PCB SURFACE FINISHES
PCB SURFACE FINISH TYPES
PCB surface finishes are crucial treatments for copper traces and pads on printed circuit boards, providing protection against oxidation, enhancing solderability and electrical conductivity, and ensuring a reliable component attachment interface. They are essential for maintaining PCB performance and longevity, especially in environments exposed to dust, harsh chemicals, and extreme temperatures. Selecting the right surface finish is a key design decision, vital for preventing copper deterioration and maximizing the assembly’s service life.
IMMERSION GOLD (ENIG)
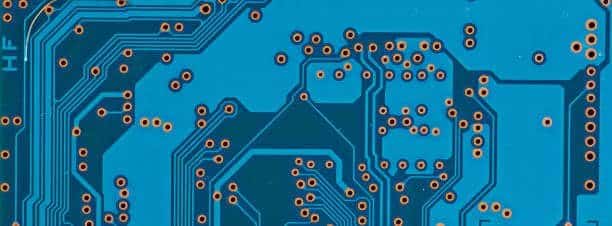
Electroless Nickel Immersion Gold (ENIG) is a premier PCB finish, featuring a two-layer coating of 2-8 µin gold over 120-240 µin nickel. The nickel layer acts as a barrier to copper, providing a robust surface for soldering, while the gold top layer prevents nickel oxidation, ensuring low contact resistance and superior protection during storage. This finish is celebrated for its flatness, lead-free composition, and compliance with RoHS standards, making it a popular choice in the PCB industry for a wide range of applications, including those requiring fine pitch and high reliability.
Advantages: ENIG offers excellent flatness, RoHS compliance, lead-free composition, and is ideal for fine-pitch components and long-term reliability.
Disadvantages: Despite its benefits, ENIG is costly, can lead to signal loss, and is susceptible to black pad syndrome, complicating rework.
IMMERSION SILVER
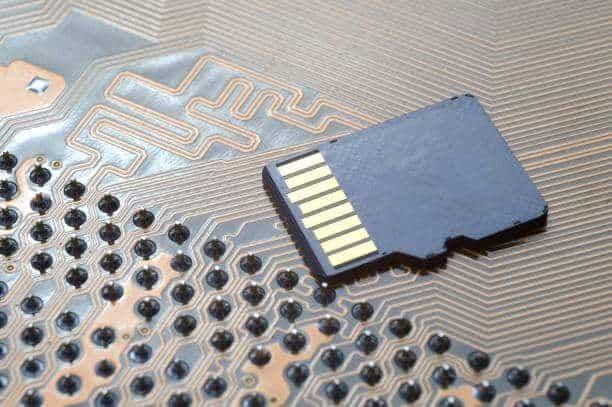
Immersion Silver utilizes a chemical displacement process to apply a submicron layer of pure silver directly onto the base metal of the PCB, offering excellent electrical properties and maintaining good solderability under heat, humidity, and pollution. Unlike ENIG, it lacks a nickel underlayer, compromising physical strength but ensuring cost-effectiveness and RoHS compliance. The finish, while susceptible to tarnishing, provides a flat surface conducive to fine-pitch and smaller components.
Advantages:Offers a flat soldering surface, is lead-free and RoHS compliant, supports tighter tolerances for plated holes, and features low signal loss for integrity applications.
Disadvantages: Sensitive to handling, causing soldering issues; more affordable than ENIG yet costlier than Immersion Tin; the finish can tarnish and oxidize without special packaging.
IMMERSION TIN
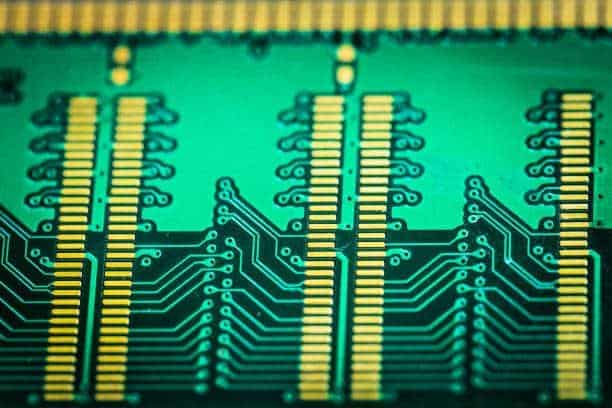
Immersion Tin (ISn) utilizes a chemical displacement reaction to apply a thin, uniform layer of tin directly onto the base metal of the PCB. This lead-free finish offers excellent solderability and is compatible with a wide range of solder types. The granular tin structure, achieved through organic additives, enhances thermal stability and overcomes issues like tin whiskers, making it a cost-effective alternative to ENIG and Immersion Silver while ensuring RoHS compliance.
Advantages: Provides a flat surface for soldering, is lead-free and RoHS compliant, suitable for fine pitch/BGA components, and ideal for press fit applications.
Disadvantages: Sensitive to handling, with potential for soldering issues and tin whiskers. It has a shorter shelf life than ENIG and requires careful storage.
HASL
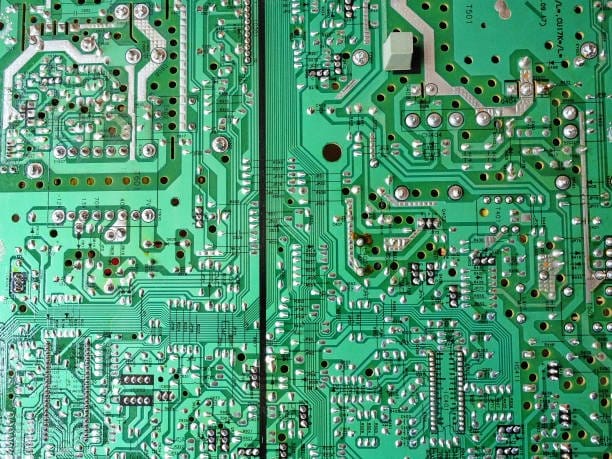
Hot Air Solder Leveling (HASL) is a traditional PCB surface finish process that involves dipping the board in molten tin-lead solder and then leveling it with a hot air knife. This method is cost-effective and provides a durable coating that protects against oxidation and enhances solderability. Although not ideal for very small SMT components or high-density interconnects (HDI) due to uneven surfaces, HASL remains a popular choice for its reliability and reworkability, especially for through-hole and larger SMT components.
Advantages: Highly economical, offers excellent solderability, reworkable, and exposes PCBs to high temperatures early on, highlighting any potential delamination issues before component attachment.
Disadvantages: Creates uneven surfaces, not suited for fine pitch components, contains lead (not RoHS compliant), and can result in solder bridging and thermal shock.
PB-FREE HASL
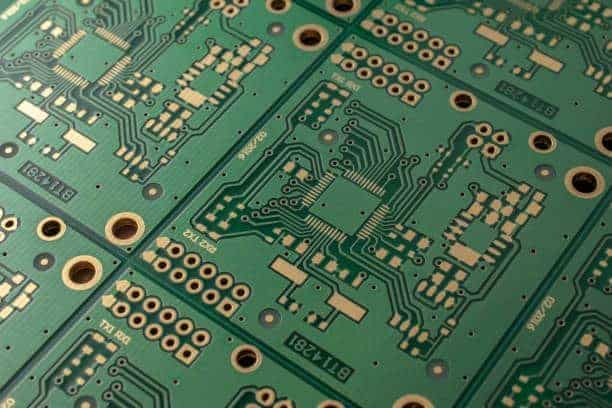
Lead-Free HASL replaces tin-lead solder with tin-copper, tin-nickel, or tin-copper-nickel germanium alloys, offering a non-toxic, RoHS-compliant alternative. It maintains the benefits of traditional HASL but supports environmental sustainability. Though more suitable for a wider range of components, it still struggles with very small parts.
Advantages: Retains excellent solderability at a relatively low cost, allows large processing windows, and supports multiple thermal excursions, making it RoHS compliant.
Disadvantages: Still presents issues with uneven pad thickness, high processing temperatures, not ideal for very fine pitch components, and can lead to bridging on fine pitch.
OSP
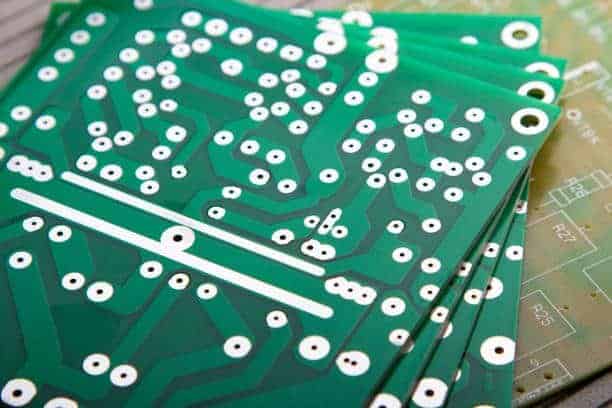
OSP is an environmentally friendly surface finish, applying a thin, organic film on bare copper surfaces to protect against oxidation, heat shock, and moisture. This lead-free coating, easily removed by flux during soldering, offers a simple and low-cost process. Utilizing water-based organic compounds like benzimidazole, OSP enhances copper protection through multiple organic layers, making it a preferred choice for its simplicity and green credentials.
Advantages: Provides a flat soldering surface, RoHS compliant and lead-free, cost-effective, simple application process, and reworkable, making it suitable for fine pitch/BGA and smaller components.
Disadvantages: Sensitive to handling, resulting in a short shelf life; not ideal for PTH; thickness isn’t measurable; can cause ICT issues; exposed copper on final assembly.
HARD GOLD
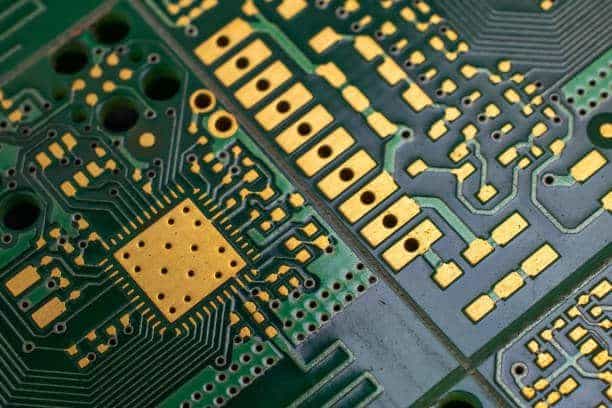
Hard Gold plating involves a durable layer of gold over a nickel barrier coat, commonly applied to high-wear areas such as edge connector fingers and keypads for its exceptional durability. This process allows for variable thickness by adjusting the plating cycle duration, catering to different class requirements. However, due to its high cost and relatively poor solderability, Hard Gold is not typically used on solderable areas, with solderable thickness recommended at 5-10 µin to remain below the solderability threshold of 17.8 µin.
Advantages to Hard Gold: Provides a hard, durable surface, lead-free, RoHS compliant, with a long shelf life, ideal for high-wear applications like edge connectors and keypads.
Disadvantages: Significantly more expensive than other finishes, requires extra processing and labor, poor solderability, can necessitate the use of resist/tape, and may lead to demarcation issues.
ENEPIG
Electroless Nickel Electroless Palladium Immersion Gold (ENEPIG) is a multifaceted surface finish that provides a robust triple-layer coating on PCBs. This finish starts with a layer of electroless nickel, followed by a thin palladium layer to prevent nickel corrosion, and is topped with immersion gold to protect against oxidation. Known for its excellent electrical properties, ENEPIG offers superior wire bondability and is ideal for mixed-assembly applications, ensuring a high level of reliability.
The ENEPIG finish is often recommended for its exceptional performance in preventing black pad syndrome, a common issue with ENIG finishes. Its layered structure makes it highly compatible with both leaded and lead-free soldering processes, providing unparalleled versatility. This finish is particularly suited for complex, high-density PCBs, including those used in the telecommunications and aerospace industries, where long-term reliability is crucial. ENEPIG’s comprehensive benefits make it an attractive option for advanced electronic applications.
ENEPIG VS. OTHER FINISHES
ENEPIG offers unparalleled versatility, serving as an ideal choice for complex PCBs with its excellent solderability, wire bondability, and resistance to corrosion. It outshines other finishes by preventing black pad syndrome and supporting both leaded and lead-free soldering, making it highly adaptable to various assembly requirements.
Compared to finishes like ENIG, HASL, or OSP, ENEPIG stands out for its compatibility with multiple assembly technologies and superior performance in high-reliability applications. Its layered structure enhances durability and connectivity, especially in high-density and mixed-assembly environments, providing a comprehensive solution where others may fall short.
ENEPIG VS. OTHER FINISHES
comparison
IMMERSION GOLD (ENIG)
IMMERSION SILVER
IMMERSION TIN
HASL
PB-FREE HASL
OSP
HARD GOLD
Co-planarity
excellent
excellent
excellent
poor
excellent
excellent
Solder joint intergrity
good
excellent
good
best/excellent
good
good
——
RoHS Compliant
good
yes
yes
no
yes
yes
——
reflows
multiple
multiple
2 to 3
multiple
2
2
——
shelf life
12months
9-12months
9-12months
12months
9-12months
9-12months
——
solder contrast
good
——
——
poor
——
best
good
electric contace use
good
——
——
fair
——
poor
good
pcb high frequency loss
poor
——
——
fair
——
best
good
environmental hazard
medium (Ni)
——
——
high (Pb)
——
low (water based)
medium (Ni)
cost of surface finish
highest (1.5~2x)
——
——
standard (1x)
——
lowest (0.2~0.3x)
highest (1.5~2x)