PCBs are the basic infrastructure of electronic gadgets, which provides the capability and connection of the different components. These highly complex panels have significantly grown and evolved to meet the extensive range of design requirements for high-end applications nowadays. Within the realm of PCB technology, Thermal Resistance PCB is one of those innovations to be reckoned with. It has the capacity to increase the performance level and improve reliability, especially in situations where there are strains on PCBs.
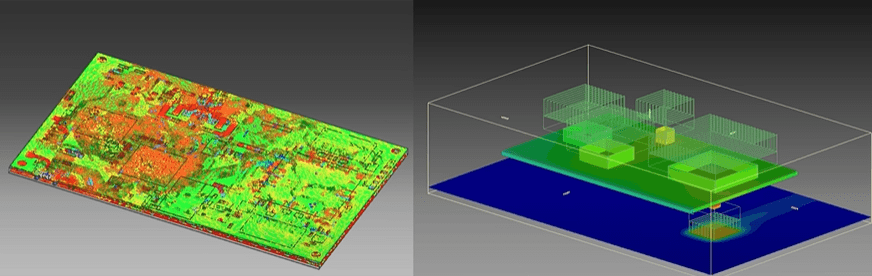
Importance of PCBs in Electronic Devices
Before delving into Thermal Resistance PCBs, let’s first understand the crucial role that PCBs play in electronic devices. PCBs, which are electrical resistance for devices like resisters, capacitors, diodes, and integrated circuits (ICs), come into play in the form of electronic circuits that are present both in smartphones and heavy-duty industrial machinery. They are a stable and organized framework for the components; they ease the electric connections and help to miniaturize and make the design flexible.
I. Understanding Thermal Resistance in PCBs
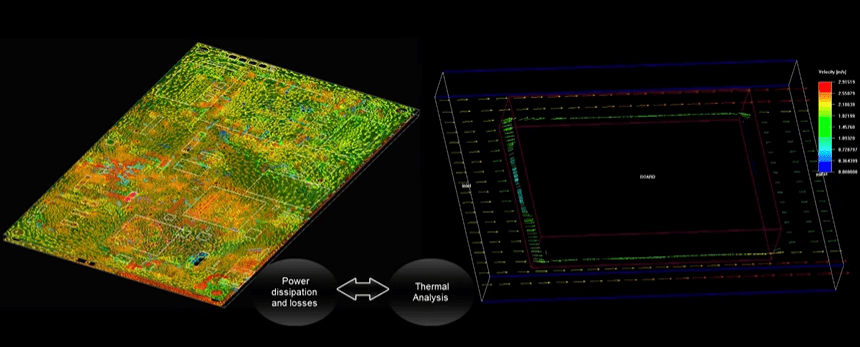
Thermal resistance signifies the material’s capability to keep heat energy from passing through it. Thermal resistance is a major parameter in PCBs that defines how efficiently convection heat transfer can be generated from the electronic components to their surroundings, or heat sinks.
Thermal-resistance PCBs are of great importance for the proper thermal management of electronics, as good performance and safety are relied on. The unit in which it is usually measured is degrees Celsius per watt (°C/W), and it shows how much the component’s temperature, or above ambient temperature, will rise when a given quantity of power is dissipated.
Importance of Managing Heat in Electronic Devices
- Performance Optimization: Extreme heat transfer occurs that can damage the performance of electronics, reducing their efficiencies and making them act incorrectly.
- Reliability: Overall thermal resistance can be harmful to components of the device, which reduces its life as well as reliability and durability.
- Safety: The accumulation of heat can be dangerous, especially in devices used in crucial applications or in places where it is not advisable to have a lot of heat.
- Energy Efficiency: The right heat dissipation promotes energy efficiency as it avoids overheating of components and thus maintains the device at its optimal temperature.
II. How Thermal Resistance PCBs Address Heat Transfer Challenges
Thermal Substrates
PCBs make use of high-thermal conductivity substrates like metal-core PCBs or thermally conductive dielectric materials to enhance heat transfer from components.
Heat Sink Integration
The Thermal Resistance PCB design features surface mounting forms, or heat sinks, and thermal pads that provide considerably larger areas for heat dissipation and enhance equivalent thermal circuits.
Optimized Layout
The arrangement of parts on the PCB Thermal Resistance is tactically installed to distribute heat as evenly as possible and create a correct airflow.
Advanced Materials
The use of superior materials with high thermal conductivity, like copper, and thermal vias for heat dissipation enhances the PCB’s ability to manage an equivalent thermal circuit.
Thermal Management Techniques
Involving the use of thermal vias, copper pours, or thermal pads in the PCB design permits heat transfer to take place more effectively and reduces thermal resistance.
The execution of these approaches makes it possible for parallel thermal resistance PCBs to highly improve the dependability and quality of the electronic goods, particularly in applications where the temperature is excessive or the items are intensively used.
III. Factors Affecting Thermal Resistance in PCBs
Thermal resistance is the key factor that contributes to the functioning of printed circuit boards (PCBs) at their maximum level and the effective performance of high-performance devices, thus increasing their lifespan. Copper resistance is created by sub-factors such as material choices, copper thickness and layout, as well as device position. Knowledge of these factors is the key to the creation of satisfactory PCBs with the best thermal management features.
A. Material Selection
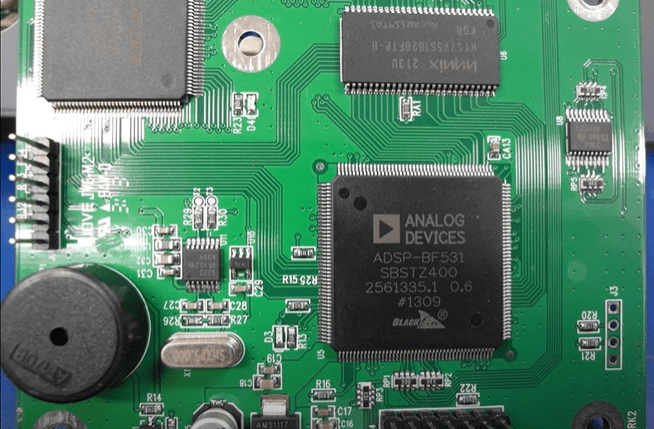
A notable factor is the selection of substrate material, since it plays a major role in the thermal performance of printed circuit boards. Different thermal conductivity properties in different components may affect the excess heat dissipation over the board. undefined
FR-4: This commonly used glass-reinforced epoxy laminate has moderate thermal properties at a relatively low cost. On the other hand, the thermal conductivity of PLA is lower compared to other materials, making it an option for limited cases of heat dissipation.
Metal-core PCBs: consist of a sandwiched metal central core, usually aluminum or copper, between layers of a dielectric material. The metal core improves thermal conductivity, so these kinds of PCBs are excellent for applications that need efficient heat dissipation, like high-power LEDs and power electronics.
Ceramic substrates: Ceramic substrates are famous for this and have very high thermal conductivity, thus providing unmatched heat dissipation ability. They are predominantly used in high-frequency and high-power applications that are sensitive to high maximum temperature.
B. Copper Thickness and Layout
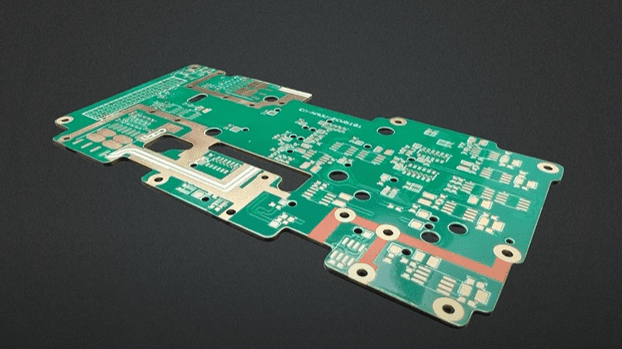
The dimension of copper circuit tracks and the layout of copper on a PCB are two of the main factors that affect thermal conductivity. The comparatively thicker copper layers of the copper-clad laminates provide very good electrical conductivity and thermal conduction. The design of copper layouts, often for power-consuming parts, can help improve heat transfer rates. Strategies like tracing wide routes for high current and utilizing thermal vias for heat dissipation are among the techniques for improving the thermal conductivity of PCBs.
C. Component Placement
This process is mainly about arranging parts on PCBs that come under the umbrella of thermal management. The placement of the heating elements in close proximity may result in hot spots, which will negate the device’s action over time and impair its reliability. The pivotal stage in strategic planning is the placement of components, which is taken from the thermal point of view, thus controlling the heat across the board more evenly.
Strategies for Minimizing Heat Buildup
- Optimize PCB Design: Resort to modeling tools in the early stages of design to simulate thermal performance.
- Utilize Thermal Vias: Thermal vias transfer thermal stuff from components to inner copper layers, which enhances the thermal conductivity of the whole board.
- Heat Sinks and Thermal Pads: When it comes to high-heat-generating components, heat sinks can be a viable option. A heat pad is part of the direct thermal pathway and serves as a means of getting heat directly into the PCB.
- Ventilation and Enclosure Design: Keep the air flowing well in the device’s enclosures and provide enough ventilation for the heat to dissipate.
IV. Thermal Resistance PCB Design Considerations
To achieve high performance in the field of electronics, heat is a vital issue, as it is the key factor for performance and heat generation. Thermal-resistance PCBs are the major factor in successful heat dissipation, that in turn affects the reliability and performance of electronic systems.
A. Heat Sink Integration
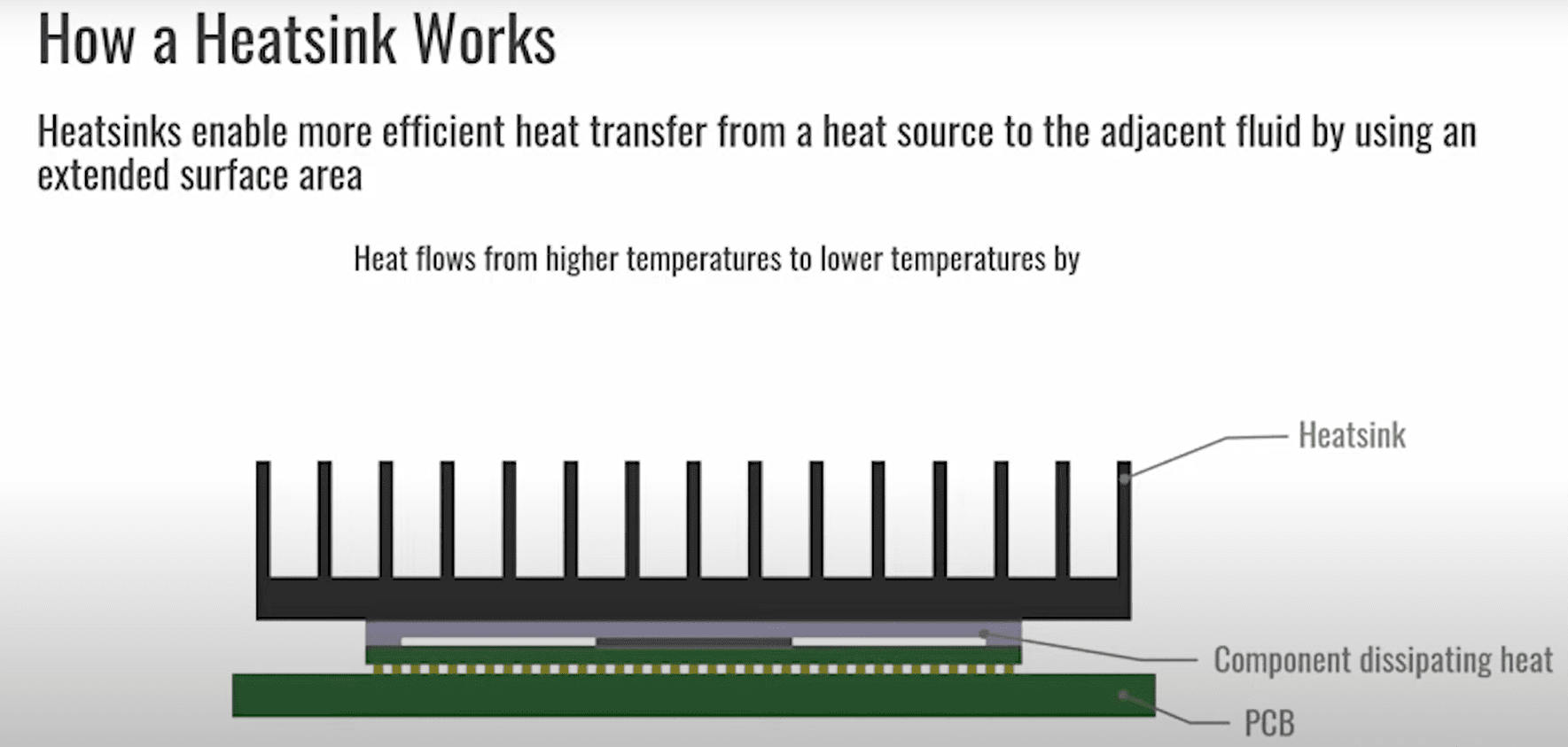
Heat sinks perform a main function of thermal engineering in PCB designs. They assist in dispersing the heat emitted by the electrical components, which could be processors and power transistors, to maintain a safe working temperature level from the heatsink and ambient air temperature.
- Enhanced Heat Dissipation: The heat sink is employed to enlarge the heat transfer area, thus improving the thermal performance of the PCB. It would have a thermal resistance of 1.8 degrees Celsius or above ambient temperature difference.
- Component Protection: This is performed through the drop of ambient temperatures, that consequently leads to higher endurance
- Improved System Stability: The actual thermal runaway prevention process occurs due to proper heat dissipation, while the power station can operate normally with various loads.
Considerations when integrating heat sinks into PCB designs include:
In the process of designing PCBs with heat sinks, compatibility, the use of high-quality thermal interface materials, the choice of the optimal mounting method and the creation of the necessary airflow for the heat to dissipate, especially in compact or enclosed designs, are the main factors that determine the mechanical and thermal resistivity requirements.
Types of heat sinks suitable for Thermal Resistance PCBs include:
Finned-type thermal resistance PCB heat sinks, heat pipes, and liquid cooling systems have been invented for thermal avoidance from the system.
B. Thermal Vias and Pads
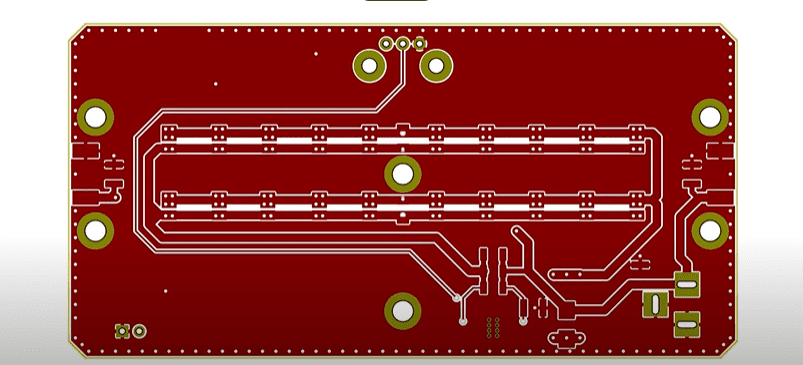
Thermal vias and pads are of the highest priority in the process of heat removal from the heat-generating components to the PCB’s external layers or heat sinks.
Thermal Via Placement: Despite the fact that placement of the thermal vias is one of the essential factors for heat flow,.
Via Size and Density: Figuring out the sizing of the copper and the density based upon the thermal demands of the problem.
Thermal Pad Design: The thermal pad must be designed in such a way that the right dimensions and positioning are ensured so that the contact area and the heat transfer effectiveness are maximized.
Material Selection: Discuss the thermal conductivity of vias and pads in your floorplan configuration.
C. Trace Width and Spacing
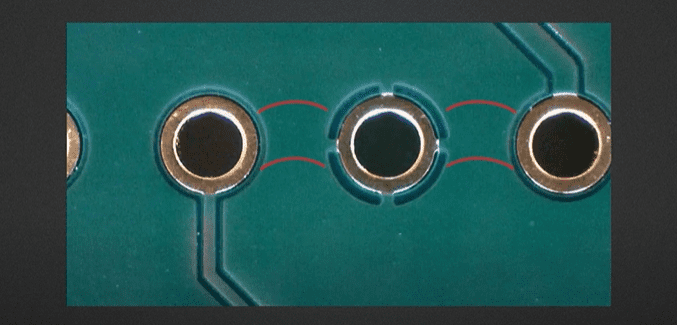
The layout of traces on a PCB plays a huge role in its thermal performance. Minimizing trace width and spacing is able to manifest the effect of heat dissipation; thus, the heat generated is effectively conducted away. Consider the following guidelines:
Wider Traces: For high-current paths and power paths where heat dissipation effect is ensured by making the path wider, resistance will be lowered.
Spacing Considerations: Maintain the spacing between the traces at a suitable distance, especially in the hot areas, to prevent thermal interference and also to enable the heat to dissipate effectively.
Ground Plane Optimization: The installation of a good enough ground plane underneath the high power lines to function as a heat sink and prevent thermal gradients will cause the heat effects to be diminished.
Thermal Relief Design: TAPs (Thermal Arrest Pattern) are used during the baking process for vias leading to major copper areas and power planes to get heat transfer without impairing soldering ability.
V. Testing and Validation
Thermal testing is a major concern in the design of a printed circuit board (PCB) that has good thermal properties for high-temperature applications and efficient heat dissipation.
A. Importance of Thermal Testing
Thermal testing is integral to the development process of Thermal Resistance PCBs for several compelling reasons:
- Performance validation allows engineers to verify the thermal performance of PCB designs in real-world environments.
- Temperature testing helps producers assess material quality.
- Testing provides valuable insights for design engineers to optimize material components.
- Thermal testing ensures compliance with industry thermal management regulations.
B. Methods for Evaluating Thermal Resistance PCBs
Thermal Imaging
Thermal imaging is a non-contact method of visualization and analysis of the temperature distribution on a PCB. The images captured by thermal cameras using infrared rays reveal where there are hot sources and reservoirs, as well as where there are high temperatures.
Simulation Software
Advanced simulation software makes it possible for engineers to model and simulate thermal behavior within PCB designs. These models use mathematical algorithms while predicting temperature profiles, thermal gradients, and heat flow dynamics. Using various scenarios and design trials, engineers can forecast the effects of multiple variables on thermal performance.
Environmental Testing
Environmental chambers are the ones that are used for PCBs to be subjected to temperature and humidity conditions that are controlled, just like the conditions that are found in the real world. The thermal cycling tests, for instance, are said to take the boards for a hot and cold cycle to check whether they are thermally and reliably stable over time or not.
Thermal Resistance Measurement
Specific measurements, such as thermal resistance (θja), quantify the thermal performance of PCBs. The thermal resistance values specify how well the board is able to dispose of the heat from components into the surrounding air. Lower thermal resistance indicates better dissipation capability for heat transfer.
VI. Applications and Industries
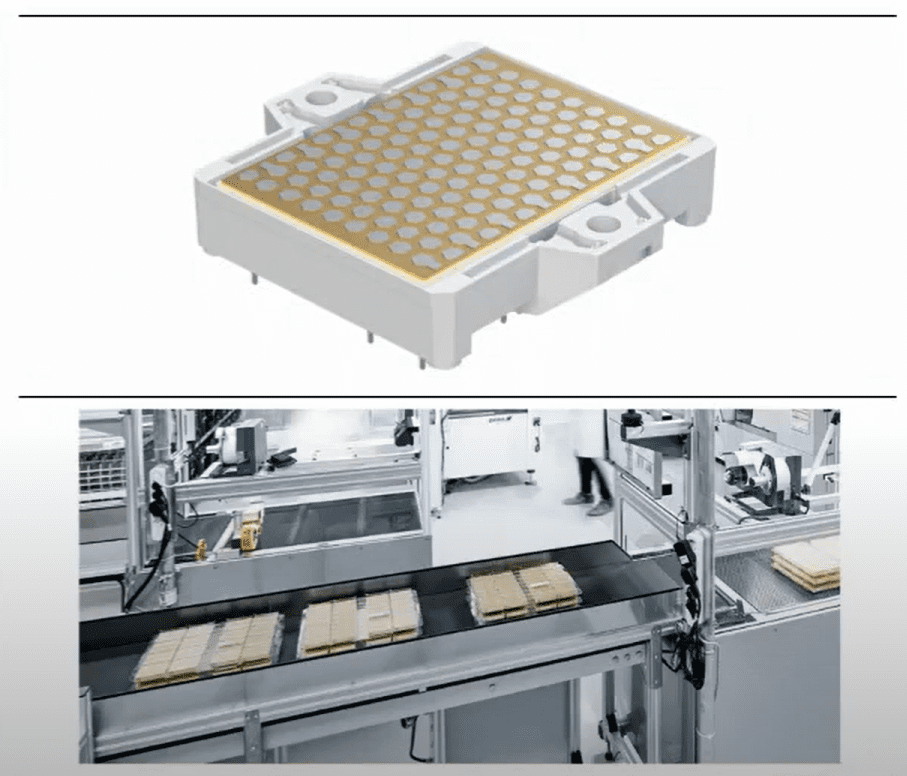
1. Automotive Industry
Advantages: Create an increase in the heat elimination systems of electric vehicles (EVs), give better reliability for the engine control units (ECUs), and ensure long life in extreme running conditions.
Applications: Developed for EVs are the electric powertrains, the battery management system (BMS), LED lighting systems, and engine control modules (ECMs).
2. Aerospace and Aviation
Advantages: improved thermal stability in avionics systems; a decrease in the risk of component failures caused by overheating; compliance with strict safety standards.
Applications: for instance, flight control systems, communication apparatus, cockpit monitors, and radars.
3. High-Power Electronics
Advantages: heat dissipation efficiency for high-power devices; extended life span of components; maintaining the low cost of the system.
Applications: power inverters, industrial automation systems, renewable energy systems (solar inverters, wind turbines), and power supplies.
VII. Future Trends and Innovations
1. Advanced Substrate Materials
In future thermal-resistance PCBs, better substrate materials such as ceramic-filled polymers, metal core laminates, and high thermal conductivity dielectrics are to be used to achieve enhanced heat dissipation and the best performance.
2. Flexible PCB and Rigid-Flex Designs
The miniaturization trend is the key to the development of thermal resistance PCBs in flexible and rigid-flex configurations, which allows efficient heat dissipation in compact applications and the optimization of thermal performance in various environments.
3. Embedded Cooling Solutions
Microfluidic channels and PCM-based cooling channels enable a breakthrough in thermal management on the PCB level and offer a way to dissipate heat and use latent heat.
4. Thermal Simulation and AI
The software that is AI-powered and uses thermal simulation is very useful in PCB design because it analyzes complex thermal dynamics, identifies hotspots, and optimizes heat dissipation strategies, which reduces the number of prototyping iterations and speeds up the time-to-market.
5. Integration with IoT and Smart Systems
Thermal resistance PCBs are applicable in IoT systems and smart systems for real-time monitoring of thermal phenomena, adaptive process management, and optimizing operation efficiency, helping to increase overall operational efficiency.
FAQs
Key Takeaways
- Thermal-retention PCBs are extremely important for high-performance application areas such as automotive, aerospace, and high-power electronics. They disperse heat well, which saves power, and they remain in good working order.
- Some of the factors that influence thermal resistance are material selection, copper thickness, layout optimization, and component placement. Taking into account the heat sinks, thermal vias, and pads, as well as optimizing the trace width and spacing, becomes one of the design considerations.
- The process of temperature testing that takes place during development helps to unearth thermal performance features.
- The applications cover automotive engine control units, aerospace avionics, and high-power electronics. The development of thermal-resistance PCBs will be a recurring theme in the future, so it can keep rewriting the rules.
Conclusion
Hence, the thermal-resistive PCB path shows that the design of PCBs must, to some extent, take thermal management into account. Through optimal thermal factors and the application of the latest techniques, designers will be able to create systems with better performance, reliability, and durability. Looking forward, this thermal management aspect will still be the secret weapon for the success of the majority of PCB design tasks, which leads to better technology and development in various fields.