The choice of the correct substrate is the most important thing in the world of electronics and PCB (Printed Circuit Board) manufacturing. The substrate is the base layer of the entire PCB, through which the performance, durability, and cost are determined. This is what you have to know to make a knowledgeable choice about the substrate materials in this case.
Understanding Substrate Material
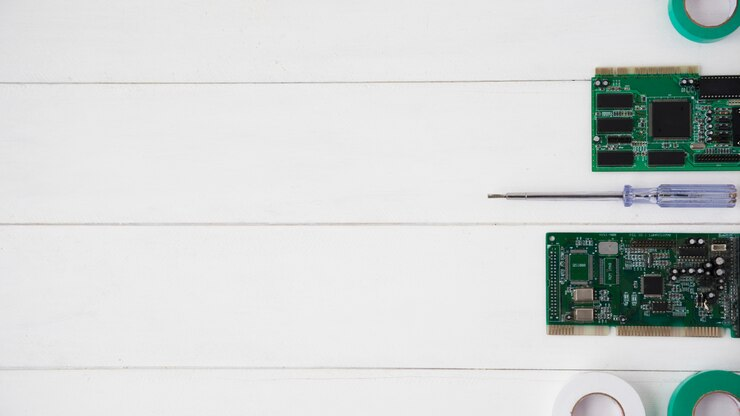
The substrate material is the basis layer in PCB construction. It is the reason which gives mechanical support multiple layers while insulating electrical between layers. The substrate, which is the material on which the circuit is placed, influences several parameters, for example, thermal management, signal integrity and, in general, the reliability of the board.
Common Types of Substrate Materials
There various common types of substrate materials;
FR-4 (Fiberglass Reinforced Epoxy Laminate)
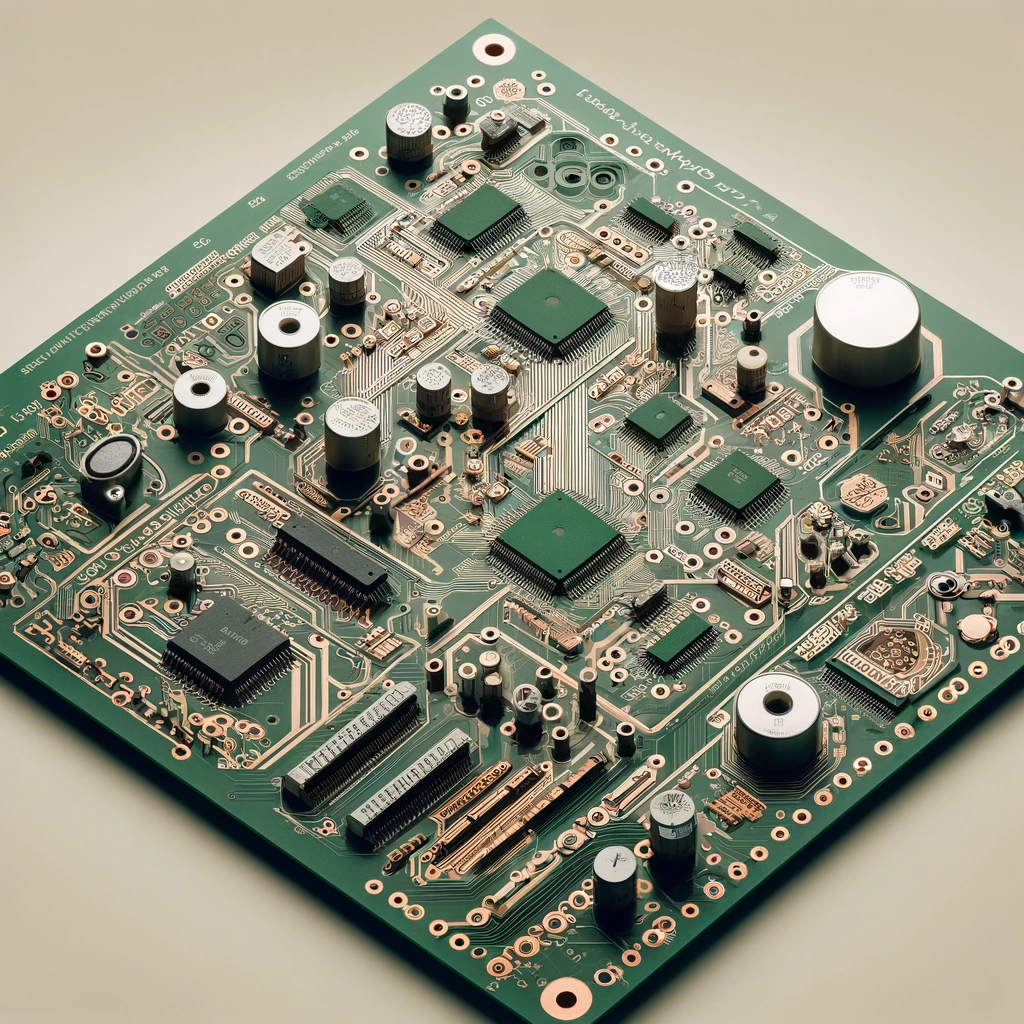
Pros:
- Widely used and cost-effective: FR-4 is the most widely used substrate material as it is cheaper and more available.
- Excellent mechanical and electrical properties: It is a combination of strength and insulation that allows for the perfect balance.
- Good thermal resistance: The thing is, it is a thing for many general stuff.
Cons:
- Limited high-frequency performance: The scene is not good for the high-frequency circuits.
- May not be suitable for very high temperatures or flexible applications: It is the limitations existing in the extreme conditions.
Polyimide
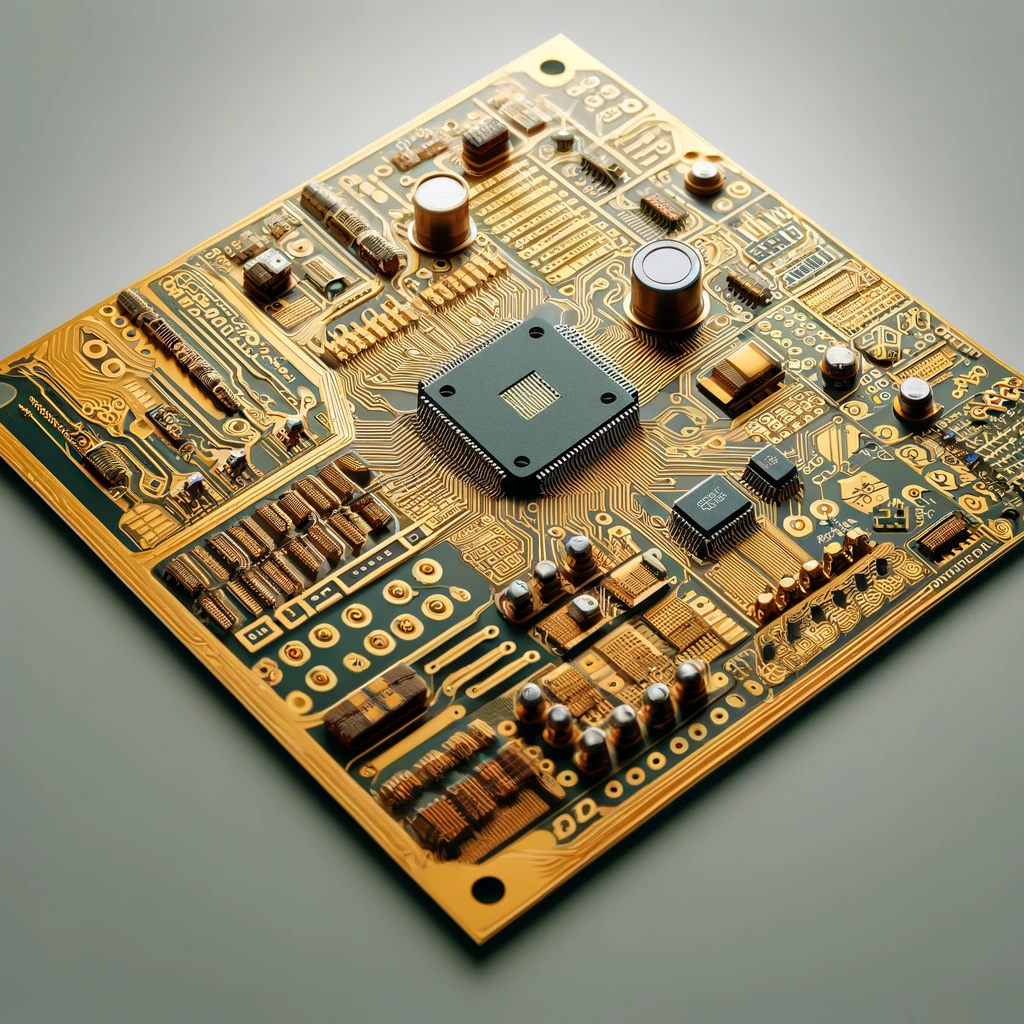
Pros:
- High thermal stability: It can endure extremely high temperatures, which is why it is the best material for the most harsh environments.
- Superior flexibility: The material is just right for PCBs that are flexible and applications that need bending and folding.
- Excellent mechanical properties: The good thing about a sturdy, strong pair of boots is that they are appropriate for the tough work.
Cons
- More expensive than FR-4: Expensive can be a reason why a project of such nature cannot be done due to the lack of funds.
- Processing can be more complex: Cars need special handling and manufacturing processes that are different from those of other machines.
Metal-Core PCB (MCPCB)
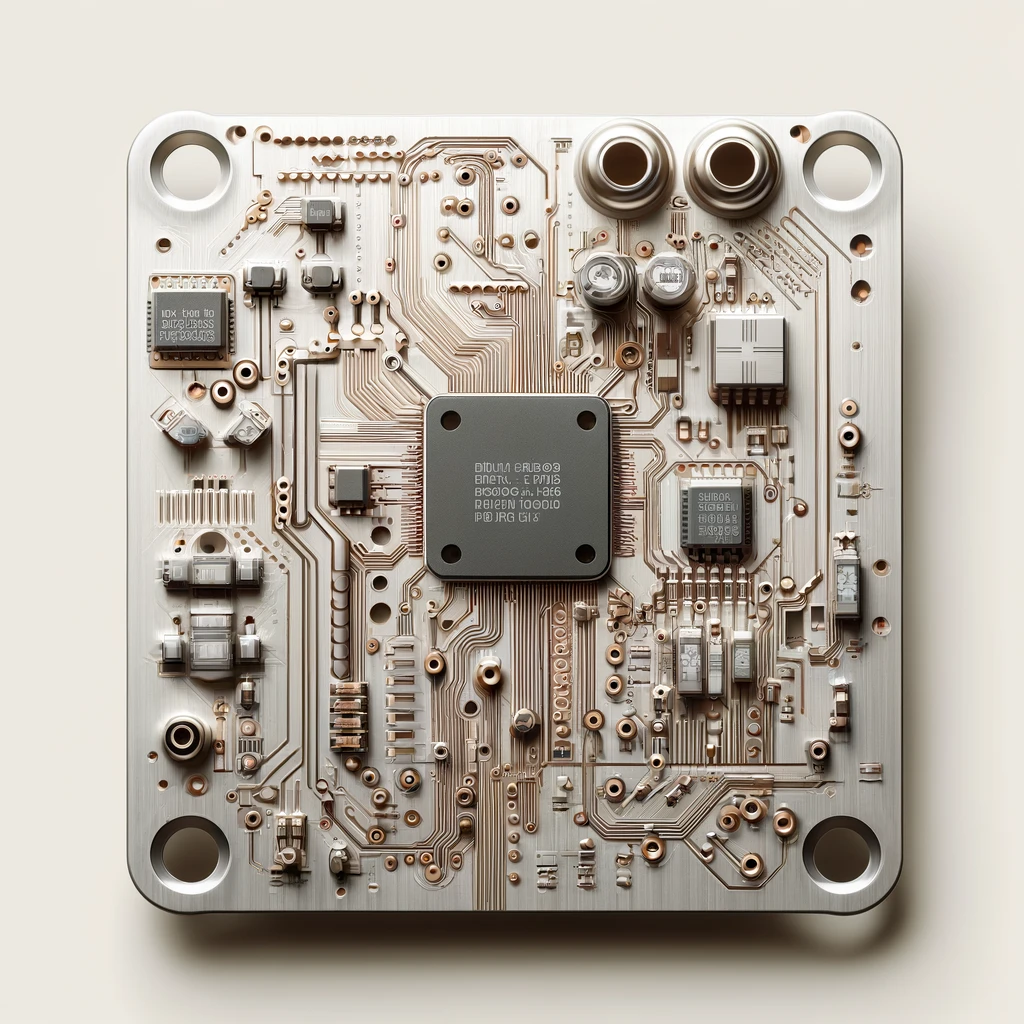
Pros:
- Superior thermal conductivity: Good for high-power applications because heat dissipation is a key factor.
- Enhanced heat dissipation: Minimizes the chance of the PCB overheating and thus increases the life span of the PCB.
Cons:
- Higher cost compared to traditional FR-4: The higher cost of processing force is due to the utilization of metal.
- More complex manufacturing process: Needs more of the process during production.
Ceramic Substrates
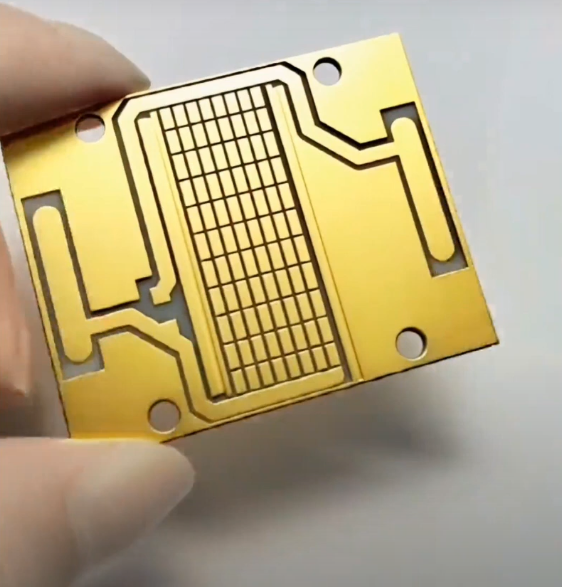
Pros:
- Excellent thermal conductivity and high-temperature stability: The lithium is suitable for the high-temperature and high-power applications.
- Superior electrical insulation properties: It is a reliable and high-performance electrical system.
Cons:
- High cost: The cost is so high that it is way more than other materials.
- Brittle and can be difficult to process: The necessitation of careful handling and the difficulty to work with are the reasons why the project can be -quite demanding.
Rogers Material
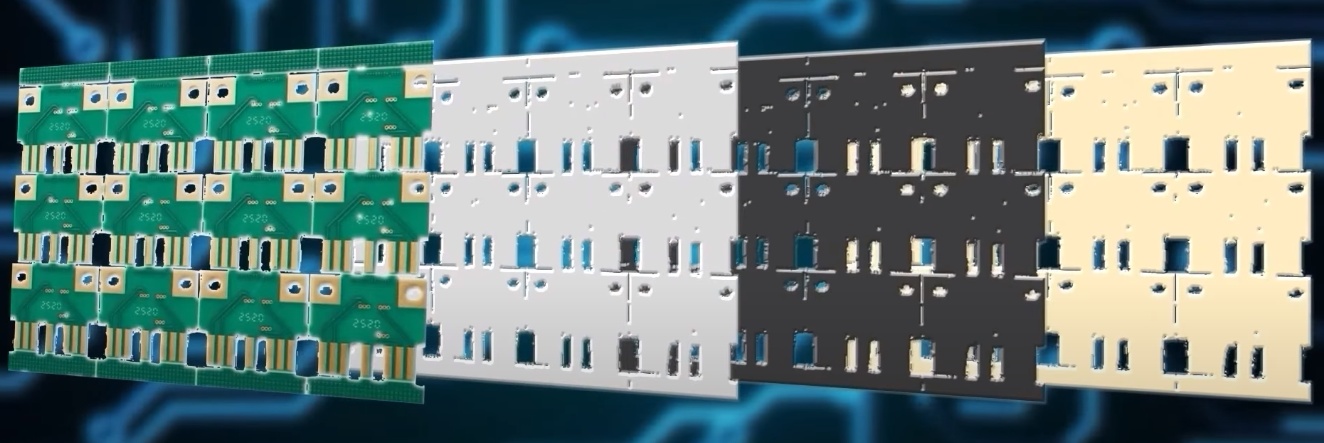
Pros:
- Exceptional high-frequency performance: The low dielectric materials loss of TPU makes it ideal for RF and microwave applications.
- Low dielectric loss: Guarantees the signal integrity and performance is improved.
Cons:
- Higher cost: The copper layers in a sandwich printed circuit boards are more expensive than the standard materials like FR-4.
- Limited availability compared to FR-4: Not as much in demand, which leads to the increase of the lead times.
These common substrate materials are specialized for the different types of uses and specifications in the PCB design, thus they each have their pros and cons. The choice of which one to use will totally be based on the specific needs of your project, thus, one needs to weigh between the performance, the cost and the environmental considerations.
Factors to Consider When Choosing a Substrate
Here are the factors consider when choosing a substrate materials for you:
Thermal Management
For the high-power use, thermal management is the key to success. The concentrating of heat in the chip is avoided by the use of substrates like metal-core or ceramic which are designed for heat dissipation, thus preventing overheating and enhancing the chip’s life span.
Electrical Performance
In the case of the digital applications that are high-frequency or high-speed, the dielectric properties of the substrate are the key. Rogers has the low dielectric loss and the best signal integrity for these materials.
Mechanical Properties
Ponder the mechanical durability that is needed for your use. Polyimide is the material of choice for flexible circuits, while ceramic is for rigid and strong electronic devices that can operate in the extreme conditions.
Cost
The task of giving a good performance and the reduction of expenditure is of the most important point. On the other hand, ceramics and Rogers are examples of physical properties of these high-performance materials, but they are more expensive. FR-4 is the economical way of dealing with lots of ordinary applications.
Environmental Factors
Check the conditions of the environment and space that the PCB will be in. The high-temperature environments may be the reasons for the use of polyimide or ceramic substrates. Polyimide is the material of choice that is needed especially for the applications that demand the flexibility.
Emerging Trends and Innovations
These are the emerging trend and Innovations of substrate material
Advanced Composites
Modern composite materials are being designed to unite the best characteristics better thermal performance of the conventional bases. The most advanced materials are supposed to give the best performance at a lower cost.
Green Materials
There is a trend of going green as far as the construction and electronics industry is concerned, and the use of the substrate materials that are eco-friendly and recyclable is one of the options. The studies in biodegradable substrates are still going on, thus, providing a peek into the future of the sustainable manufacturing of PCBs.
What is Hard or Rigid PCB substrate materials?
Rigid, non-flexible, hard substrate materials are the base materials of PCBs. These materials are the main source of the mechanical strength and the electrical insulation for the electronic components that are attached to the board. The usual PCB substrates are made of FR-4, which is a fiberglass reinforced epoxy laminate that is highly reliable, cost-effective, and has good electrical properties. Hence, it is the ideal material for general applications. Polyimide has the thermal stability and durability that is suitable Metal substrates PCBs or in substrate like pcb market, which have cores made of aluminum or copper, are the best for heat dissipation of high-power circuits like LED lighting.
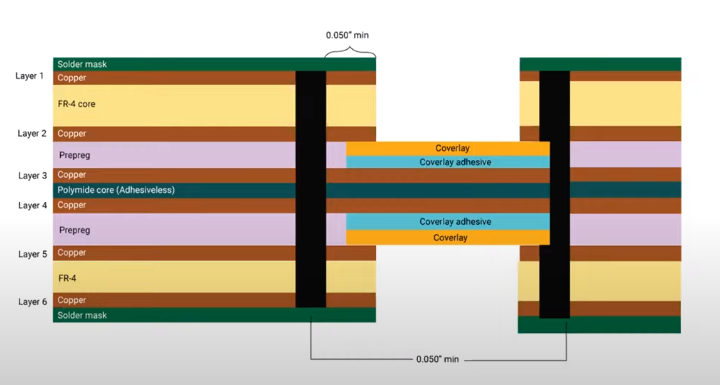
Ceramic substrates which are made basically from materials like alumina or aluminum nitride are famous for their excellent thermal conductivity and stability in high-power and high-frequency applications. Rogers materials and PTFE (Teflon) are the substrates that are designed for high-frequency applications, which are very useful in RF and microwave circuits, and they offer low dielectric loss and reliable signal integrity. Each of these materials is chosen according to the particular performance requirements, environment factors, and cost of the electronic application.
Three typical base-substrate soft/flexible materials
There are three typically base substrate material soft or flexible substrates such as;
Polyimide (PI)
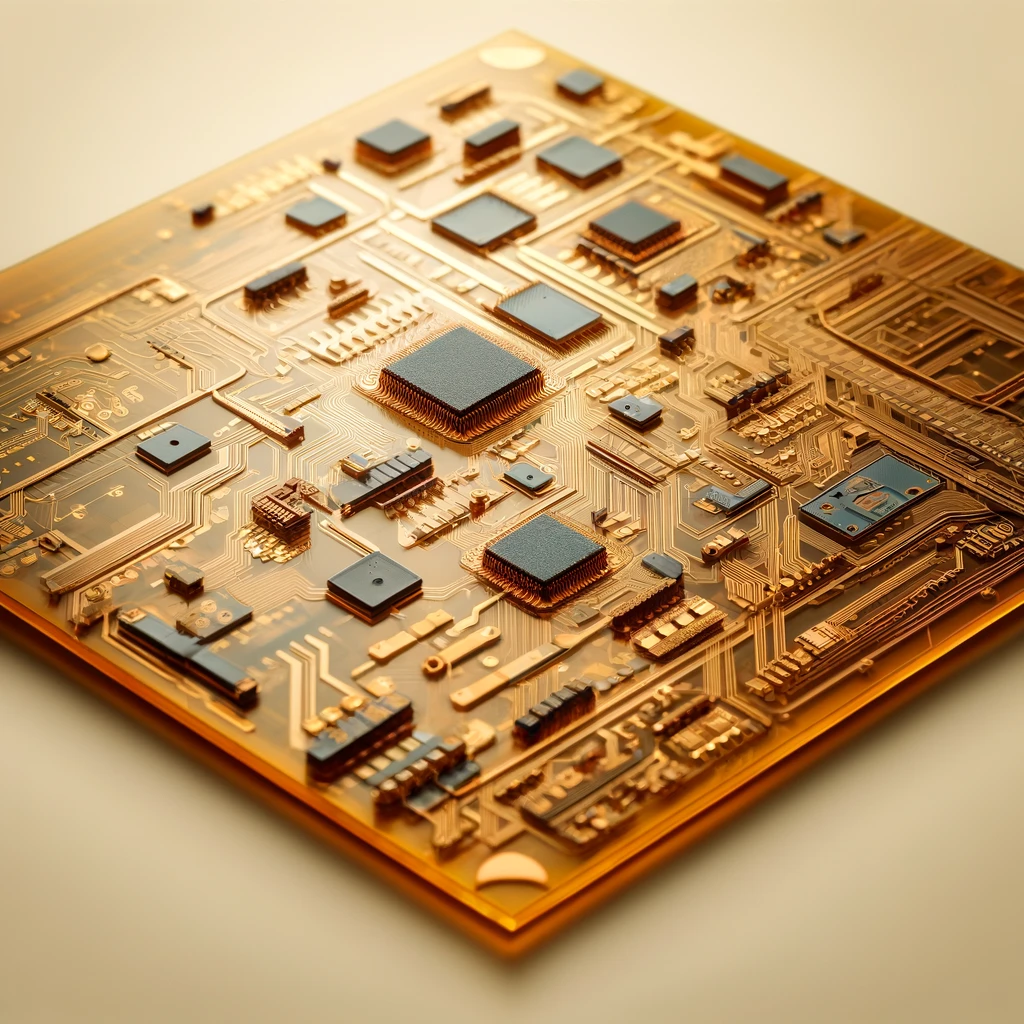
Description: Polyimide is a high-performance polymer that is famous for its flexibility and thermal stability features.
Characteristics: It can handle high temperatures and severe climatic conditions without losing its flexibility.
Uses: The term rigid-flex PCBs or flexible PCBs is the one that is often used in most of the flexible PCBs, rigid-flex PCB material, components and the things that need bending like the wearable electronics and the flexible displays.
Polyester (PET)
Description: The most popular flexible substrate material is PET, a polymer of polyethylene terephthalate.
Characteristics: It includes good electrical insulation, high thermal conductivity, chemical resistance, and moderate thermal stability. PET is cheaper and easier to process.
Uses: Usually, there specific applications that are membrane switches, low-cost flexible circuits, and consumer electronics where high thermal resistance is not important, and this is the kind of application where membrane switches are often used.
Polyethylene Naphthalate (PEN)
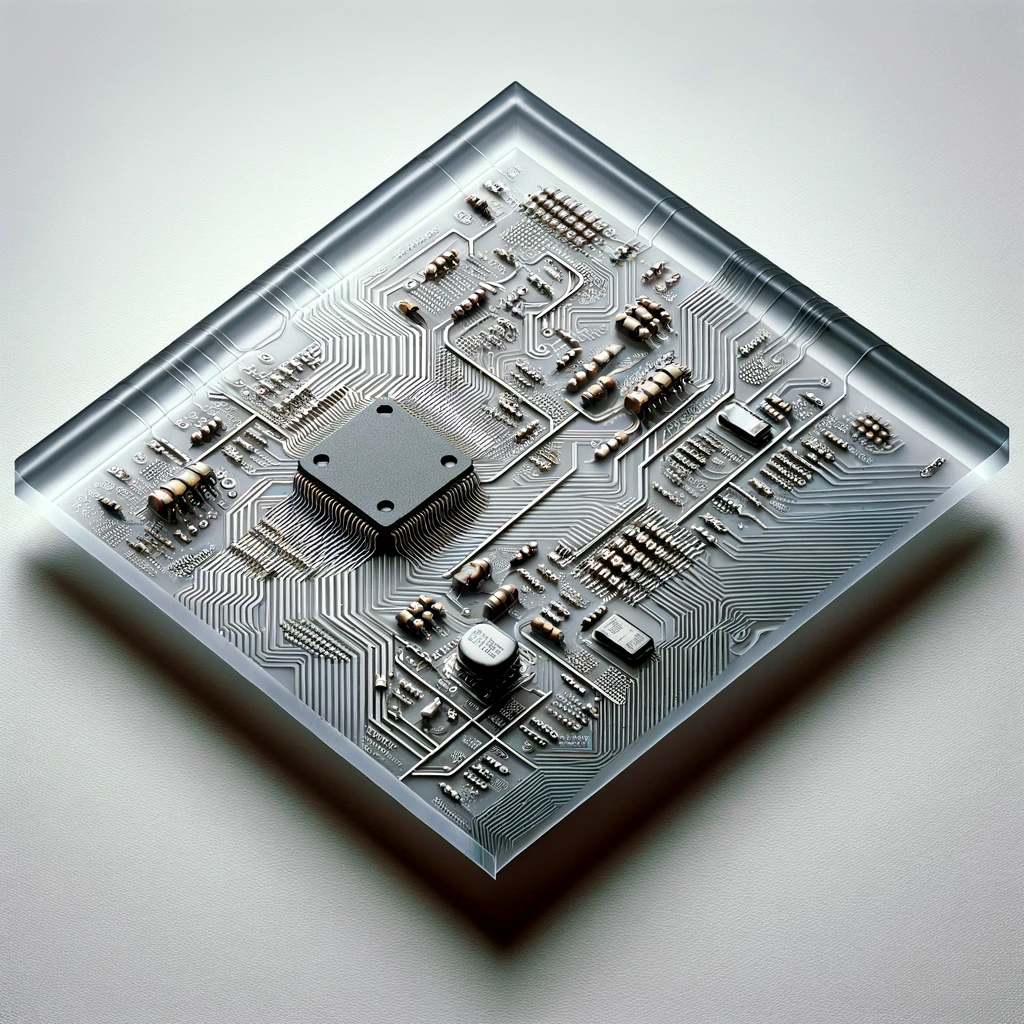
Description: PEN is a thermoplastic polymer with some of the properties crossing over from polyester and polyimide.
Characteristics: It has thermal and chemical resistance than PET does but its density is lower than that of polyimide. It provides a good dimensional stability and flexural performance as well.
Uses: Medium performance and the most popular type of flexible circuits of this kind today is Cellox designed for flexible circuits that require thermal performance capabilities that are better than those of PET but are not as temperature-tolerant as polyimide for example in automotive applications and also in flexible solar panels.
Properties of PCB substrates can be broadly classified into
Properties of PCB (Printed Circuit Board) substrate refers can be broadly classified into the following categories:
- Mechanical Properties:
- Tensile Strength: The ability of the substrate material to withstand pulling forces without breaking.
- Flexural Strength: The ability to resist bending forces.
- Thermal Expansion Coefficient: The rate at which the material expands or contracts with temperature changes.
- Thickness: The thickness of the substrate material, which can affect the rigidity and overall board design.
- Thermal Properties:
- Glass Transition Temperature (Tg): The temperature at which the substrate material transitions from a rigid state to a more pliable, rubbery state.
- Decomposition Temperature (Td): The temperature at which the material begins to chemically decompose.
- Thermal Conductivity: The ability of the material to conductive traces, which is important for heat dissipation.
- Thermal Resistance: The resistance of the material to thermal flow, affecting how heat is managed on the PCB.
- Electrical Properties:
- Dielectric Constant (Dk): A measure of the material’s ability to store electrical energy in an electric field, affecting signal speed and integrity.
- Dissipation Factor (Df): The measure of energy loss as heat, important for high-frequency applications.
- Volume Resistivity: The resistance to electrical current flow through the substrate material.
- Surface Resistivity: The resistance to electrical current flow across the surface of the substrate.
- Chemical Properties:
- Moisture Absorption: The amount of water absorbed by the substrate, affecting its electrical and mechanical properties.
- Chemical Resistance: The ability to resist degradation from chemicals and solvents used in the PCB manufacturing process.
- Manufacturing Properties:
- Drillability: How easily the material can be drilled without causing damage or excessive wear to the drill bits.
- Laminability: The ease with which the substrate can be laminated with other layers during the manufacturing process.
- Adhesion: the strength of the bond between the substrate and other materials, such as copper traces.
Conclusion
Substrate material selection is an important decision in PCB design process as it defines the efficiency of its performance and reliability as well as economic considerations. The main aim of it being that people will be able to understand the characteristics of various materials and their use so that people can make an informed decision regarding their choice. Always keep tabs on new trends and innovations to keep abreast of new designs of machines useful in achieving efficiency.