Printed Circuit Board Assembly (PCBA) is the cornerstone of electronic device manufacturing, bringing to life the functionalities of everything from household gadgets to sophisticated industrial machinery. This blog aims to demystify the process of PCBA, providing a comprehensive guide to its techniques, components, and critical considerations.
Understanding PCBA
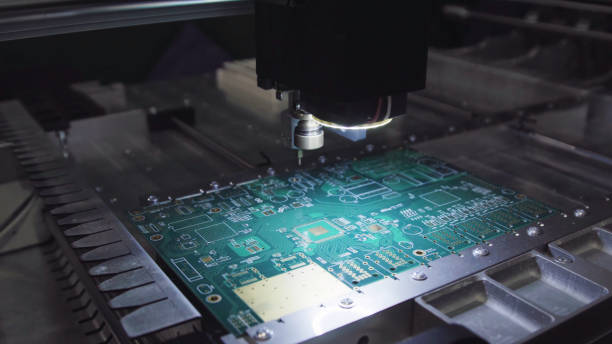
PCBA is the process of soldering various electronic components to a printed circuit board (PCB) to create a functional electronic assembly. The PCB provides the necessary mechanical support and electrical connections through conductive pathways etched from copper sheets laminated onto a non-conductive, substrate material.
Two main methods that a PCBA company may use for PCB assembly
Two main methods commonly used by PCBA companies for assembling printed circuit boards are:
Surface Mount Technology (SMT)
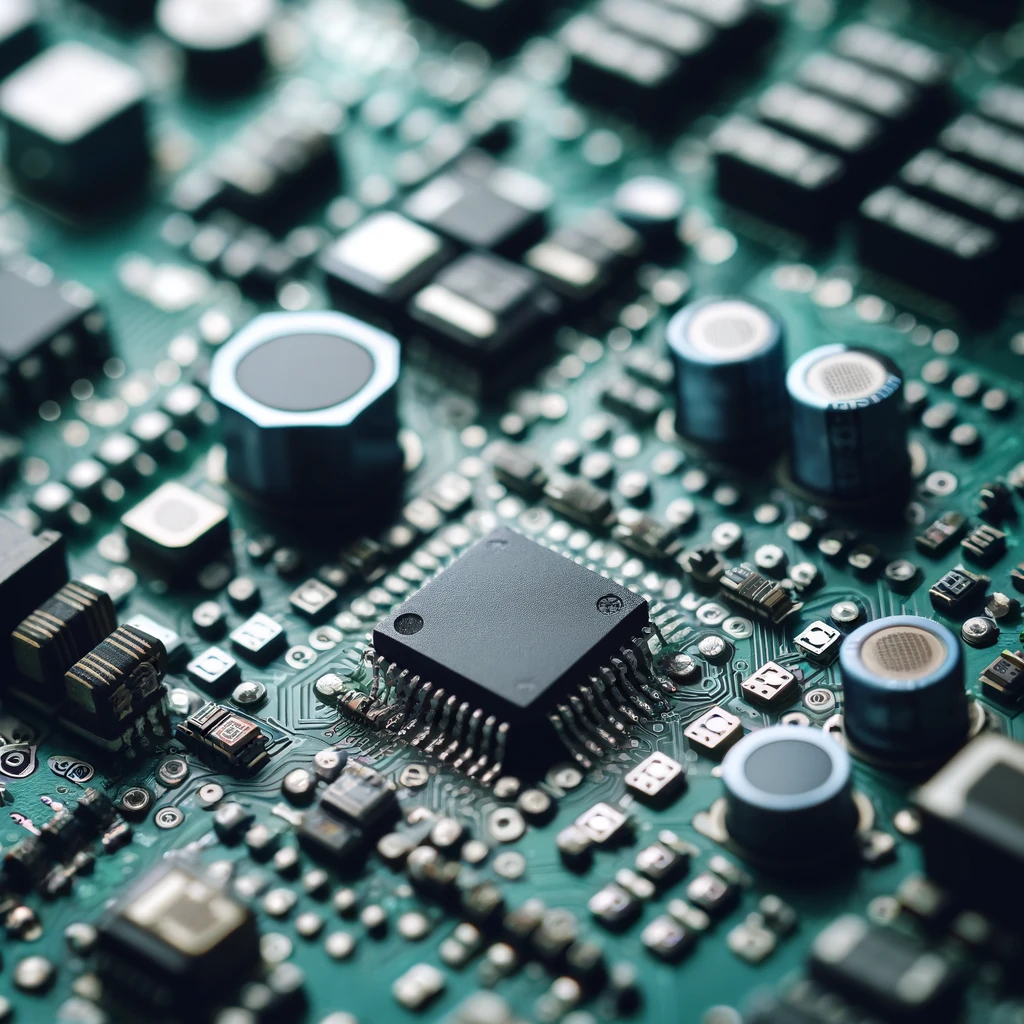
(SMT process involves placing components directly onto the surface of a PCB. Components, known as surface-mount devices (SMDs), are smaller and allow for more complex and compact PCB designs. This method is highly automated, enabling faster production speeds and higher component density, making it ideal for modern electronic devices.
Through-Hole Technology (THT)
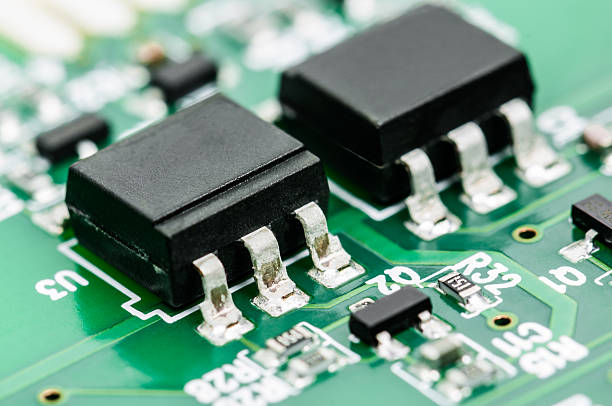
In THT, components have leads that are inserted into holes drilled in a single layer of the PCB and then soldered to pads on the opposite side. This method provides stronger mechanical bonds than SMT, making it suitable for components that endure mechanical stress or need more robust connections. THT is generally used for larger components or where extra durability is required.
How Do PCBA and PCB Relate to Each Other?
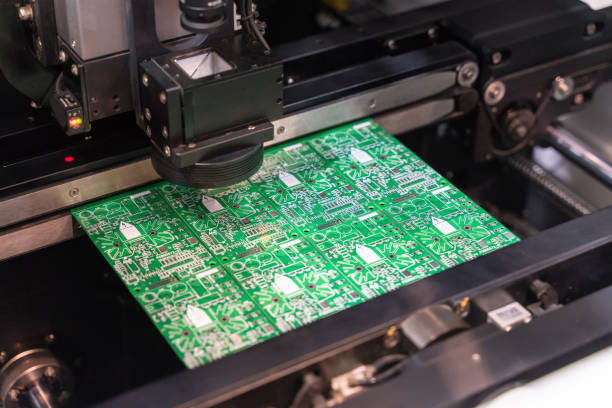
PCBA (Printed Circuit Board Assembly) and PCB (Printed Circuit Board) are closely related in electronics manufacturing. A PCB serves as the base structure, consisting of layers of insulating material with conductive pathways etched into it. PCBA refers to the process and result of mounting electronic components such as capacitors, resistors, and ICs onto a PCB, making it a complete and functional electronic circuit. Essentially, a PCB is the foundation, and PCBA is the completed assembly that allows electronic components attached the device to function as designed.
Difference Between the PCBA and PCB
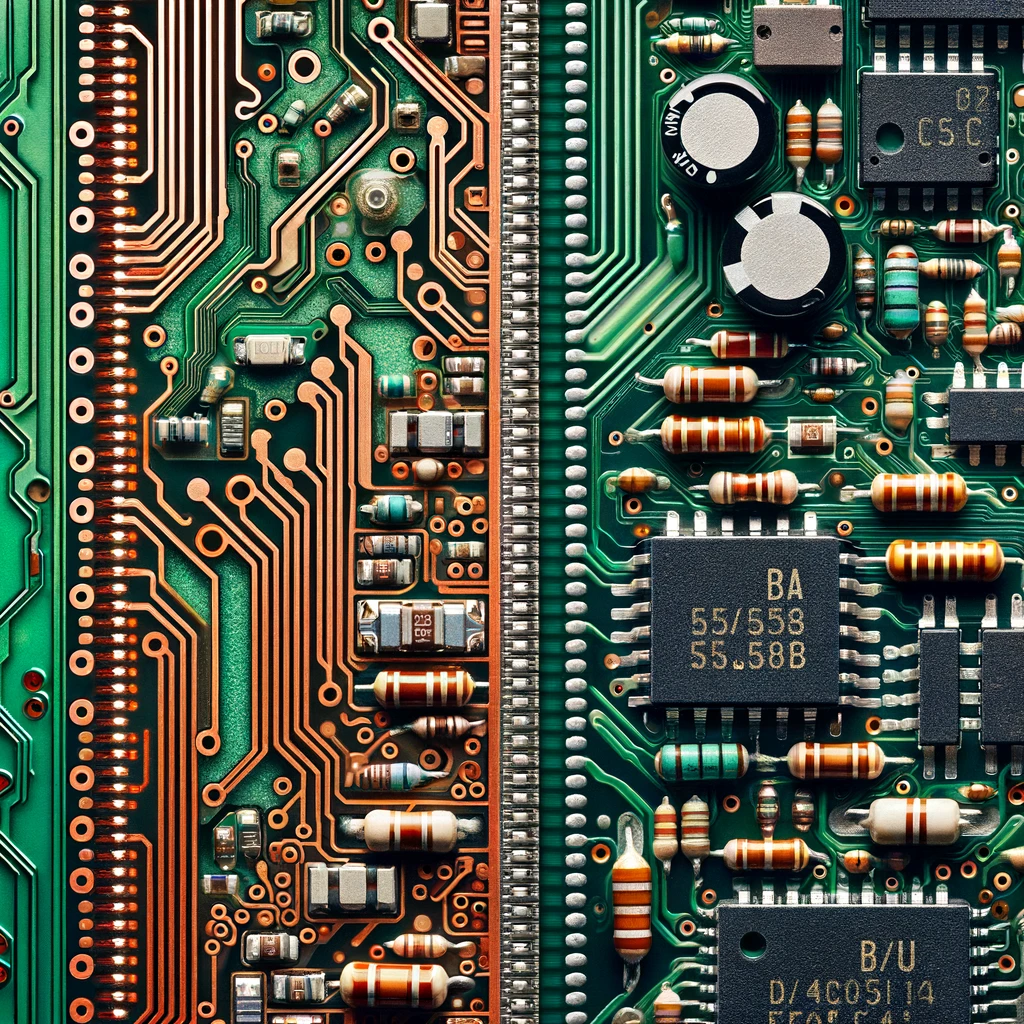
The main difference between PCB (Printed Circuit Board) and PCBA (Printed Circuit Board Assembly) lies in their respective stages within electronics manufacturing:
- PCB (Printed Circuit Board):
- A PCB is a bare board made from non-conductive materials with layers of copper circuitry embedded. It serves as the physical base on which electronic components will be mounted but does not yet contain any of these components. The focus is on the design and layout of the conductive tracks, pads, and other features that are etched onto the insulating substrate to form electrical connections.
- PCBA (Printed Circuit Board Assembly):
- PCBA refers to a PCB that has been assembled with electronic components. This involves the process of soldering various components onto the PCB to create a fully functional electronic circuit. PCBA represents the completed assembly process, where the board is equipped with all necessary components like resistors, capacitors, transistors, and integrated circuits, making it ready for use in electronic devices.
What To Consider For the Best PCB for PCBA Manufacturer
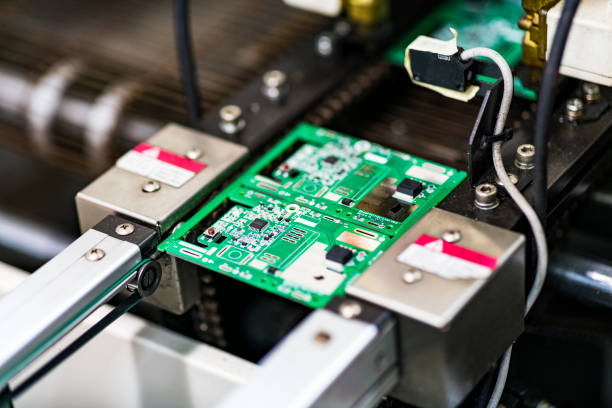
When selecting the best PCB manufacturer for PCBA, several key factors should be considered to ensure quality, reliability, and suitability for your specific needs. Here’s a list of important considerations:
- Quality Certifications: Look for manufacturers with recognized quality certifications like ISO 9001, ISO 13485 for medical devices, or automotive standard IATF 16949. These certifications indicate compliance with industry standards and a commitment to quality.
- Manufacturing Capabilities: Assess whether the manufacturer can handle the specific requirements of your PCB, including the type of material, layer count, trace widths, and spacing capabilities. Also, check if they can provide surface finish options like HASL, ENIG, or OSP.
- Assembly Technologies: Ensure the manufacturer supports the assembly technologies you need, such as Surface Mount Technology (SMT), Through-Hole Technology (THT), and mixed-technology assemblies. They should have the capability to place all types of components, including fine-pitch and BGA.
- Prototype Services: Verify if the manufacturer offers rapid prototyping services. This allows you to test and refine your PCB designs before full-scale production, reducing the risk of costly errors.
- Lead Times and Flexibility: Consider the manufacturer’s lead times and their flexibility to adapt to urgent demands. A responsive and flexible manufacturing partner can be crucial in meeting market demands and deadlines.
- Testing and Inspection: Check that comprehensive testing and inspection methods are in place, such as Automated Optical Inspection (AOI), X-ray inspection, and functional testing. These are essential to ensure the reliability and functionality of the assembled PCBs.
- Supply Chain and Component Sourcing: A manufacturer with a robust supply chain management system and good relationships with component suppliers can offer more stability in terms of component availability and pricing.
- Experience and Technical Support: Evaluate the manufacturer’s experience in your industry and their ability to provide technical support throughout the development and manufacturing process.
- Cost-effectiveness: While quality should not be compromised for cost, it’s important to ensure that the pricing offered by the manufacturer is competitive and aligns with the market standards.
- Environmental Compliance: Ensure that the manufacturer adheres to environmental regulations like RoHS, REACH, and WEEE, which are important for reducing the environmental impact of electronic products.
Key Steps in the PCBA Process
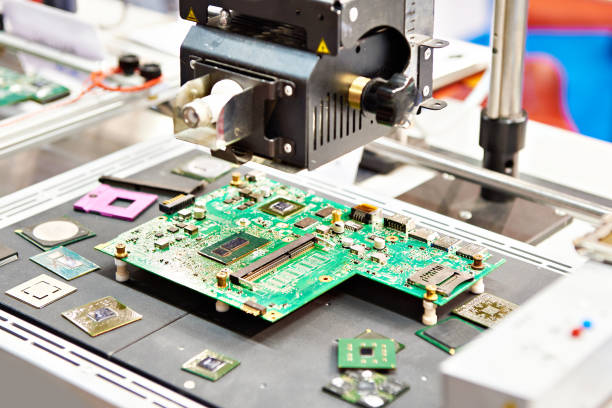
The Printed Circuit Board Assembly (PCBA) process is critical in the manufacturing of electronic devices. Here are all the necessary components and key steps involved in the PCBA process:
- PCB Design: The process begins with designing the printed circuit board using CAD software. This step involves laying out the circuit schematically and converting the schematic to a PCB layout that dictates where each component will be placed.
- PCB Fabrication: Once the design is finalized, the physical PCB is manufactured. This involves multiple steps such as etching the copper to form traces, drilling holes for through-hole components, and applying a solder mask to prevent unwanted solder bridging.
- Component Sourcing: All electronic components required for the assembly are procured. This step must ensure that all components are available and meet the required specifications for the device.
- Solder Paste Application: Before placing components on the PCB, solder paste is applied to areas where components will be mounted. This is typically done using a stencil that matches the PCB layout, ensuring the solder paste is only applied where needed.
- Pick and Place: Automated machines then place surface-mount components onto the PCB. These machines use vacuum nozzles to pick up components and accurately place them on the solder paste.
- Reflow Soldering: After placement, the PCBs go through a reflow oven. The heat in the oven melts the solder paste, which solidifies to form electrical connections between the components’ terminals and the PCB.
- Through-Hole Component Insertion: For components that cannot be surface-mounted, manual or automated through-hole insertion is performed. The leads of these components are inserted into pre-drilled holes on the PCB.
- Wave Soldering: If through-hole components are used, the PCB might pass through a wave soldering machine where molten solder forms the necessary joints. This may not be necessary if selective soldering techniques are used instead.
- Inspection and Quality Control: After soldering, the board is inspected for defects such as solder bridges, cold joints, or misaligned components. Automated Optical Inspection (AOI), X-ray inspection, and manual checks are common methods used.
- Testing: Functional tests are conducted to ensure the PCB works as intended. This may include power-on tests, in-circuit testing, and functional verification tests.
- Assembly: The PCB may be assembled into a housing or combined with other boards or components to form a larger part of an electronic device.
- Final Inspection and Packaging: The completed assembly is inspected one final time to ensure quality and functionality before being packaged and shipped to the customer.
Challenges in PCBA
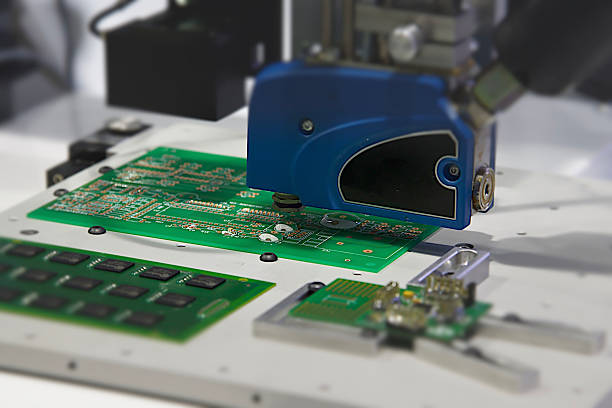
PCBA is not without its challenges, which can impact the efficiency and outcome of the production process. Common issues include:
- Soldering Defects: Issues like cold solder joints or solder bridges can lead to malfunctioning assemblies.
- Component Placement Errors: Misalignment or incorrect placement of components can cause the entire board to fail.
- PCB Design Flaws: Errors in the PCB design can lead to costly reworks and increased waste.
Best Practices for Efficient PCBA
To master PCBA, manufacturers should adhere to several best practices:
- Thorough Design Review: Ensure the PCB design is free of errors before fabrication.
- Quality Component Sourcing: Use high-quality components from reliable suppliers to minimize failures.
- Regular Maintenance of Equipment: Keep all assembly equipment well-maintained to ensure accuracy and reliability.
- Skilled Workforce: Employ well-trained technicians who can handle the complexities of PCBA.
- Continuous Improvement: Implement a feedback loop from testing and quality control to design and assembly to continuously improve the processes.
Applications of PCBA manufacturing process
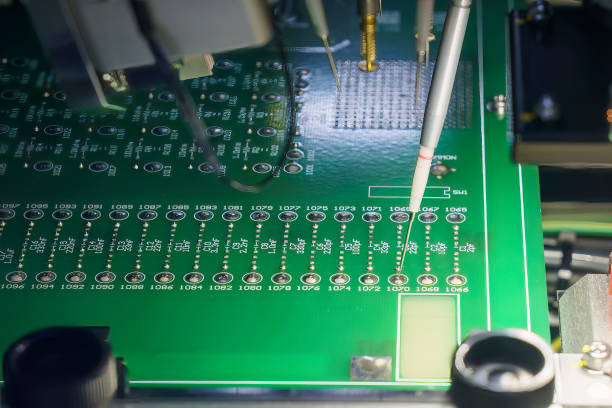
Here is a close-up image showcasing various applications of the Printed Circuit Board Assembly (PCBA) manufacturing process. The photograph features different types of PCBAs used in multiple sectors of electronics industry, such as consumer electronics, automotive, medical devices, and industrial automation in pcb manufacturing. Each PCBA is clearly visible, demonstrating the complexity and diversity in design and component placement, highlighting their adaptation to different functionalities and industry requirements.
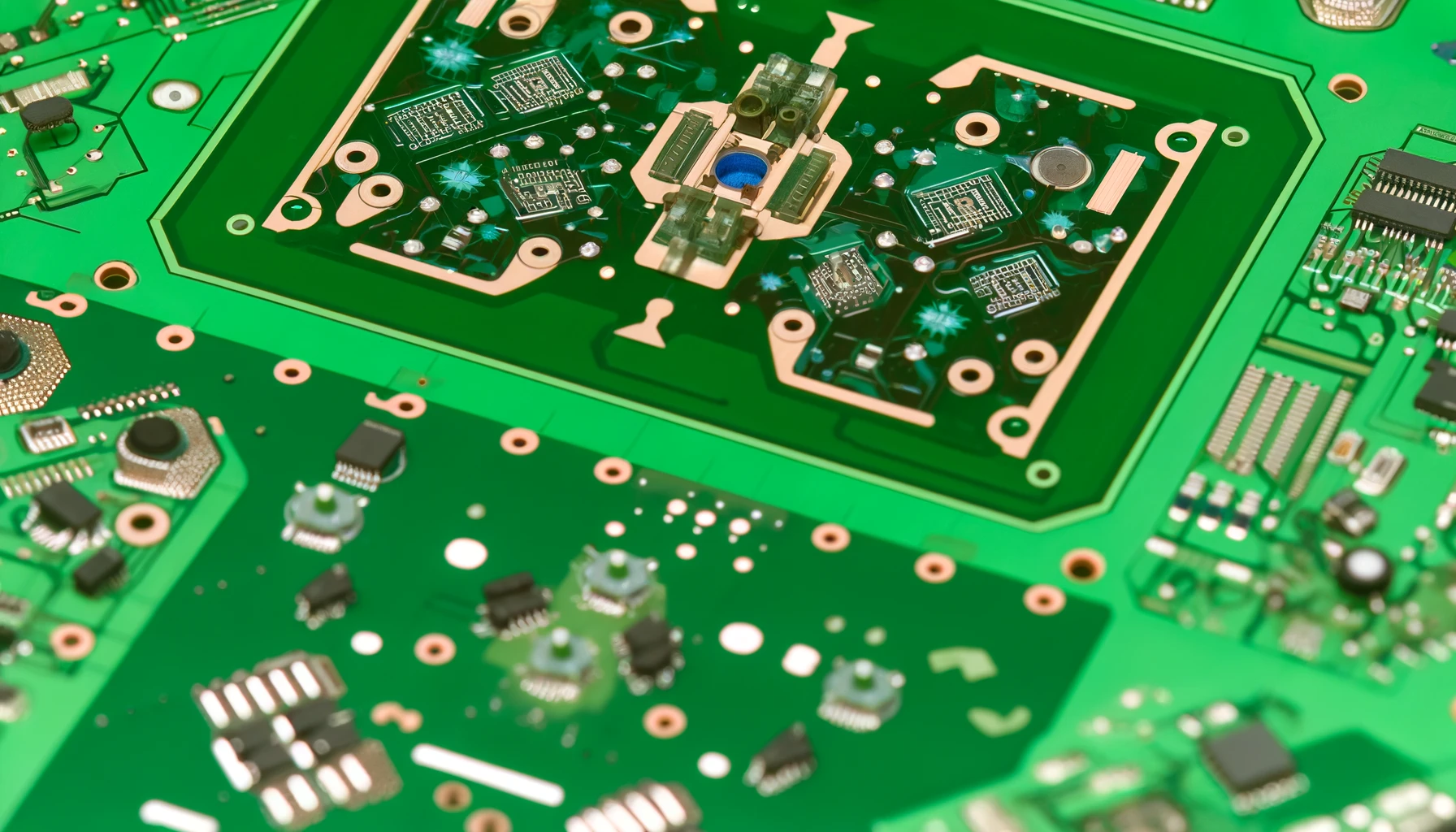
The PCBA (Printed Circuit Board Assembly) manufacturing process is integral to creating functional electronic devices used across various industries. Here are some of the key applications:
- Consumer Electronics: PCBA is crucial for assembling devices like smartphones, tablets, laptops, and household appliances such as refrigerators, microwaves, and televisions.
- Automotive Industry: PCBA is used in the manufacturing of electronic components for vehicles, including engine control units, infotainment systems, navigation systems, and safety systems like airbag controllers.
- Medical Devices: Critical medical equipment such as pacemakers, MRI machines, heart monitors, and diagnostic equipment rely on PCBAs to function accurately and reliably.
- Industrial Automation: PCBAs are integral to the operation of machinery and robots in manufacturing processes, as well as in control systems used in industries like mining, oil and gas, and agriculture.
- Telecommunications: PCBAs form the backbone of devices and infrastructure in the telecommunications sector, including routers, switches, base stations, and other networking equipment.
- Aerospace and Defense: PCBAs are used in various applications, from avionics and satellite communications to control systems for drones and military equipment.
- Computing: In the computing industry, PCBAs are found in servers, data centers, and personal computers, where they help manage data processing and storage.
- Wearable Technology: Wearable devices such as smartwatches, fitness trackers, and health monitors use PCBAs to integrate various sensors and connectivity modules in compact formats.
- Energy Sector: PCBAs are used in energy applications, including solar inverters, battery management systems, and control units for wind turbines.
- Consumer Robotics: Home robotics like vacuum cleaners and lawn mowers, as well as educational robots, incorporate PCBAs to handle various tasks autonomously.
Conclusion
Mastering PCBA is essential for the production of reliable and efficient electronic devices. By understanding the complexities of the process and implementing best practices, manufacturers can ensure high-quality outputs and minimize production issues into the blank circuit board. Whether you’re a seasoned electronics manufacturer or a newcomer to the field, understanding PCBA is critical to the success of your electronic projects.