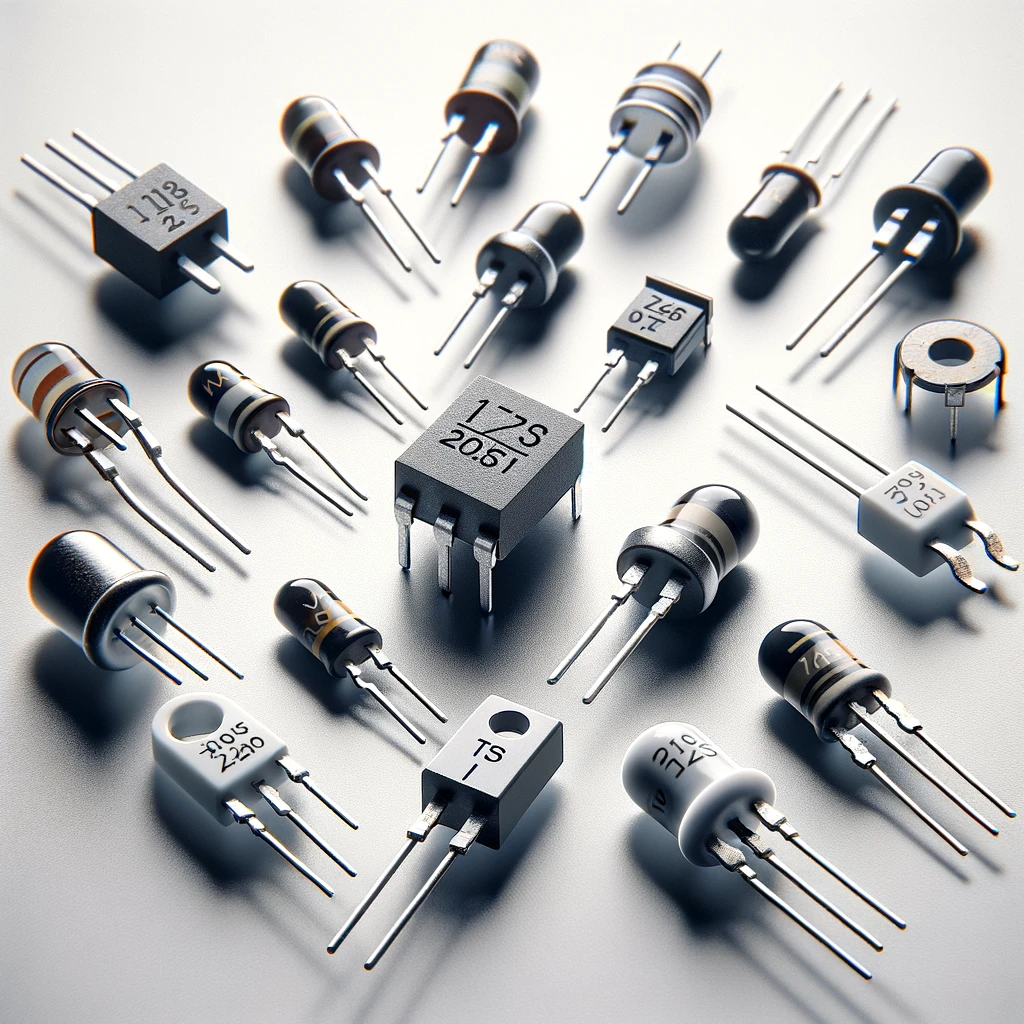
Integrated circuits (IC) are a collection of electronic components such as bipolar transistors, resistors, inductors, etc. that are fully integrated into a single semiconductor chip. The use of SMT electrical components allows the components to be directly mounted onto a PCB using surface mount techniques and yields greater space savings and improved electrical performance as compared to through-hole components or integrated circuit packages. They generally come in different types that include microcontrollers, amplifiers, sensors, and memory chips, hence allowing electronics machines to perform well-defined tasks.
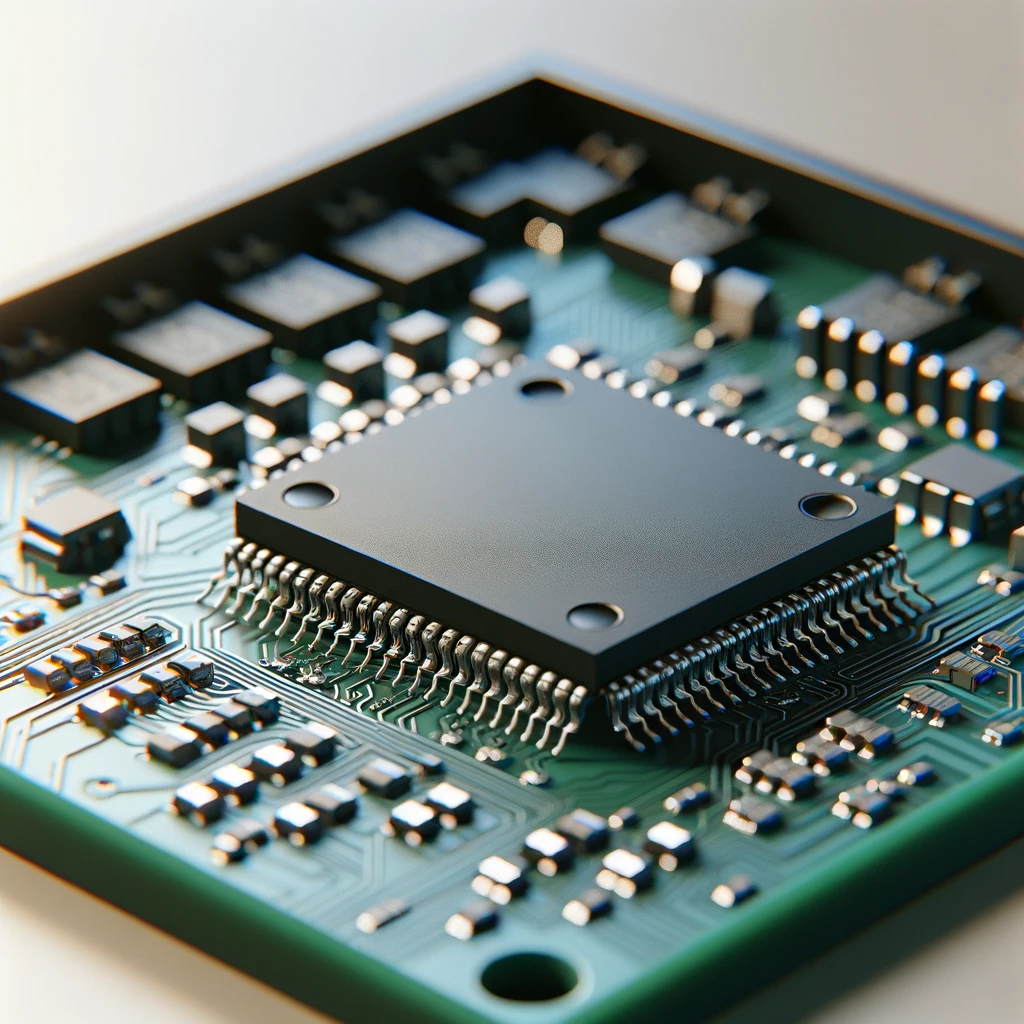
Characteristics and Benefits of PCB SMT Components
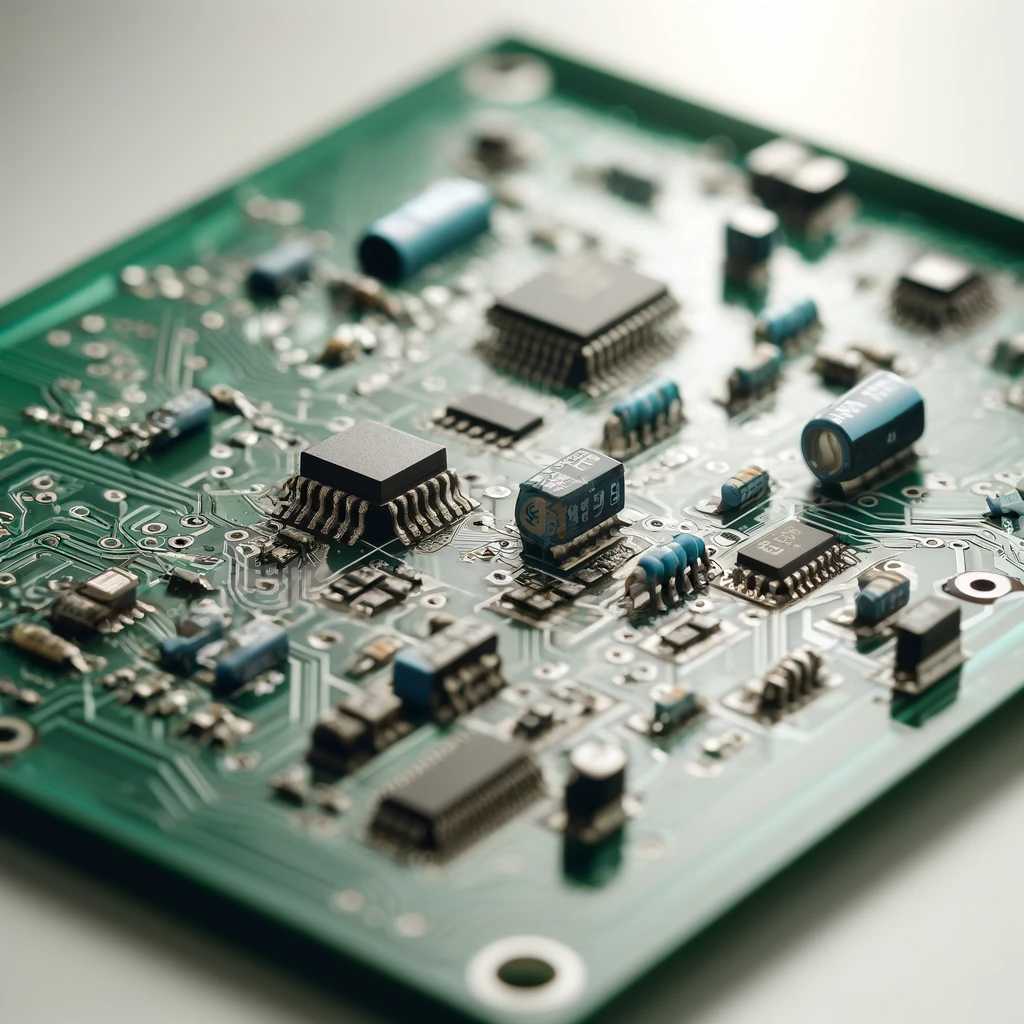
Surface-mount components such as resistors, capacitors, diodes, molten solder and ICs tend to perform much better than their through-hole counterparts in terms of space efficiency, performance, integration, automation, and cost-effectiveness. It is these features that make SMT the preferred method of modern electronics production, providing for the miniaturization, sophistication, and advancement of electronic devices into different industries.
Space-saving: SMT components are a handful in size as compared to through-hole components or parts, resulting in lightweight and compact electronic epoxy. Therefore, this parameter plays a huge role in the making of portable devices and miniaturized electronics of the same size.
Improved Performance: SMT component packages have several electrical advantages, mainly because of short traces and better heat dissipation. Consequently, the above process contributes to the increased dependability and usability of electronic systems.
High-Density Integration: By implementing SMT facilities, the board layouts are more compact, with a close spacing of components that brings into play higher functionality and better signal quality. Thus, designers are given the opportunity to fit as many functions as possible in the given limited space, and resource efficiency is absolutely guaranteed.
Automated Assembly: SMT is welcoming automation technology, like pick-and-place machines and reflow soldering, to streamline the manufacturing process and cut production costs. With this automation, the manufacturing process is dispensed with human error and variations, providing high accuracy and precise component placement.
Cost-effective: SMT assembly set-up costs could be high initially, but due to high production efficiency, material waste declines and shipping expenses become smaller because they do not involve the transport of bulky components.
Key Components in SMT Manufacturing Process
PCBs (Printed Circuit Board): These are the open platforms that contain all the essential components and are responsible for holding together all the electronic elements. Fiberglass replenished with epoxy or other organic composite materials is usually used as basic materials for manufacturing Printed Circuit Board.
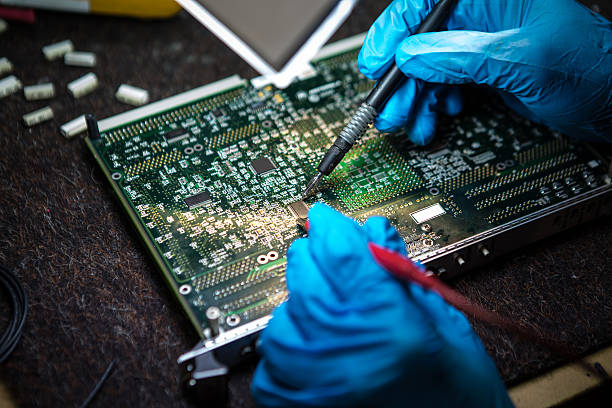
Electronic Components: SMT elements come in different form, such as resistors, capacitors, ICs, diodes, and so forth. This module can be placed or mountedin a way that will allow direct contact with the surface of the Printed Circuit Board.

Solder Paste: Solder paste and solder joints consist of condensed lead and flux in a uniform mix. Here we will be solder to the pads on the Printed Circuit board, where components will be positioned. The mix serves as a bridge between the components until they become part of the solder.
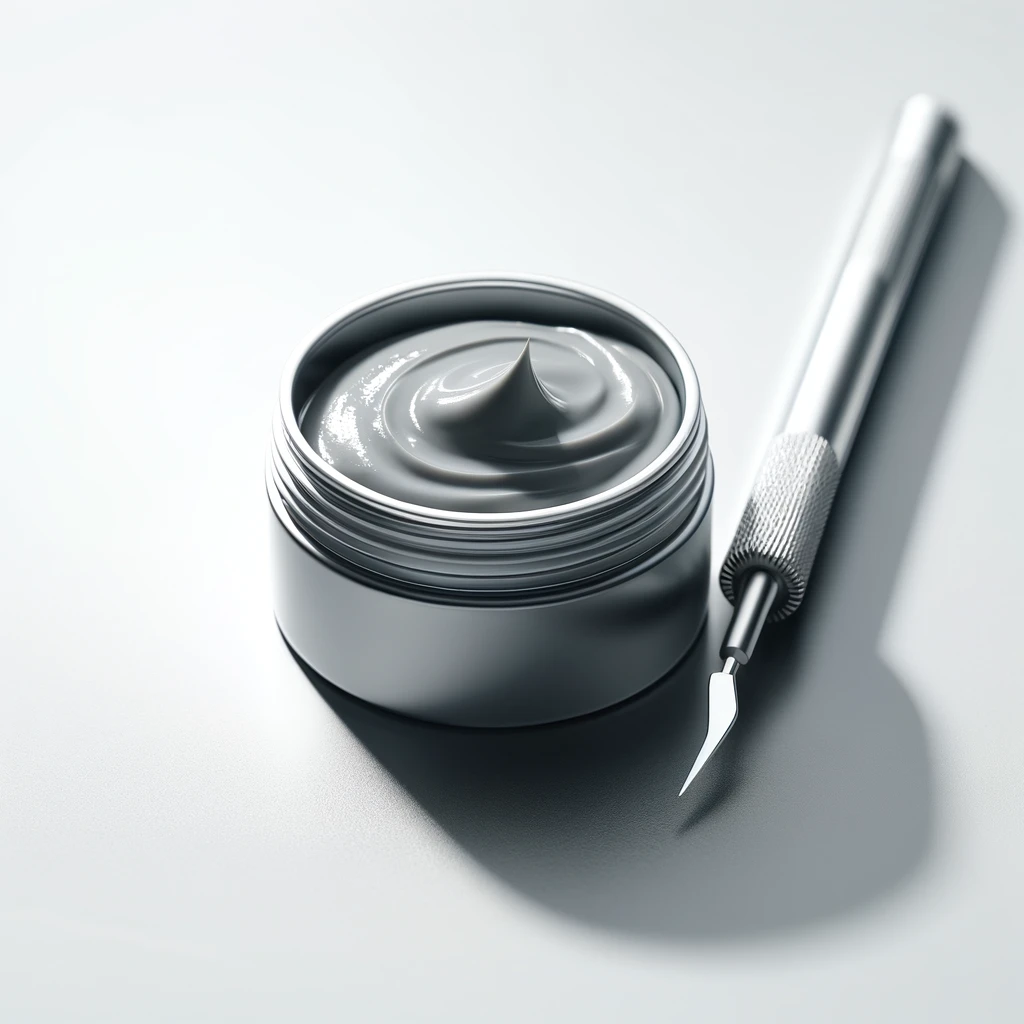
SMT Placement Machines: These are highly precise SMT placing systems which can put the required components onto the PCB boards according to the set specifications. Such machines are designed with the purpose of feedback and can handle and position components accurately and efficiently.
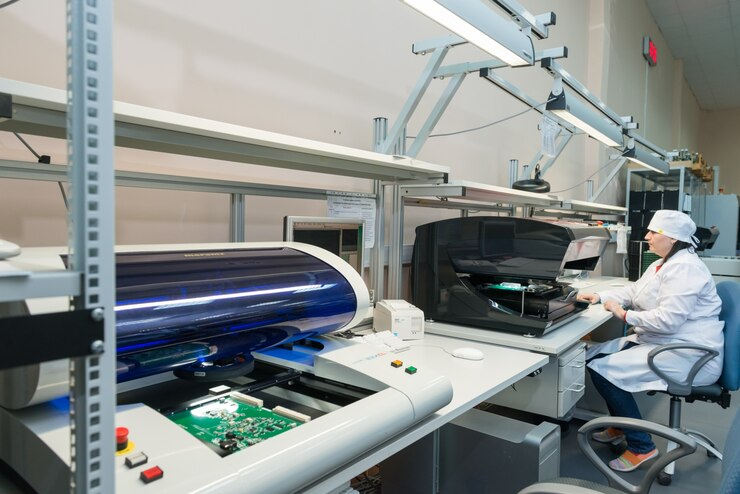
Reflow Oven: When components are placed on the board, the assembly process goes to the oven, which provides reflow. Overall, this process heats solder paste to certain temperature, leading to its melting and consequently causing the permanent jointing of components to PCB.
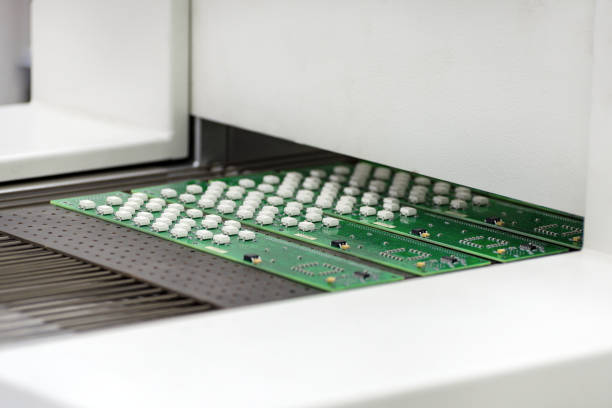
Advantages of SMT Manufacturing
In electronic industry, SMT (Surface Mount Technology) has been developed faster to other methods, which is used to mount electronic components on boards. In addition to SMT, it could equally be another dominant technology in the electronic industry through the production of latest devices through the employment of through-hole assembly techniques. Let’s delve into four key advantages of SMT manufacturing:
Space Efficiency: Machine translation is one of the main reasons why the lack of space has become an important issue. The SMT parts are significantly smaller and even lighter to work with than the through-hole components. The size of systems is getting smaller, thereby leading to an increase in component density on the circuit boards. It aids in the creation of small devices, which may include their efficiency and portability.
Enhanced Performance:This is the small size of SMT that, when integrated into machines, helps not only to save space but also to distribute better power. We observe the reduction of dead tracks between the bits and decreasing of the electrical noises that make the operation of electronics perfect. It’s almost an SMT passive components that becomes necessary in high-end devices with the latest technology because they operate fantastically, producing high-frequency desirable functions and fine-pitch leads, which causes a huge rise in performance metrics.
Cost Efficiency: Among surface-mounted technology (SMT) manufacturing, there are economics to be taken advantage of, which can be one of the very contrasts versus the mounting through-hole technique. The introduction of this automated technology makes processing cheaper, reduces faults incurred by humans in placement of components, and reduces manufacturing costs.
5. Challenges and Solutions in SMT Manufacturing
A. Component Miniaturization Challenges
Component Size and Accuracy: Much smaller components demand more accuracy in positioning and soldering, and therefore, such process becomes more complicated.
Density and Routing: More components being packed in a smaller area results in multiplexing of signal paths and traces to prevent cross-talk.
Inspection and Quality Control: Due to miniaturization of the components, the inspection becomes more and more difficult; therefore, advanced inspection methods are needed.
Solutions for Component Miniaturization
Advanced Pick-and-Place Machines: Up-to-date Surface Mount devices consist of high-speed, precision pick-and-place machines fitted with vision systems and robotic arms. These pieces of equipment can process even the tiniest components and make sure the desired position is achieved on PCBs.
Miniaturized Soldering Techniques: Surface-mounted devices like laser soldering and ultra-fine-pitch soldering enable manufacturers to solder small components precisely without harming nearby parts.
3D Inspection Systems: Automated optical inspection (AOI) and X-ray inspection systems complement the thorough quality control process where defects in miniaturized components may not be detected by manual inspection.
B. Thermal Management Challenges
Heat Generation: High-performance chips and very thin layers of printed circuit boards (PCB) inside the cellphone body create a lot of heat during the cell phone operation.
Heat Dissipation: The heat sink should be able to effectively collect and dissipate the heat produced by components and PCB.
Temperature Variations: Consistency in temperature distribution across the PCB is a mandatory condition to achieve a failure-free operation.
Solutions for Thermal Management
Advanced Cooling Systems: Thermal methods such as heat sinks, heat pipes, and thermal pads are applied to effective removal of heat from components and individual boards (PCBs).
Thermal Simulation and Analysis: Thermal simulating software has been a must-have tool of manufacturers who want to simulate heat flow and design their printed circuit boards for heat passage.
Smart Thermal Management: Certain devices features smart thermal management systems that regulate the rotation of blades, fluctuate the scatter frequency and manage power usage according to the feedback particle temperature sensors, This reduces heat build up and maximizes device functionality.
6. Future Trends in SMT Manufacturing
- Miniaturization and High-Density Integration: Manufacturers are looking into more sophisticated ways to accurately position components with higher pin counts and density, which then enables for the construction of very compact boards. High-density Integration means cramming more function to a space limited by minimum space. These demands also push out manufacture of more complex PCB manufacturing (Printed Circuit Boards) and innovative interconnection solutions such as Microvia and HDI (High-Density Interconnect).
- Advance Materials and Processes: In SMT manufacturing of the future, the bill of materials will include newly-developed advanced materials like nanomaterials, flexible substrates, and conductive inks. These materials provide enhanced performance, flexibility, and endurance suitable for smart wearables, Internet-of-Things (IoT) devices and flexible displays, fulfilling the needs accordingly.
- Automation and robotics: The function of automation is to establish a strong connection with manufacturing as it ensures the effectiveness SMT processing, reduces errors made by humans, and increases production efficiency.
- Environmentally Sustainable Practices: With sustainability becoming a serious issue in the electronics industry, including SMT, there is a significant need to improve our environmental standards as well. Tending toward future outcomes boils down waste, energy, and eco-stress through the incorporation of measures like lead-free soldering, recyclable materials and eco-friendly technologies.
- AI and Machine Learning in Quality Assurance: AI-enabled inspection devices and practical algorithms that use deep learning techniques are having a great impact on the SMT quality process. The use of these technological tools is crucial for online out-of-sight manufacturing, that allows designers to detect real-time defects, perform detailed analysis and perform automatic restoration to ensure manufacturing quality and reliability.
Exploring Diverse Applications of SMT
Surface Mount Technology (SMT) as a breakthrough in electronic parts manufacturing stems from the fact that it is not only highly compact but also very efficient at putting electronic parts onto printed circuit boards (PCBs). These days, this technology has seen significant adoption in a range of electronics industry and has consistently spurred innovation and forward progress in electronics.
Consumer Electronics: In the category of consumer electronics, Surface Mount Technology gets used widely among all the industries. Smartphones, tablets, laptops, and smartwatches represent the main devices that are heavily using surface-mounted devices for their compact design and high capabilities. Surface-mount Mount Device gives a chance to the manufacturers to integrate a large number of electronic components like microprocessors, memory modules, sensors as well as connectivity devices in compact and easy to carry devices.
Automotive Electronics: In automotive industry, Surface Mount Technology is a crucial technology for the production of electronic control units (ECUs), sensors, infotainment systems and advanced driving assistance systems (ADAS). This includes small sizes, reliability and badging through resistance to harsh environmental conditions, which are done in this process.
Medical Devices: In the area of medical technology, numerous important breakthroughs that are based on SMT advances have taken place, including the production of sophisticated tools and surface-mount devices involved in treating patients. The advantages of SMT, such as accuracy and reliability, increase the outcome and effectiveness of medical treatments and, consequently, impact the health and recovery of patients.
Role in Driving Innovation: SMT is undoubtedly the main factor behind versatile technological advancements. Its small-scale production, quick assembly procedure, and optical inspection liquefy electronics development. Automated PCB assembly and components space use is being optimized, their weight and power consumption are reduced, and manufacturing assembly scalability is enhanced by the SMT. It enables manufacturers to push the boundaries of technological innovation.
In Summary
Surface Mount Technology (SMT) has made a tremendous impact in the electronics production industry by promoting the creation and assembly of electronic devices through the mounting of the components directly on the Printed Circuit Board (PCB). This article was all about clarifying myths concerning SMT, detailing its principles and advantages, and focusing on its key role in scaling down the size of modern electronic devices and improving them as well.
SMT’s basic elements include components size and packaging, as well as mounting avenues that provide the means for the creation of PCB designs of high density and sophistication. In the era of compactness and portability, smartphones represent one of the best examples of processors, memory chips, sensors, and connectivity modules being packed into sleek and small form factors.
Surface Mount technology as a component promotion that saves spaces, provides better performance, high-density integration and automated assembly is, in addition, cheaper. They are what put SMT ahead of the rest and from precision to ease of mass production, these are the qualities that manufacturers shooting for top performance, seamless design and cost-effective production look for.
SMT manufacturing seems to be filled with challenges related to component miniaturization and thermal management. Complicated methods comprised of high-precision pick-and-place machines, micro-soldering technologies, thermal simulation software and smart thermal management systems have the potential to help deal with these challenges and continue to make progress in electronics manufacturing.
SMT manufacturing future trends comprise not only miniaturization and high-end integration but also advancements in materials, automation, environment, and AI and machine learning in quality assurance processes.
The application scope of SMT ranges over a broad spectrum covered by consumer electronics, automotive electronics, and medical devices, among others, enabling innovation and improved performance in technological fields. The significance of SMT in shaping innovation in the field of electronics cannot be overstated, progressing the development of technology and preparing for future growth.