Printed circuit boards (CPBS) are vital for the technology of electronic devices because they connect the elements with precision and reliability. The surface finish is another essential factor in PCB manufacturing that makes sure the circuit board itself is protected from oxidation and components will solder smoothly. Surface finish effectively improves board reliability and service life and lowers production costs.
The purpose of the following guide is to discuss different types of surface finishing of PCB, their benefits as well as drawbacks, and how to make a choice about which one is the most suitable one for your specific case.
Why do you need a surface finish on a circuit board?
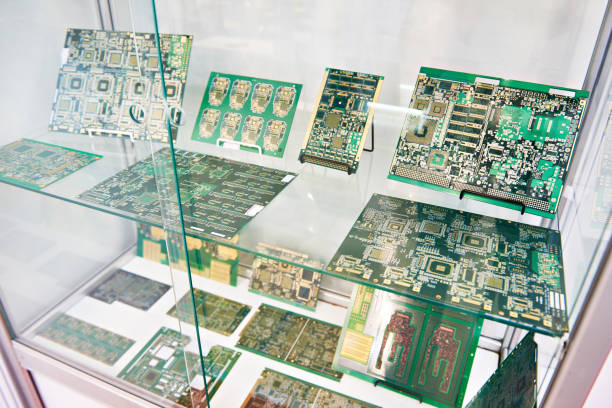
A surface finish is commonly the last finishing treatment applied on the circuit board by printing the exposed copper because if the exposed copper circuitry was not coated with a surface finish, it would oxidize and then deteriorate. The second layer, hereupon, serves as a Copper Diffusion Barrier (CDB), which provides the copper with solderability that is otherwise unavailable and ensures that the connections between the board and its components remain reliable. Besides the fact that these factors affect the electrical components performance of the board, which in turn increases the board’s endurance at the specified temperature limits, they are essential for maintaining the overall integrity and quality of electronic devices.
Types of PCB surface finishes or surface coatings and their advantages and Disadvantages
Printed Circuit Board (PCB) surface finishes are imperative components of any PCB board layout, which increases the overall consistency and performance. Each technology has its own favourable and unfavourable properties that provide the ability to be used in different applications. Here’s a brief overview of the most common PCB surface finishes:
1. Hot Air Solder Leveling (HASL)
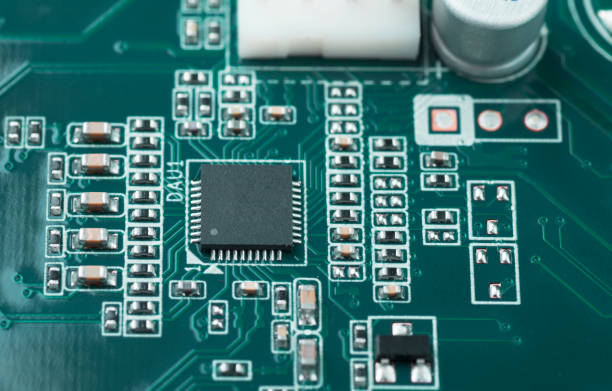
Hot air leveling, or hot air solder leveling (HASL) for short, is a method that involves a PCB board first being dipped into molten solder; excess solder is then removed using hot air blowing, which leaves an even and thin layer of solder on the surface of the PCB. This is due to its self-leveling and flux-activated resin, which enhance solderability and protect copper from oxidation.
Advantages:
- Cost-effective: HASL aerially represents some of the most affordable surface treatments utilized in manufacturing.
- Long Shelf Life: With this product’s long shelf life compare to short shelf life, it is not hard to purchase it in many categories of stores.
- Reworkable: The ease of reworking makes it a great fit for prototypes and low-volume productions, acting as a tempest for design iterations.
Disadvantages:
- Not Suitable for Fine Pitch Components: The unsymmetrical surface can therefore be a problem when you wish to place tougher, finer-shaped particles.
- Thermal stress: It is due to the PCB being exposed to high temperatures that this can lead free finish to stress.
2. Lead-Free HASL

Along with the same regularization of the environment, lead-free HASL has come to be the most frequently used platform, but the latter.
Advantages:
- Environmentally Friendly: It excludes the element of lead in the standard based on RoHS.
- Good for General Use: This makes it a viable option for multiple working spots, bearing in mind that it has a moderate introduction.
Disadvantages:
- Higher cost than HASL: slightly higher price as a result of the cost of the necessary crude.
- Thermal Stress: Its mechanism is similar to HASL, while the PCB is operated at high temperatures.
3. Electroless Nickel Immersion Gold (ENIG)
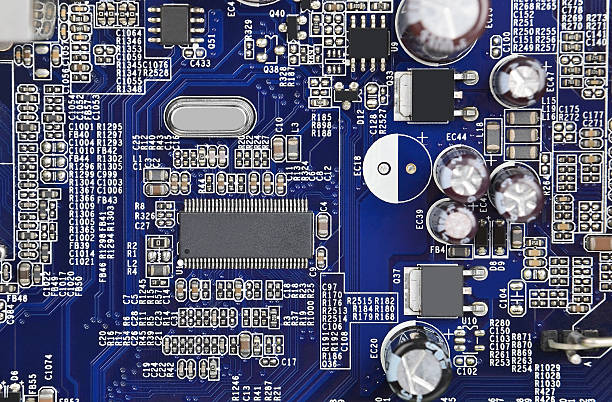
ENIG offers a level ground for collecting and preventing corrosion, which is vital in high-density part packing because of the increased potential for corrosion issues to gold layer.
Advantages:
- Excellent Surface Planarity: The best option for BGAs and FP, therefore.
- Good Oxidation Resistance: A nickel-barrier layer is in place to shield the copper under it from oxidation.
- Long Shelf Life: The use of oil-based finishes provides better storage than any alternatives.
Disadvantages:
- Cost: Costly rather than HASL and lead-free HASL.
- Black Pad Issue: Black pad syndrome, which may cause inadequate solder joints, is associated with tin-lead alloy soldering.
4. Immersion Silver
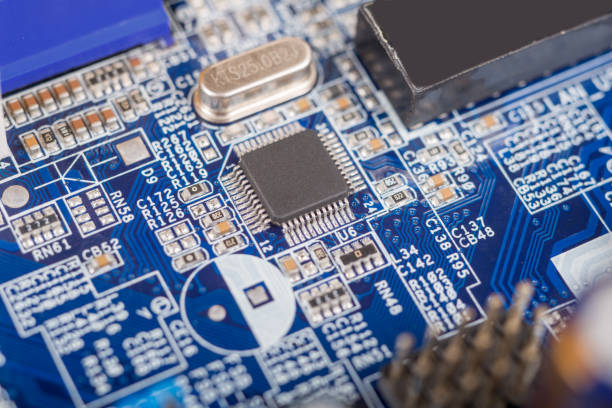
Immersion silver is a relatively simple process among finishes, with the balance between cost and quality serving as the middle ground.
Advantages:
- Good conductivity: found best in the superconducting components.
- Flat Surface: Offers a surface, simplifying the use of the fine-pitch components.
- Cost-Effective Alternative to ENIG: An ENIG alternative that is about half the price but provides the same advantages.
Disadvantages:
- Handling Sensitivity: Will shine until left in the open, or wear and tear appears if not care is taken.
- Limited Shelf Life: It is not fit for long-term storage.
5. Immersion Tin
The fame of this finish comes from its outstanding soldering ability and many designs’ applications. This is an affordable option.
Advantages:
- Excellent Solderability: This gives an ideal surface coating for operating with heat who have solderable surface.
- Cost-effective: Around the double of the cost of ENIG and four times less than immersion silver.
- Flat Surface: A noise filter is good for fine-pitch components.
Disadvantages:
- Whisker Growth: Can cause the occurrence of tin whiskers, which is a reliability challenge.
- Handling Sensitivity: It loses its shade or color intensity faster than other paint systems.
6. Organic Solderability Preservatives (OSP)
OSP is an aqueous organic material that imparts a protective coating on the copper surface until it is assembled on the board.
Advantages:
- Environmentally Friendly: Leadless and none of the heavy metals.
- Good for Fine Pitch Components: Features a completely flat surface.
- Cost-Effective: Often less expense than other surface finishes is involved.
Disadvantages:
- Limited Shelf Life and Handling Sensitivity: It requires special handling and proper storage conditions.
- No Added Thickness: Copper is used in these devices, which is a very thin material or typical thickness.
7. Electroless Nickel Electroless Palladium Immersion Gold (ENEPIG)
As the PCB surface finishes, ENEPIG provides the presence of nickel ions, palladium, and top golden layers via the immersion of copper pads into chemical solutions or copper pcb. This anti-oxidative, multi-layer film is intended to be used as a corrosive-resistant, durable, and versatile optimum solution for soldering process and wire bonding processes.
Advantages:
- suitable for integrating into multiple assembly processes.
- An ideal surface texture for wire bonding and soldering.
- Resistant to corrosion and possess a long product life.
Disadvantages:
- the most highly priced thin coating.
- Process control as a whole can be quite complex.
- Over-engineering for purposes where such high performance is not needed.
Which surface finish is better, HASL or ENIG?
The pick between hot air solder leveling (HASL) and electroless nickel immersion gold (ENIG) intensifies on account of many factors, including cost, application requirements, and specific performance levels.
Explanation:
- Cost: Among other things, HASL is often lower priced than ENIG; therefore, this kind of technology is often widely utilized for gadgets that are considered to be in the standard category.
- Solderability: HASL is very effective; however, its capabilities highly depend on its ability to create a smooth surface, which can be unpredictable. The high quality and uniformity of the ENIG film solderability are attributed to its flat and zero-perfection finish.
- Surface Flatness: HASL usually causes an irregular or uneven surfaces as it is bad for parts with fine pitches. In contrast, ENIG exhibits the peculiarity of a very flat surface, which makes it perfect for the connection of BGAs (ball grid arrays) and high-density components with high pitch accuracy.
- Lead Content: HASL is offered in both lead and no-feeding, whereas ENIG is lead-free by nature, which makes the latter more useful for applications subjected to harsh environmental requirements.
- Environmental Impact: ENIG is most often equal to or even superior to other lead-free HASL options in terms of environmental impact. In some cases, it even outperforms them.
- Shelf Life: Mixes remain the same lifetime, though it is better for enig because of its stability to oxidation.
- Suitability for Fine Pitch Components: ENİG is the right target for swift fine pitch component installation because of its superior surface structure, but HASL might not be appropriate for very fine pitch components with the unfavorable consequence of an uneven surface.
- Assembly Processes: For these operations, ENIG will be used when precision is critical and comes into play in different multilayer assembly processes. However, HASL could be the best choice if it is a simpler, less vital assembly machine.
- Reliability Issues: The various impediments of the ENIG can even get to the point of affecting the connectivity of the nickel layer, a defect known as the ‘Black Pad’ syndrome. In the aspect of reliability, HASL most often does not possess any specific issues, but it may be an issue to be reckoned with with connections in the high-density arrangements.
ENPEPIG surface finish
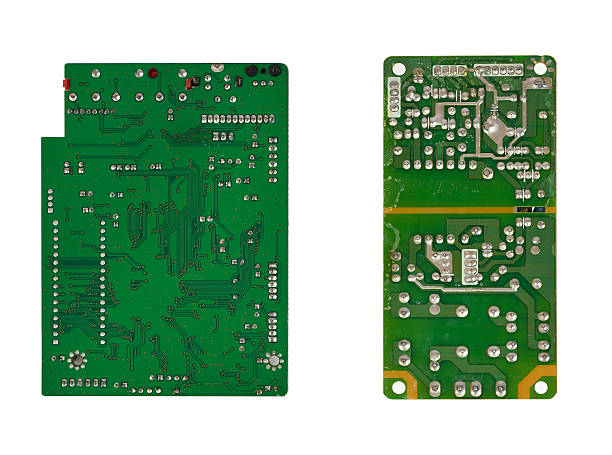
ENEPIG coating is a high-performance outer coating for PCBs. It applies to several layers on the substrate surface. The multilayer surface of contacts is three-layered, and successively, the metals are deposited onto the copper traces of the printed circuit board surface. Here’s how each layer contributes:
- Electroless Nickel (EN): This inner coating plays the role of a barrier to the copper underneath, thus protecting it from oxidizing processes. Thus, even after oxidation, when the solder is applied, the copper will not be de-solderable. It does it in a way that is solid and provides a framework for self-regulation of emotions.
- Electroless Palladium (EP): The palladium layer is also electrolessly plated over the nickel layer. This layer plays the role of a variation impeder that keeps the gold from being diffused into the nickel layer serves. It makes the finishing not only appearance but also corrosion resistance.
- Immersion Gold (IG): The top layer of gold takes the form of a thin one, which is done through immersion, which prevents gold from building up a thick layer of plating. This layer increases wear resistance and makes it possible to replace the connections by soldering them or using a wire bonding method.
Choosing the right surface finish for a board
As a surface finish for PCB, the right choice shall be made based on balancing the different factors that match bespoke attributes. Here is an organized and straightforward table that will show you all the essential things, whether it is a normal board or one made of different kinds of finishing surfaces, as well as their importance, such as agronomy, purpose, durability, and ecology.
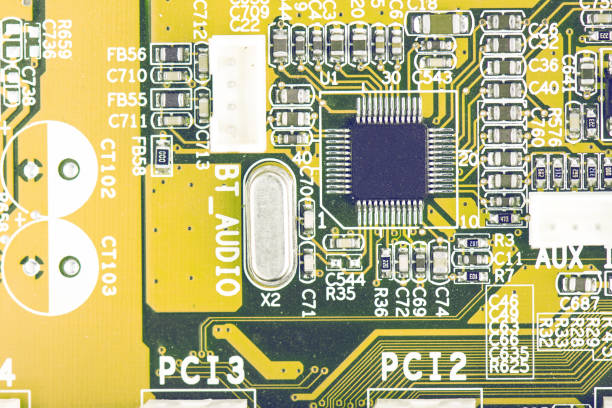
Selecting the right PCB surface finish depends on several factors:
- Assembly Processes: Look what you are going to include concerning components and soldering processes.
- Environmental Conditions: Conduct an assessment of the PCB operation.
- Cost Considerations: Make out your budget requirements clearly.
- Regulatory Requirements:Ensure that the organization complies with environmental laws.
This should be the table that will help you match your particular requirements with the qualities of each surface finish so that you can make up your mind and finally choose a PCB surface finish for your design and manufacturing needs.
What PCB surface finish do you most commonly use (PIE CHART)?
Here is a pie chart pretty much picturizing the approximately existing mutual PCB surface finishes being used in the industry. The graphic is displayed in a way that the reader grasps, for example, how different finishes are preferred depending on such factors as cost, construction, or environmental requirements.
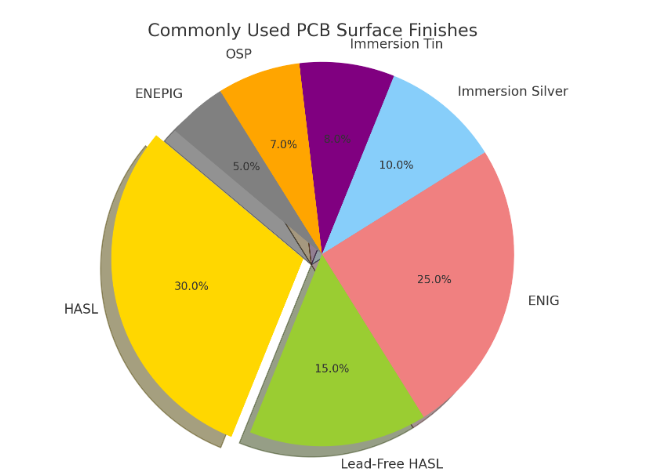
- Hot Air Solder Leveling (HASL): 30% – The effectiveness of this medicine in treating cancerous cells has been extensively studied and used for many years.
- Lead-Free HASL: 15%: Not only the eco-friendliness of products but also the growing demand in industries is driving the industry towards lead-free products.
- Electroless Nickel Immersion Gold (ENIG): 25%: This material was often used for its superior solderability and flat surface, which are good for the fine-pitch technology in enig surface finishes.
- Immersion Silver: 10%: It chose the product of high performance because it is a good performer.
Hypothetical pie chart for 2024, reflecting the possible trends in the usage of PCB surface finishes based on industry shifts towards more environmentally friendly and high-performance options:
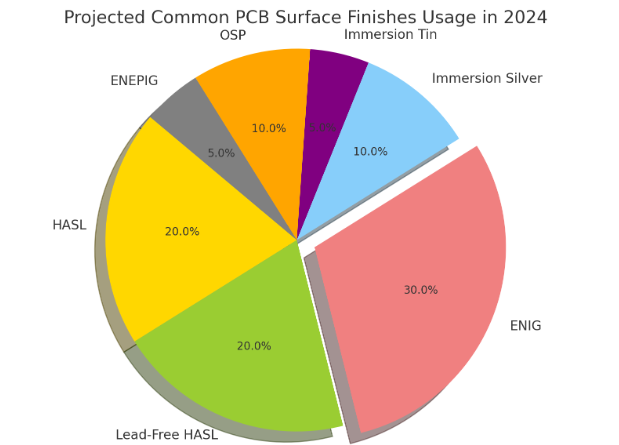
- ENIG (Electroless Nickel Immersion Gold): Growth in its usability could be due to its reliability and applicability to the design of complicated, crowded boards.
- Lead-Free HASL: Furthermore, electric vehicles remain in demand as they are considered to be cheap and nature-friendly.
- Immersion Silver and Tin: The unit could be used for narrow purposes such as linear and high-dot-pitch solutions.
- OSP (Organic Solderability Preservatives): This could be more successful as it’s the most environmentally friendly choice.
- ENEPIG (Electroless Nickel Electroless Palladium Immersion Gold): Its usage may look more expensive, but due to its high performance in multiple projects, it can still gain wider proper use.
Characteristics of common surface treatment methods
Several top-trending surface finishing processes for printed circuit boards (PCBs) have different features that allow the application of the method to suit different application types. Below are descriptions of several widely used PCB surface treatment methods:
Hot Air Solder Leveling (HASL):
- Characteristics: It entails the process where the PCB plunges into melt solder and then is removed from there using hot air knives to achieve the covering.
Lead-Free HASL:
- Characteristics: Like the other type of HASL, it uses a no-lead solder alloy as well due to the environmental laws passed.
Electroless Nickel Immersion Gold (ENIG):
- Characteristics: A nickel coating applied chemically follows the thin golden layer and gold plating.
Immersion Silver:
- Characteristics: A straightforward chemical displacement reaction that deposits a silver coating, made up of nanosized grains, onto the copper surfaces involved
Immersion Tin:
- Characteristics: By means of a chemical process reaction tin stratifies thin film on the copper surface.
Organic Solderability Preservative (OSP):
- Characteristics: A water-based organic compound that is composed of copper inhibits its reaction until soldering.
Electroless Nickel Electroless Palladium Immersion Gold (ENEPIG):
- Characteristics: The solution to this problem is a three-layer coating made of nickel, palladium, and gold, electrochemically applied to the surface or non electrolytic chemical finish.
CONCLUSION
The PCB finish surface selection is the core of PCB production, in which the operational life span and the completed product success of the electronic device are highly relevant. Due to the cosmetic nature of each of the finishes, they offer some unique benefits, although they also come at some cost, which makes the decision process quite a dilemma and highly dependent on the needs of your application.
HASL process, whether this is with a lead component or is lead-free, might offer a more economical way of getting a sufficient degree of performance that isn’t too expensive. But if the application stipulates high-density component assembly, ENIG (Electroless Ni-Gold) or Immersion Silver, which give finer pitch and reliability, could be preferable in these cases. On the flip side, the best build and satellite-level applications requiring the highest environmental compliance and vital connections may opt for the more costly ENEPIG choice.