Explore with us into the labyrinth of Surface Mount Technology (SMT) as we head off into the depths of its inner workings. By our in-depth guide, you will become aware of different theories, practical techniques, and recent breakthroughs required for Electronics SMT. From understanding the fundamentals to executing the advanced techniques, our detailed route will guide you in digging out the source of power from SMT. Whether you are a beginner or an experienced engineer, this all-in-one guide has everything you need to be knowledgeable in electronic production.
What is SMT?
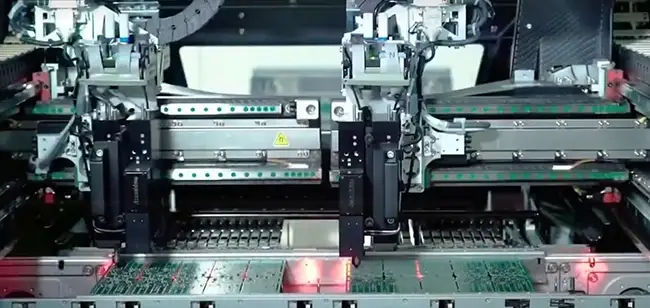
Surface Mount Technology (SMT) refers to surface mount process, a technique used in electronics manufacturing to solder parts in a printed circuit board (PPC). While, in through-hole surface mounting technology, components as the ones which have the leads inserted into the holes on the board are used, the SMT parts are instead positioned directly onto the board’s surface which enables a space-saving design and a higher packing density because of that.
The SMT parts are generally smaller and lesser in weight when compared to the ones used in through-hole technology and this reward manufacturers by the creation of more compact and light weighted devices. SMU liner circuit is made of smaller components made up of resistors, capacitors, diodes, integrated circuit packages and many electronic components.
The process of surface mount technology involves several steps:
Component Placement:
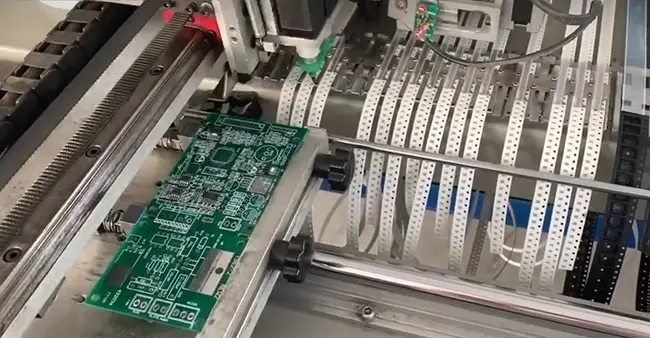
SMT devices are picked off reels and tray by automated machines and then they are set accurately to the design pattern.
Solder Paste Printing Application:
Solder paste, a viscous liquid containing both flux and solder balls of the smallest size, is spread on the pads of the PCB in which these components will be placed.
Reflow Soldering:
The PCB containing reflow soldering components and then, smc and solder pads are then conveyed into a reflow oven. In this furnace, molten solder pulls components forming solder joints by imparting a strong electrical solder connections as we as mechanical connection between the components and the board.
Inspection:
Solder is then placed on the PCB, which is then inspected to determine if all the components have been properly put in place and soldered. Automated visual check, automatic automated optical inspection (AOI) or X-ray inspection may be included.
Testing:
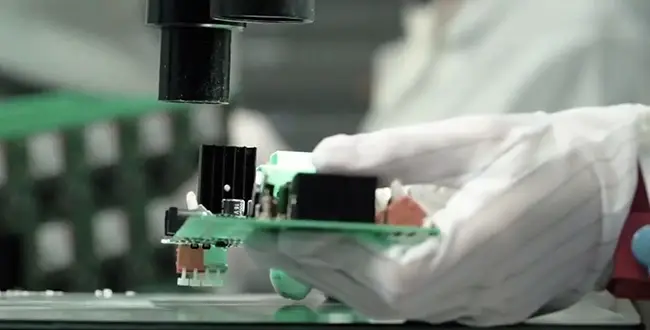
Once the PCB assembly is finished, it may be checked to see if it’s working efficiently.
SMT has now become the principal way of producing electronic semblance because of its benefits of the rate, accuracy and budget. It will lead to the computerized automated processes, decrease in the manufacturing time, and to the production of more complex electronic circuitry devices.
What are the Types of Surface Mount Components?
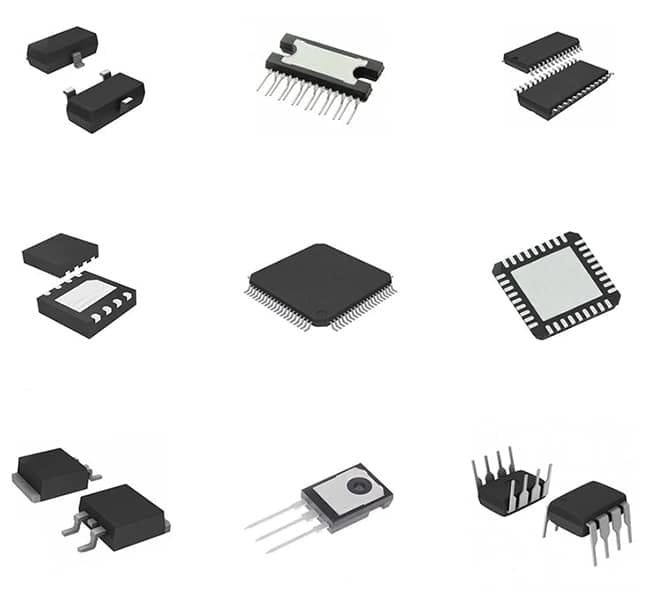
Surface mount components (SMCs) are electronic components that are designed to be surface mounted devices, directly in the surface of a printed circuit board (PCB), as opposed to through-hole components that are inserted into holes drilled in the PCB. Surface mount technology (SMT) enables mounting of SMCs, which are chip circuit devices, onto the surface of a PCB, by contrast, through-hole technology involves drilling of the PCB to insert them to the PCB, while in SMT, drilling is not necessary. Surface mount technology has different types of surface mount components where each component
has its specific use in various electronic circuits. Here are some common types:
- Surface Mount Resistors (SMD Resistors): They are surface tension resistors, specifically meant to be positioned on a printed circuit board. They can come in different sizes and shapes, for that their resistance values will be indicated with color codes or printed directly on them.
- Surface Mount Capacitors (SMD Capacitors): Surface mounting type of capacitors is capable of supplying energy for the storage and then releasing it again into electronic circuits. Various forms available such as the ceramic, tantalum and electrolytic ones.
- Surface Mount Inductors (SMD Inductors): Inductors of this type are manufactured so that they can be mounted onto the surface of a PCB. They give the space for energy in magnetic field, which are frequently used in filters, oscillators, and power supplies.
- Surface Mount Diodes (SMD Diodes): Diodes are the components which use current to flow in one direction only and are served in rectification, switching, and signal demodulation in various types of circuits. Surface mount diodes are intended to be directly mounted onto the PCB assembly as their design suggests.
- Surface Mount Transistors (SMD Transistors): Transistors are semiconductor elements that are responsible for increasing or switching electronic signals. Surface mount transistors come in various category from NPN via PNP to MOSFETs and JFETs.
- Surface Mount Integrated Circuits (SMD ICs): Small Outline Integrated circuit (ICs) are very advanced and compact circuits that have many components mounted on a single chip. Generally, integration circuit surface mount ICs are massively employed in numerous electronic products, including microcontrollers, memory devices, and amplifiers.
- Surface Mount LEDs (SMD LEDs): LEDs or light-emitting diodes are the semiconductor devices where light energy is produced when current passes through them. LCDs are the dominant display technology for desktops, televisions, and tablets.
- Surface Mount Switches and Connectors: These constitute some kind of switches such (e.g., tactile switches) and connectors including USB connectors, HDMI connectors which are made compatible with the surface of PCB.
These are the most frequently encountered among the surface mount components for electronic devices. The different process techniques related to surface mounts are each unique with their own specific features and applications. Taken together, they and surface mount assembly are critical in all modern electronic designs because of the fact that they utilize less space and are very friendly pcb manufacturing process.
When to best use SMT Components?
The surface mount technology (SMT) parts are the standard parts most the electronic devices employ not only because of their advantages over the through-hole parts but also for their blending nature with other advantageous aspects of the modern-day electronics.
Here are some scenarios where using SMT components in electronic assembly is advantageous:
- Miniaturization: Nowadays the size of SMT components are extremely smaller than their ultimate through-hole embodiment, so it greatly affects on the miniaturization of electronic devices. Such situation brings profit to the producers of the portable electronics, wearables, and these compact devices where space is a significant limitation.
- High-Density Packaging: SMT components can be put as closely side by side onto the PCB surface instead of aspering through the holes on through-hole components. It saves significant amounts of space enabling more complex circuit designs and higher functioning assemblies in small places.
- Automated Assembly: The SMT components comprise electronic parts which are integrated through bulk automated assembly processes injecting pick-and-place systems. This leads to disk manufacturing in a side by side manner with much less and efficient process as compared to through-hole assembly that is done manually and by hand.
- Improved Electrical Performance: SMT components show improved high-frequency features because of lead lengths and reduced parasitic capacitance and inductance thereby also result in better frequency response. This ensures that they are applicable for signals in which high-speed transmission is needed, like in telecommunication and data centers.
- Enhanced Thermal Performance: SMT components has lower heightening footprint than through-components allowing for more operational heat migration. It also becomes critical as a device operates in demanding operating environments or packing higher power density.
- Lower PCB Manufacturing Costs: Automated placement of SMT components replaces the need for human labor and consequently speeds up the manufacturing process by outpacing the conventional methods, thus decreasing the manufacturing costs. And, adding to this in smaller size and weight of SMT pieces in order to achieve the materials cost and shipping expenses, saving is also possible.
- Improved Reliability: SMT modules frequently boast better mechanical stability and shock resistance, as they are mainly receptive to external forces only from the side. This contributes to the life and reliability of electronic devices, especially the ones that sees bumps or vibration.
- Design Flexibility: SMT devices are available in various forms that vary on the size, shape, and formats, thereby giving engineers more options to play with while designing. Since they can be placed at both sides of a single print circuit board, they prevent the waste of the area on board as well as make a way for intricate multilayer designs.
Without a doubt, SMT modules as the building blocks for the same were all about the size, weight, cost and performance issues of the design. Their adoption of services across various industries plays a role which accentuates their significance in this industry.
What are the Soldering Techniques in SMT Components?
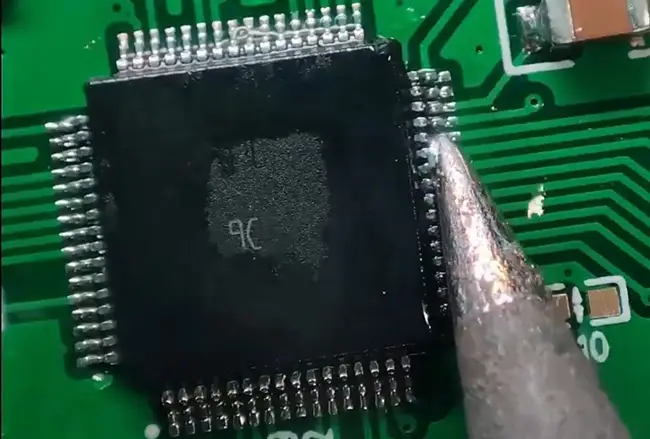
SMT components with tiny appendages are much prone to technical errors and disconnection of the small components to the PCB should be used.
Here are some common soldering techniques used for SMT components:
Reflow Soldering:
Reflow soldering is the mainstream technology, which should be SMT components providing SMT components to PCBs. Silkscreening is a method whereby a solder paste is automatically dispensed through a stencil on the pads of the PCB board using solder paste printers. The components will then have to be spread onto the solder paste. The solder paste is next thermally profiled with the reflow oven. When all solder paste melts, it forms solder joints which will bond the components to the circuit board. Reflow soldering machine techniques is effective for large batch productions as well as being capable of concurrent soldering of multiple components.
Infrared (IR) Soldering:
Infrared soldering uses electromagnetic radiation with a wavelength of the thermal radiation emitted by heated solder paste and components. With infrared soldering systems, where heat is directly concentrated on the solder joints opposite to reflow ovens which dip the entire assembly process, speedier heating and cooling cycles are realized. IR soldering is applied to the rework of SMT assemblies and to R&R providing temperature control which is necessary for doing precise thermal operations.
Hot Air Soldering:
An alternative to both hot air and fume extraction is hot air soldering, or hot air rework, which involves using hot air flowing through to melt the solder and reflow the SMT components. This process is generally applied to remove unwanted material and rework to repair small areas like changing or reassembling of individual components or rectifying solder defects. The thermal soldering stations include the heat regulation with temperature and wind settings for precise control of the soldering process.
Vapor Phase Soldering:
Vapor phase soldering relates to the entire assembly of the PCB being immerse in a cloud of solvent made from low boiling point fluorinated substances. Instead of being gas, the soldering medium will condense directly on PCB, at the same time releasing latent heat and affecting the normal melting of the solder paste and the formation of solder joints. While the vapor-phase technology has a uniform heating effect and is characterized by being able to reduce the thermal stress applied on the components, it is best suited for sensitive electronic processes.
Wave Soldering (Selective or Mini-wave):
Traditionally used for processing of leaded components, through-hole soldering techniques could also be made suitable for some SMT parts if selective or mini-wave soldering methods are used instead. With selective wave soldering the solid state solder is imparted only to the those PCB areas where through-hole components are mounted furthermore the soldered molten solder wave is also applied to the SMD components. Sourcing this equipment is either to assemble SMT and through-hole components in the case of a mix of the two techniques or for soldering only SMT assembly components on one side of the PCB.
Such soldering techniques that printer applies solder paste can be classified into some main categories that are used for various soldering processes of SMT parts. Assembly technique selection is based on the things which are involved, like the process tasks that need conducting, production volume, joint quality desired, and equipment required.
Why is solder paste an important factor in SMTs?
Solder paste plays a critically important part of surface mount (SMT) assembly manufacturing. Solder paste is the volume held in which case solder alloy micro-particles and flux, which is a cleaner of chemical contain. Here’s why the solder paste volume is an important factor in SMT assembly:
- Component Attachment: Solder paste like a glue tends to bond the chips to the printed circuit board. In the course of making, the solder paste is put on the pads of board and stencils are made use of as the applicators. Components are put onto the solder paste once it has been put onto the circuit board, and consequently through reflow soldering, the solder paste will melt which results in formation of solder joints that mean the components are securely linked to the board.
- Facilitates Reflow Soldering: The solder paste during the reflow soldering process will melt and result in the solder joints which are electrical and mechanical connections between the module components and the PCB. The fluid within the solder paste is one of the factors that help the metal surfaces to remove oxides and contaminants from the surface, ensuring the solder fluid gets wetted and adheres well to the component leads and PCB pads during reflowing.
- Fine Pitch and High-Density Assembly: Miniaturization and higher component density in modern electronics leads to more fine pitch parts with small solder size as part of the design. The quality of final product varies depending at solder paste on which solder is accurately laid on small pads and the joint reliability even in high-density assembly.
- Stencil Printing Control: Solder paste consistency and viscosity is crucial for the stencil printing method, otherwise known as the process of placing solder paste on the PCB pads via a stenciling. Correct viscosity is a critical factor that determines either solder paste applies well and consistently onto the pads, which would in turn eliminate the defects like the solder bridge or inadequately solder.
- Flux Activity: The stirring in the solder paste not only removes the oxide and the contaminant from the surface but it eases the wetting and flow in the solder process during reflow soldering. The balance of the flux activity is a key factor for the obtaining of credible soldering connection and solder balling, voids or tombstones defects prevention.
- Compatibility with Component and PCB Materials: Soldering paste should stay compliant with the materials used in both the components and the PCB as this is a guarantee of the solder joint’s quality and will avoid solder cracking or delamination. Solder paste designs are made for certain kinds of applications and material composing.
- Process Control and Quality Assurance: Inspection into the quality of solder paste including particle size distribution, flux activity and viscosity is one of the key principles ensuring a steady pcb assembly process. The accurate storing and using of solder paste are also of necessity to maintain the stability through the equipment performance.
Of all variables used in the Surface Mount Technology process, solder paste plays a significant role in this whole process, allowing precise electrical component and attachment, reflow soldering, fine-pitch assembly, stencil printing control, flux activity, material compatibility, and process control. Solder paste leads the way when searching best one to achieve the desired quality and reliability of surface mount devices (SMD) and the surface mount technology (SMT) remains.
What is the difference between SMT & SMD?
SMT (Surface Mount Technology) and SMD (Surface Mount Device) are related but distinct terms in the realm of electronics manufacturing:
Surface Mount Technology (SMT):
- SMT represents the whole part of in collision with electronic elements mounted onto the surface of printed circuit boards (PCBs) or substrates.
- It saves time and space compared to the board drilling and lead pitch processes since components are attached on the board’s surface without the use of holes and leads using solder.
- Semiconductor manufacturers employ SMT to create highly compact, featherweight, fast, and cost-efficient electronic components by means of using higher mount precision and automated assembly processes.
Surface Mount Device (SMD):
- This SMT stands for the small form factor conventional assembly and components other parts that are designed for surface mounting.
- Basically micro-component comprise small and flat electric connections having signals controlled by soldered metal contacts or pads on their back allotments.
- Traditionally, SMD components include resistors, capacitors, diodes, transistors, ICs (ICs), and other types.
- SMD components are designed to be installed directly to a PCB surface in due course of SMT process.
To simplify, SMT is exactly the whole technology and process of the PCB components without the leads incoming onto the PCB, meanwhile the SMD is the specific design of the components already for SMT. SMD elements are part of the SMT assembly process and cannot be missed.
Why Original Equipment Manufacturers (OEMs) should care about the SMT manufacturing process?
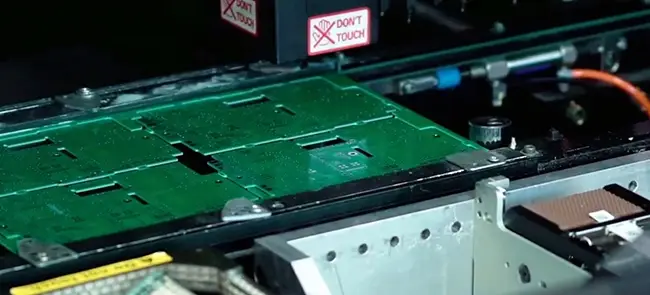
Original Equipment Manufacturers (OEMs) should care about the Surface Mount Technology (SMT) manufacturing process for several reasons:
- Cost Efficiency: SMT manufacturing has a vital benefit over the use of the through-hole technology in that the materials, labor and the assembly time are the features. Manufacturers may enhance their automation level while cutting production stepflow and thereby cutting costs as well.
- Space Savings: SMT component packages occupy less space on PCBs by being small and lightweight similar to THR components, thus permitting creation of the smaller but functional systems. This is particularly significant for devices where the physical space is limited, such as mobile phones, notebooks, and watches that you wear.
- Performance: Unlike conventional through-hole components, most SMT assembly components feature reduced parasitic inductance and improved high-frequency performance. They have high permittivity and dissipation factor making them a preferable material in fast speed and high frequency devices like microwave equipment, computer network equipment, and automotive electrical devices.
- Reliability: SMT assembly components enjoy shorter lead formation rather than the longer conductor in traditional wire length. This short lead formation has a lower parasitic capacitance and inductance. To this effect, there can be improvement in signal fidelity and reliability, especially in terms of wide bandwidth and high frequency applications. Another key benefit is the fact that SMT assembly components show tolerance to mechanical stress and vibration disturbances, and hence can be used in harsh conditions where through-hole parts cannot stand either of these.
- Flexibility: SMT manufacturing offers the opportunity for the designers to have the freedom to come up with more design ideas to test and fast prototyping. Manufacturers have the advantage of enabling the use of more components in a smaller area and allowing components to be placed on both sides of the PCB by way of the SMT technology. This increases the design options for integration and optimization of performance, cost and space utilization.
- Industry Standards and Trends: The electronics industry development keeps changing and SMT machines are firmly established as the prevalent choice for PCB assembly. Usage of SMT processes together with OEMs not only makes it possible to join the industry standards but also be considered among the best companies in the niche.
- Environmental Considerations: The build up of SMT most often produces less waste compared to the through-hole assemblies owing to the lesser amount of material loss and more efficient processes. It has the same effect with intensifying societal and regulatory paths as we move towards the environmentally friendly manufacturing.
- Supply Chain Efficiency: The majority of electronic components- including chip circuits, resistors, capacitors and diodes- are designed for SMT mounting lines. As a result of the fact that SMT newer mounting technique has much wider range of components than the traditional TH mounting technique. This situation will result in parts having a better availability and pricing, with shorter lead times for OEMs’ supply chains and thereby maximizing their efficiency of electronic assemblies.
To sum up, later OEMs should care about the SMT production process that provides cost-effectiveness, dimensional savings reduce manufacturing costs, higher performance and reliability, design flexibility, alignment with regulations, environmentally friendly, and degrees of supply chain operating. Such benefits are used by OEMs as a fighting instrument in a very tough market of electronic devices and contribute to their competitiveness and success.
Summary
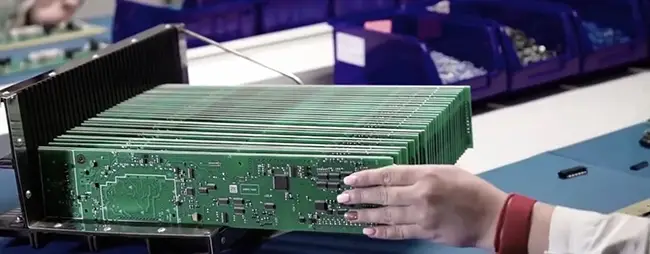
Surface mount technology (SMT) represents a construction technology applied to building electronic circuits, when the components are directly attached on the surface of printed circuit boards (PCBs), differently than being inserted into the drilled holes (as it is in through-hole technology). Include SMT into your assembly process will give you the benefit of figuring out how to miniaturize.
This will help to improve the capability of high-density packaging and the process can be automated and will definitely improve the electrical and thermal performance. You can design the products enabling various flexibility options.
Through the process of soldering, components important electrical components, like resistors, capacitors, diodes, and chip circuits are attached to the PCB, with solder flux application to ensure reflow soldering. It is the most applicatory method of modern electronics manufacturing, if not just the one, which etymologically can be found in smartphones, computers, automotive electronics, etc. due to its decreasing speed and adaptability.